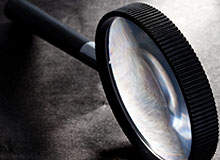
In January 2008, Saudi Aramco opened the Drilling and Workover Real-Time Operation Center (RTOC), a state-of-the-art well realtime monitoring command centre, to plan, drill and complete wells in the safest, efficient and cost-effective manner. Three phases were devised to meet drilling management expectations.
In phase I, the initial RTOC objective was to focus on critical wells, mainly offshore, to reduce the occurrence of tight hole, stuck pipe, borehole collapse, sidetracked bottomhole assemblies (BHA) and borehole instability problems. Phase II involved improving drilling optimisation and efficiency for the monitored wells. One of the techniques used was to implement mechanical specific energy (MSE) to optimise drilling parameters. Another goal in this phase was to reduce the non-productive time (NPT) for the monitored wells by monitoring rig activity. During phase III, the RTOC might recommend the bit selection to increase rate of penetration (RoP).
Another target is to optimise hydraulics, hole cleaning and equivalent circulating density (ECD) for extended reach drilling(ERD) wells, BHA design, monitor drill string mechanics and BHAs to prevent damage and reduce well control incidents.
RTOC equipment
The RTOC consists of a main room equipped with computers that are connected to large screens on the wall to display the monitored wells’ real-time data. One collaborative room for daily meetings is equipped with plasma screens and a PC, while another has video-conferencing tools to communicate with other teams in the company and the outside world as needed.
See Also:
The team starts by collecting and preparing required data from various sources, including both surface and downhole tools. By using different tools and mechanisms, it predicts the wellbore stability and monitors it in real time, automatically generates targets and optimises platform placement.
How well do you really know your competitors?
Access the most comprehensive Company Profiles on the market, powered by GlobalData. Save hours of research. Gain competitive edge.
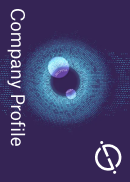
Thank you!
Your download email will arrive shortly
Not ready to buy yet? Download a free sample
We are confident about the unique quality of our Company Profiles. However, we want you to make the most beneficial decision for your business, so we offer a free sample that you can download by submitting the below form
By GlobalDataCommunication using phone calls and embedded chat sessions assists in better and faster decisions, and key performance indicators (KPI) are used to monitor the RTOC’s results and to follow-up on what was achieved. Alerts are classified into two levels: low and high. Examples of low-level alerts include: loss of real-time data, weight on bit (WoB) deviations, reaming of stands while drilling, overpull while reaming, connection gas, low circulating time prior to pulling out of hole (PooH), low circulating rate to achieve hole cleaning, change in torque and drag trends, variation in expected hook load while running casing and deviations from programme/procedures. High-level alerts are for problems that require an immediate response.
Examples include: sudden drop or increase in standpipe pressure, sudden loss of string weight, flow-out rate variations, alarms (washout, kick, loss circulation), erratic or sudden increase in torque while drilling, high over-pulls while picking up on connections, high over-pulls while PooH, and a sudden increase in drag while tripping pipe or casing and stuck pipe.
IT infrastructure
Saudi Aramco uses different service organisations to deliver its global drilling and completions (D&C) agenda. Applying a common approach to information access on a global basis has enabled it to streamline its operations and make wider use of emerging analysis, monitoring and collaboration technologies. In early 2007, the company implemented new data architecture for real-time D&C information.
As well as enabling Saudi Aramco to make wider use of its monitoring and collaboration centres, it also enabled it to leverage the evolving Well Site Information Transfer Standard Markup Language (WITSML) standard more effectively in drilling operations.
The WITSML is a continually developing industry standard for the transmission of real-time, historical and contextual drilling and completions information. It is managed by Energistics, the energy standards resource centre. Saudi Aramco is a contributing member of Energistics and has also been a member of the drilling WITSML Special Interest Group (SIG) since January 2008. It is the most active user of the WITSML standard worldwide.
The tools RTOC uses come from a range of different providers, and vary from downhole parameters measuring while drilling/logging while drilling (MWD/LWD) tools to surface parameter tools. They are unmanned and just need to be set up at the beginning of the job and are based on WITSML standards. Data is collected from different rigs and sorted in Saudi Aramco’s drilling real-time data hub (DRTDH).
Real-time technologies were used to capture, monitor and analyse drilling data from rig sites so that critical decisions can be made in real-time to help reduce and eliminate borehole problems, thereby reducing NPT. The RTOC runs a complete geo-pressure and geo-mechanics solution that improves drilling success. It includes all the tools needed to achieve new levels of risk reduction, cost savings and drilling performance, such as leading geo-pressure analysis, 3D visualisation and analysis, seismic velocity correction, seal integrity and compartment analysis, uncertainty analysis, and fully integrated wellbore stability analysis.
Mechanical-specific energy
Real-time MSE surveillance provides calculations to monitor changes in the efficiency of the drilling operation by measuring the calculated work that is being performed to destroy a given volume of rock. An MSE calculation helps to identify the best drilling parameters and justify any design changes, such as bit selection, BHA design, mark-uptorque, directional target sizing and motor differential ratings. The MSE depends on the fact that the input energy from the rig (RPM, WoB, torque and pump pressure) is equivalent to the output energy (vibration and RoP). Vibration must be minimised to optimise the RoP.
The following equation has been defined to calculate MSE: To make analysis more accurate, Saudi Aramco has chosen to calculate >and display the adjusted MSE by including an efficiency factor: where EFF = 0.35 (efficiency factor).
To use real-time MSE, the company has collected drilling parameters from the subject well and reference data from offset wells. For efficient MSE utilisation, a dedicated analysing team to achieve continuous RoP optimisation in real time is required. In addition, comprehensive training is given to rig supervisors/rig foremen, drilling engineers and bit specialists on how to achieve optimised MSE.
The company applies optimal drilling parameters to collect realistic MSE data and trend on two pilot wells for each lithological formation. The recommended parameters are passed to the bit specialist to apply them at the well site while drilling.
During the drilling operation, the MSE from recommended drilling parameters are recorded for future MSE analysis against recommended drilling parameters for the next well(s). Meanwhile, work is in progress to implement advanced real-time modelling, diagnosis, visualisation and simulation systems. The systems will use real-time data acquired from surface and downhole sensors to simulate the drilling activities through 3D interactive visualisation techniques. The systems will assist the engineers in looking forward to downhole problems, provide recommendations and develop scenarios while drilling to avoid operational risks, and speed up drilling.
Measuring RTOC value
A system was developed to help the RTOC management in defining and measuring progress towards reducing NPT, optimising drilling operations and to improving safety in drilling activities. So far the RTOC team has identified the following KPIs to be calculated:
- average total operation time and average total lost time in RTOC verus non-RTOC wells in the same field
- percentage of wells that had specific trouble (for example, stuck pipe) per year
- percentage of drilling troubles per field
- total lost time per operation code
- compare how many feet per day were drilled in the RTOC and non-RTOC wells.
It has been calculated that the cost of the centre was recouped in the first six months of operation. Also, a total of 90% of stuck pipe issues were monitored and prevented. Further RTOC statistics, reported in August 2009, include:
- Total monitored sections =232
- Total alerts raised = 115
- Total recommendations = 335
Improving performance
There are several solutions to the challenges faced by the RTOC:
- Aggressive technical marketing of the RTOC is needed. Many drilling engineers are not aware of what the RTOC can provide. Training sessions have been held for drilling engineers and rig foremen to overcome this challenge.
- Enforce data analysis every 12 hours per shift to determine an independent technical critique of drilling activities, and to make recommendations to the drillers offshore on how to respond when parameters change to ensure wellbore viability and bring forward practices worth replicating to the next phase of execution.
- Use of the processes and procedures on monitored wells, such as using a traffic light system for the monitored rigs. Green means the RTOC is tracking the well, amber means slight deviation from the plan executed and red means stop operations. This is to ensure the interaction between the rig and the RTOC follow clear protocol.
- Improve collaboration with the Geosteering Operation Center, petrophysics and senior well engineers. There are initiatives to implement a collaborative environment between the two centres.
- Automate rig activity detection, and to optimise and award merit-based bonuses to enhance rig activity. This is needed to monitor NPT/invisible lost time and to create best practices and lessons learned.
Future plans including implementing an interactive applications dashboard for drilling applications. The system is a business and operations management dashboard platform that can be customisable for user roles (such as command centre manager, drilling supervisor, drilling engineer, geologist, geo-steering supervisor) or departmental functions (for example, drilling geo-steering, IT).
Overhauling the Saudi Aramco Drilling Knowledgebase (SADK) framework to encompass real-time, drilling simulation and planning data in addition to the existing operation data is also on the agenda. The reports will be interactively driven by the planning data and real-time data updates. SADK was developed five years ago and has been growing ever since. It is time now to build a new framework to capitalise on the introduction of new workflows as realtime data gathering and automation of drilling programmes