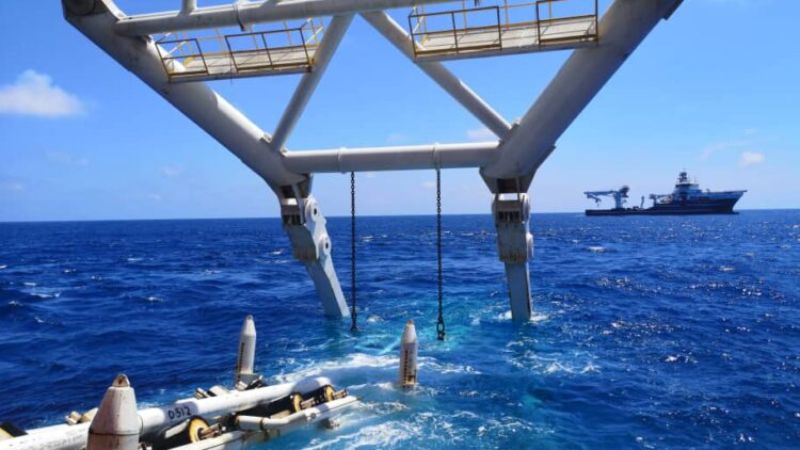
Cortez Subsea has completed a subsea pipeline installation project using the NOV-Tuboscope Zap-Lok mechanical connector.
Carried out in offshore Malaysia, the project was completed in partnership with Alam Maritim.
According to the company, the usage of the new technology allowed for faster and cheaper completion of subsea pipelay compared to conventional welded pipelay process.
It recorded the best average lay rate of 4.7km in 24 hours with the rigid pipelay section completed within 20 days.
The pipeline system was developed specifically for the Tembikai Non-Associated Gas (TNAG) Development by Vestigo Petroleum, a subsidiary of PETRONAS Carigali.
The system utilises NOV-Tuboscope Zap-Lok connectors to connect the rigid pipeline through diverless connections.
How well do you really know your competitors?
Access the most comprehensive Company Profiles on the market, powered by GlobalData. Save hours of research. Gain competitive edge.
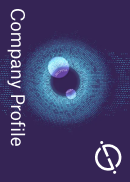
Thank you!
Your download email will arrive shortly
Not ready to buy yet? Download a free sample
We are confident about the unique quality of our Company Profiles. However, we want you to make the most beneficial decision for your business, so we offer a free sample that you can download by submitting the below form
By GlobalDataCortez Subsea managing director Alasdair Cowie said: “We championed the Zap-Lok mechanical interference connector as a weld-free alternative to traditional pipelay. This is the first time this technology, which is much faster and more efficient, has been used offshore Malaysia.
“In another industry first, the rigid pipe was connected to flexible risers using a Stinger Deployed Diverless Connector (SDDC), which we brought to the market in partnership with AFGlobal. Using a Remotely Operated Vehicle (ROV) and a deployment frame, the connection is made from the pipeline to the host facility without the use of divers.
“A complete diverless approach reduces cost and increases safety for the team offshore. This mechanical alternative to welding results in a safer work environment, which is free from hot-work and radiography.”
The company was contracted for the engineering, procurement, construction, installation and pre-commissioning of the pipeline system.