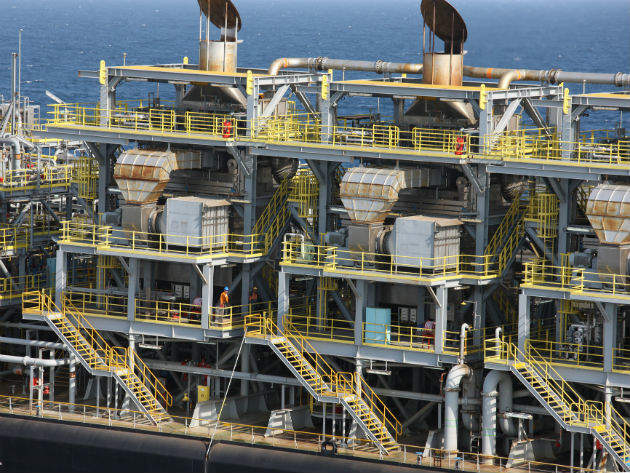
Offshore oil rigs are often located in dangerous and isolated areas, and their engineering and construction must be of the upmost quality to protect the platform and its crew from the elements. One undoubted threat to their security comes from earthquakes, as seismic movements can cause untold damage to unprepared rigs.
Oil and gas company OMV was recently forced to shut one of its rigs in the Maari oilfield offshore Taranaki, New Zealand after the discovery of a crack below the water level. This crack may have been at least in part cause by the large earthquake which had recently hit the surrounding area.
The announcement of the rig’s closure raises a question: how you can earthquake-proof a rig? To find the answer, we take a look at new seismic technologies being implemented around the world, including at the Sakhalin project in the Sea of Okhotsk, one of the most seismically active areas on earth.
The Maari crack
Following routine checks starting on 1 November last year, a crack was discovered on an OMV rig in the Maari oilfield and the platform was immediately shut down. All 34 staff were helicoptered off the platform. OMV insisted that the crack didn’t pose a threat to either staff or the environment, stating that abandoning the rig was just a precautionary measure due to bad weather expected to hit the platform soon after its discovery.
The 1.4m crack occurred in just one of the twelve underwater struts that support the rig. Shortly after it was discovered an OMV spokesman stated that "the crack was caused by fatigue on level 3, exactly where the wave and wind pressure is greatest". However, it has also been suggested that the crack could have been caused or exacerbated by the 7.8 magnitude earthquake which hit the area around midnight on 14 November.
See Also:
OMV has said it is impossible to determine whether the crack was even in part caused by the earthquake. The implications of the earthquake’s effect on the Maari oilfield, however, could be massive. New Zealand lies on the boundary of the Australian Plate and the Pacific Plate, along which a large amount of faults (including the Wellington fault which lies close to the oilfield) make the area prone to earthquakes.
How well do you really know your competitors?
Access the most comprehensive Company Profiles on the market, powered by GlobalData. Save hours of research. Gain competitive edge.
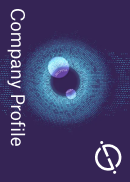
Thank you!
Your download email will arrive shortly
Not ready to buy yet? Download a free sample
We are confident about the unique quality of our Company Profiles. However, we want you to make the most beneficial decision for your business, so we offer a free sample that you can download by submitting the below form
By GlobalDataWhilst the Kaikoura earthquake of last November was particularly large, the Maari oilfield must be able to withstand quakes of this magnitude. Thankfully no damage was caused by the cracked strut this time, and workers returned to the platform in January following reinforcement of the strut by three supports.
Always on shaky ground
The Maari field is not the only one located within an earthquake-prone area; many other platforms are also situated near faults. One example is the Sakhalin project off the east coast of Russia. Around 20% of Russia is prone to earthquakes, 5% of which is territory where earthquakes are expected to reach a destructive magnitude of between 8.0 and 9.0. The Sakhalin project run by Sakhalin Energy Investment Company (SEIC) and owned by Gazprom, Shell, Mitsui and Mitsubishi, is located in one such area.
An earthquake could potentially devastate a rig like the three in the Sakhalin project. It would put the lives of the crew in danger, as well as the surrounding environment. If a quake was significantly strong and the rig significantly unprepared, the rig could collapse, releasing vast amounts of oil or gas which would pollute the surrounding seas and could also fuel fires that would ravage the site.
It has been paramount since the construction of the Sakhalin project, one of the largest combined oil and gas fields in the world, that the three platforms just off the coast of Sakhalin Island can withstand potential earthquakes. “Sakhalin sits in the middle of an active seismic zone and as a result we have had to safeguard the three platforms in the Sea of Okhotsk from this danger,” a Shell spokesperson says.
Protective measures at Sakhalin
The Sakhalin project was engineered and constructed taking earthquakes and ice into account. All three of the platforms use structures which have seen success in the construction of bridges and public building on land, such as San Francisco’s Oakland Bay Bridge and Istanbul’s Ataturk Airport. The platforms, Piltun-A (PA-A), Lunskoye-A (Lun-A), and Piltun-Astokhskoye-B (PA-B), use two different techniques to withstand earthquakes.
PA-A, the oldest of the three platforms, was built in 2008 and services 13 oil production wells, four water injection wells, one gas reinjection well and one waste disposal well. “[Piltun-A] is based on a sand-filled caisson that anchors it to the seabed,” says the Shell spokesperson. “Bearing pads between the caisson and the platform’s deck structure allow the deck to move somewhat with respect to the caisson, protecting it from the jolts of earthquakes.”
The other two platforms, Lun-A and PA-B, were constructed using a different method of earthquake-proofing. “The other two platforms are built on massive concrete legs – each wider than 20 metres,” Shell’s spokesperson says. “These concrete structures were both constructed in Russia, near Vladivostok. They are extra thick to help withstand not only the pressure of ice but also the shaking of earthquakes. They also feature an earthquake-protection mechanism that had never before been used offshore: friction pendulum bearings.”
Friction pendulum bearings are being applied all over the world to protect structures from earthquakes. “A friction pendulum bearing is basically a bearing pad with a smooth, concave surface,” the Shell spokesperson explains. “During an earthquake, the supported structure is free to slide on the concave surface, both horizontally and vertically. The force needed to move the structure upwards limits the horizontal forces that would otherwise cause deformations.”
“At Sakhalin the friction pendulum bearings sit atop each of the four legs of the two concrete-based platforms,” the Shell spokesperson continues. “They support topside steel decks. And they were the largest load-carrying seismic isolation bearings ever manufactured when installed.”
Proven protection?
So far the technology has proved effective at the Sakhalin rigs, protecting them against numerous earthquakes. At the time of writing, two earthquakes have hit the area in the last month alone, both over 4.0 in magnitude. As well as the seemingly constant small earthquakes, the platforms have successfully withstood much larger quakes including one measuring 8.2 which hit the region in 2013. Already the technology has proved itself capable of protecting rigs from quakes even stronger than that suggested to have damage of the Maari platform.
The two platforms mark a $20bn investment by SEIC. But it saved an estimated $300m in the construction of the two platforms by using the bearings as opposed to other techniques. The bearings should keep the platforms elastic in their responses to earthquakes for 200 years. Not only have they proved effective at protecting the platforms from seismic activity but also from moving ice and waves.
The friction pendulum bearings for the Sakhalin platforms were not only the largest ever constructed, but also the first of their kind to be used offshore. The technology therefore remains relatively untested in a range of environments with similar challenges, and whether it continues to be the most effective choice for earthquake-proofing will remain to be seen.
Whether or not the Maari oilfield platform was damaged by the earthquake, preparation for seismic activity is paramount to the safety of offshore fields in regions with high seismic activity. The Sakhalin project has proved successful in its application of friction pendulum bearings in particular, a technology which looks set to be more frequently used as offshore operators continue to consider earthquake-proofing as a key part of platform design.