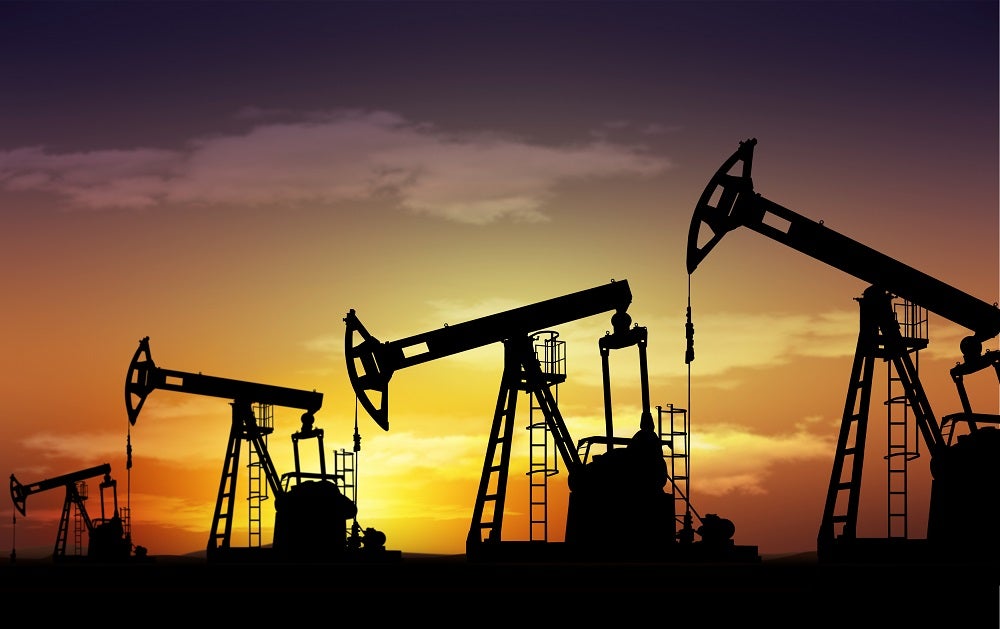
The oil & gas industry remains a fundamental industry for economies around the world, with cables and connectors essential components in operations.
With the increase in global demand for petroleum and related products, the need for exploration and uninterrupted supply is crucial for numerous industries. According to the Organization of the Petroleum Exporting Countries (OPEC), the world oil demand in 2023 will rise by 2.33 million barrels per day (bpd).
In the face of such growth, there is a need for durable, explosion-proof connectivity solutions in oil & gas operations that are reliable and can withstand extreme offshore environments.
Connectors for oil & gas operations
The connectors for oil reserve monitoring sensors must provide long-term performance at elevated temperatures in harsh environments. They are an integral part of the equipment used for land or offshore drilling, seismic evaluation, or geophysical and infrastructure maintenance.
As petroleum exploration enters remote landscapes, investing in high-quality interconnecting products is crucial. Petroleum operations such as drilling, completion of production wells, transportation to refineries and distribution networks depend on sturdy cables and connectors.
When it comes to offshore environments, Matt Steele, key account manager at Omnetics, says: “Failure is not an option for this market. Time is money. If your product causes a failure while the tool is downhole, they must remove all of the pipe to remove the tool and replace the tool. This is not a quick process and the downtime is very costly.”
A suitable cable design can tackle the challenges of electromagnetic interference and crosstalk. The signal integrity of a cable is vital during explorative operations to avoid radio frequency and triboelectric noise interference.
Chemical resistance and a high flex-life depend on the material of the cable. The gear should be able to withstand corrosive elements and high temperatures. Temperatures can reach 200°C or higher in these operating environments. Therefore, insulation and conductor materials must be rated accordingly.
Alongside robustness, the product should be durable to carry out the operations seamlessly, as any failure can result in severe delays in production and cause costs to spiral. Devices such as backshells, strain reliefs, braided shields and special cables are essential for uninterrupted petroleum operations.
Technical solutions for complex offshore installations
To meet highly specific demands, miniature connectors and cable assemblies can fulfil all the functional considerations in a sector where speed, safety, and efficiency are of paramount importance.
Most modern connector designs and materials require smaller dimensions, rugged superiority, and extreme reliability to meet the demands petroleum electronics sector. However, these smaller connectors may be more susceptible to signal interference and crosstalk. Therefore, it is essential to opt for manufacturers that provide solutions capable of performing in challenging environments. In such harsh scenarios, durable miniature connectivity and cable solutions by Omnetics are well-suited for these operations.
The company tests its cables and connectors to ensure they can withstand extreme conditions. “Omnetics connectors are designed and built to meet or exceed the requirements of MIL-DTL-32139 and MIL-DTL-83513. Meeting the qualification requirements of these two specs allows for the highest performance through high shock and vibration applications, as well as extreme environmental use,” says Steele.
Omnetics specialises in manufacturing and designing high-quality miniature connectors and cables. The company’s connectors are crucial in petrochemical operations where minimising size and weight are essential to the function. Many connectors from Omnetics can operate at high temperatures of 200°C.
The Omnetics Nano–Rectangular Design connector at a .025in pitch can be populated by up to 91 contacts with a current rating of up to 1 Amp. There is also a Micro–Rectangular Design at a .050in pitch that allows 100 contacts and a current rating of up to 3 Amp.
In addition, Omnetics manufactures the Metal Circular Connector Series, which is available in micro and nano versions. This custom cable is designed for the intense demands of petroleum electronics. With a sophisticated EMI Cable Shield to Shell Design, the pin count for both the micro and the nano is up to 39 positions.
From shales to deep water and more, operations may have specific requirements where no existing solution is available. To meet this exact need, Omnetics also supplies customised connector and cable solutions for oil & gas operations.