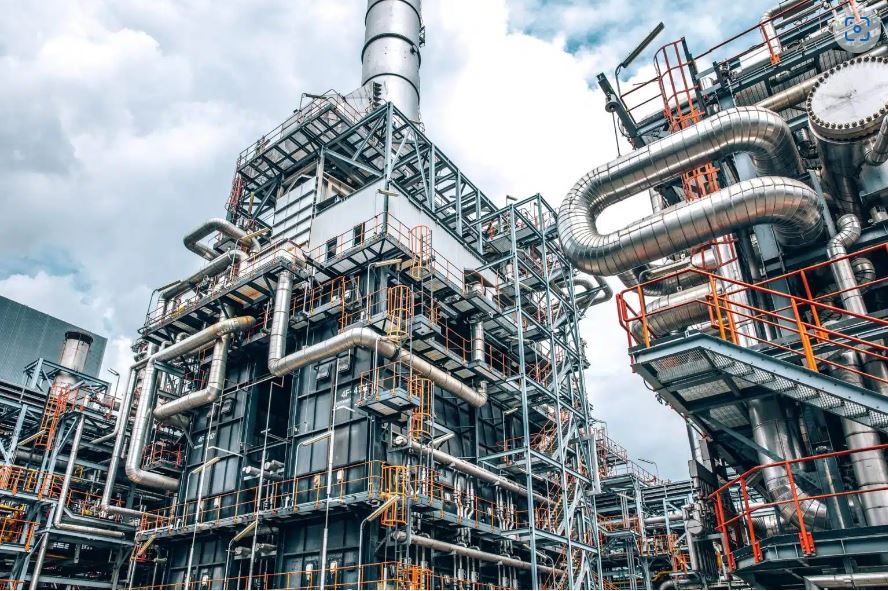
Introduction
Steam Crackers play a crucial role in various industries, ensuring the efficient production of ethylene and propylene. In this blog, we will discuss the mechanics of these furnaces, exploring their temperature requirements, cracking process, and the significance of the convection section. By optimizing the operation of ethylene furnaces, industries can enhance productivity while minimising issues such as tube coking and lost production.
Temperature control and the cracking process
To achieve the correct cracking of hydrocarbons, ethylene furnaces maintain a temperature of approximately 1470-1600F (800-870°C). A narrow band of temperature range is vital for successful cracking. The reactions involved are endothermic, demanding a substantial amount of energy. However, due to the exceptionally fast cracking process, the light feed must be exposed to this intense heat for only milliseconds, allowing conversion to ethylene and propylene without promoting coke formation.
The role of the convection section
The convection section serves as the vital pre-heat mechanism in ethylene furnaces, ensuring the correct temperature range is achieved. Deviating from this range can lead to inefficiency and limited conversion if the temperature is too cold or excessive coke formation if it becomes too hot. Maintaining an optimal flow rate is equally important to prevent overheating the product and generating coke.
Consequences of fouled convection sections
When fouling occurs in the convection section, heat transfer becomes limited, resulting in an inefficient pre-heat process. To compensate, additional firing and fuel consumption are required to reach the desired temperature. This has a knock-on effect and overheats the radiant section, leading to potential complications. Ethylene furnaces are typically designed with a turndown range, normally down to 80% of the design throughput rate, allowing them to operate smoothly. However, when the convection section is fouled, it may be necessary to reduce the flow rate below the turndown range, which can cause tube coking and reduced production.
Conclusion
Optimising the performance of ethylene furnaces is critical for industries aiming to achieve maximum efficiency in ethylene and propylene production. By maintaining the correct temperature range, monitoring flow rates, and mitigating fouling issues in the convection section, facilities can ensure smooth operations, enhance safety, and minimise downtime, ultimately elevating their overall production output.