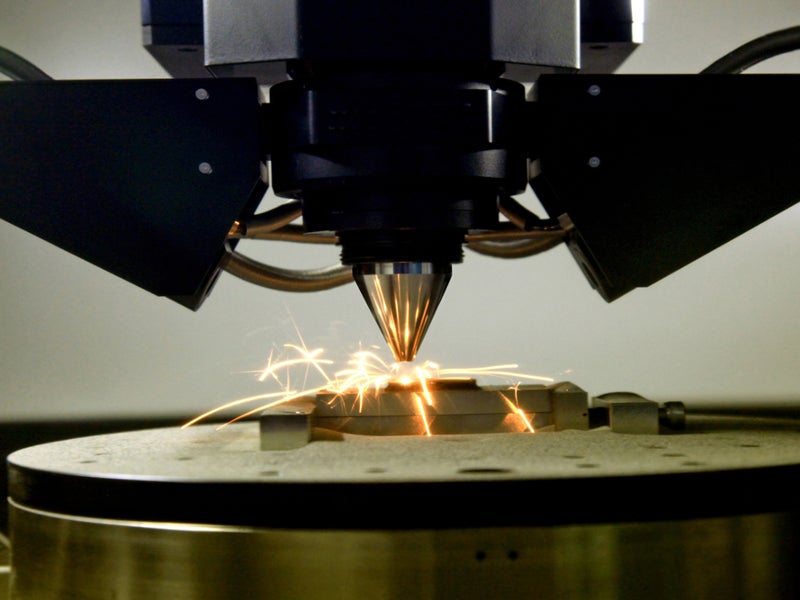
3D printing has tremendous potential in the oil and gas industry in delivering productivity gains, according to GlobalData. It is expected to gain further market penetration and find new use cases with greater collaboration between industry and technology players in developing more purpose-built 3D printing materials and solutions.
Here are the key technology trends impacting the 3D printing industry, as identified by GlobalData.
From prototyping to digital manufacturing
The mindset around 3D printing is shifting and there is an aspiration to change the terminology to move beyond prototyping and think in terms of bigger volumes. The disruption in value chain means wider thinking, more in terms of digital manufacturing than 3D printing. Also, the wider idea of digitally manufacturing parts–say, for the automotive marketplace–offers potentially much greater commercial success.
Sustainability
The global focus on climate change and global warming are driving a greater sustainability focus, based on the idea of creating a circular economy around 3D printing, instead of a linear one (where the mindset is typically one of ‘take; make, and dispose’).
It means keeping materials in use for the longest period of time at their highest available value. By utilising changes in design –and cutting out unnecessary parts –the weight of parts created can be reduced by over 93% in some cases, meaning a reduction in carbon footprint of up to 95%.
Materials
The entry of several chemical companies into the 3D printing market is helping drive the use of new innovative materials and compounds. Those companies include BASF, which is supplying its Ultracur3D ST 45urethane resin to Paxis and its Ultrasint PA6 (polyamide 6) powder to start-up, Impossible Objects.
How well do you really know your competitors?
Access the most comprehensive Company Profiles on the market, powered by GlobalData. Save hours of research. Gain competitive edge.
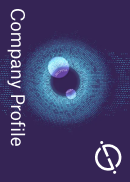
Thank you!
Your download email will arrive shortly
Not ready to buy yet? Download a free sample
We are confident about the unique quality of our Company Profiles. However, we want you to make the most beneficial decision for your business, so we offer a free sample that you can download by submitting the below form
By GlobalDataOther materials currently in use include glass fibre and diamond-based polymer composites, not to mention plastic powders, plastic filaments, photopolymers, hydrogel, metals, ceramics, and biomaterials, including hydrogel tissue-derived bio-ink, and synthetic and biodegradable polymers. Early in 2019, T&R Biofab registered a patent for its 3D bioprinting technology to create artificial skin. The technology operates through the 3D printing of dermal (inner skin layers) and epidermal (outer skin layers) cells that uses a porous 3D structure to form skin with similar characteristics to actual human tissue.
Digital twins
Digital twins is a concept from the Industrial Internet that is now being adopted for 3D printing. NASA first used the idea of digital representations of physical objects for its space projects. It was not able to see and monitor systems physically because they were too far away, so it created digital models to simulate and analyse the systems back on Earth. In the Industrial Internet, a digital twin provides a holistic view of the capabilities of an asset and so can help orchestrate, manipulate, or program certain aspects of an Industrial Internet device.
In 3D printing, digital twins’ advanced analytics enable organisations to be able to close the loop between a digital production plan and its actual performance. Siemens’ MindSphere software interrogates an Industrial Internet data pool to feed insights back into the digital twin of a multi-jet fusion process, thus enabling an organisation to troubleshoot what happens before and after printing with equipment, material flow, and worker performance. That means being able to better optimise processes for future projects and provide feedback into design and engineering.
Design benefits
One of the benefits of 3D printing is the greater design freedom it enables, with a continual iterative process reducing components, weight, and, ultimately, manufacturing cost. While previously designs developed for conventional manufacturing were hampered by manufacturing processes that required the creation of separate components assembled to create the end product, 3D printing has the potential to remove many of the constraints of the traditional manufacturing process. With 3D printing, there is also no additional cost to creating a complex design.
Unshackled from traditional manufacturing constraints, designers will be able to create geometries that better achieve their desired performance and meet customer needs. GE took advantage of this freedom to redesign the LEAP jet engine nozzle from 18 separate components to a single part. This decreased the product’s weight and increased its performance with complex internal pathways.
The appliance of science
The science around 3D printing, particularly metal, is still developing. At the same time, the process of 3D printing is opening up new possibilities in other scientific areas. A recently 3D printed model of a lung-mimicking air sac was created, complete with functioning airways capable of delivering oxygen to surrounding blood vessels. It was made by a team of researchers in the US by gradually building up layers of hydrogel, a synthetic, jelly-like material that shares many features in common with human tissue.
The same approach could be used to create complex vascular networks that mimic the body’s natural passageways for blood and other vital fluids, thus opening up the possibility of creating a new means of bioprinting human organs for transplant. Work is now underway in the US involving several universities, including Rice University, and Massachusetts design firm Nervous System. Previously, one of the biggest barriers to generating functional tissue replacements was an inability to print the complex vasculature that can supply nutrients to densely populated human tissues.
Partnerships
The need to better understand the industrial automation and materials world is driving more partnerships. HP, for example, is keen to learn from Siemens’ industrial automation expertise and BASF’s 3D printing materials specialism. It is also working closely with GKN in the same materials arena. Other alliances include Stratasys with Solvay, BASF with Impossible Objects, and French chemicals company Arkema with Carbon.
Specialist applications
Some argue that the future for the industry is not so much in technology but in applications and that is what will attract and keep the attention of investors. Materialise’s chief executive Fried Vancraen has suggested that investments are not going to machine manufacturers anymore but to companies and start-ups that apply 3D printing technology to create added value in specific domains. He believes creation and stimulation of user demand is what will accelerate 3D printing further.
Asia is a fast-growing market for 3D printing and governments that might previously have invested in 3D machine manufacturing are now looking instead to stimulate 3D printing consultancy and co-creation.
Materialise is helping manufacturing companies in Ulsanin South Korea to develop applications through co-creation projects combining Materialise’s 3D printing expertise with the manufacturing companies’ knowledge of their industry, market and product. Meanwhile, the German multinational ThyssenKrupp has argued that the 3D printing industry could generate an incremental value of $100bn by 2025 for the Association of Southeast Asian Nations (ASEAN).
More materials
Although there is a strong move towards greater adoption of metal 3D printing, materials manufacturers, including an increasing number of chemicals companies, are starting to produce a variety of new powders, including polymers. That, in part, will also be driven by the expected rise in manufacturing applications, rather than prototyping ones.
Automation and software
As organisations start to integrate 3D printing into their production options, they come up against the twin issues of reducing cost and increasing efficiency. In short, there is a need to improve productivity, which means greater automation of tasks.
Software will be key in achieving this. Incorporating simulation into 3D printing workflow can help reduce cost elements such as consumables and machine time. Simulating the 3D print process can make it easier for production operators to spot potential errors before a build starts.
Interoperable, not proprietary
This mirrors one of the continual arguments within the IT industry: the need for greater interoperability and technology-neutral solutions rather than proprietary ones. There is an ongoing argument that if the 3D printing industry is serious about getting industrial manufacturers to consider 3D printing as a valid manufacturing technology for final products, then tying industry’s hands by locking them into proprietary solutions that limit flexibility and choice may not be the best way to go.
This is an edited extract from the 3D Printing in Oil & Gas – Thematic Research report produced by GlolbalData Thematic Research.
Related Company Profiles
Solvay SA
Materialise NV
Impossible Objects Inc.
Siemens AG
Stratasys Ltd