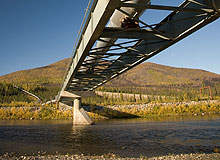
In the wake of the Deepwater Horizon disaster, which caused significant destruction to the Gulf of Mexico ecosystem, preventative efforts were made to secure oil wells and stop a similar situation reoccurring. In addition to the substantial threat of spills during drilling or production, there is an ever-present threat of problems during the transportation of crude oil, particularly along transcontinental pipelines.
In March 2006, a pipeline transporting crude oil through Alaska’s North Slope ruptured and spread more than 265,000 gallons of crude oil in what became the Arctic region’s worst ever oil spill. Because of the remote location of the pipe, within the most sparsely populated US state, the leak was not spotted for days and that delay contributed greatly to the impact on the Alaskan environment.
In July 2010, part of the Lakehead System pipeline that transports oil from the US state of Indiana to Ontario, Canada, burst, spilling 800,000 gallons into a creek that flows into the Kalamazoo River in Michigan, killing fish and endangering wildlife and water supplies.
Operating in corrosive environments
Pipelines designed to transport oil often operate in particularly corrosive or hazardous environments, such as across tundra or underwater at depths below 7,000ft where they are subjected to temperatures frequently below freezing. Because of these conditions, and the potentially damaging qualities of the cargo, considerable efforts are made to maintain the strength of the pipe as well as to offer consistent monitoring of the pipe’s condition.
A popular method is cathodic protection. This works by making the pipe itself the cathode of an electrochemical cell and applying a protective voltage. Important pipelines are often protected with an initial coating which is then supplemented by cathodic protection methods. The use of cathodic protection also allows for a number of monitoring methods for the entire line.
See Also:
Conventional monitoring involves measuring the pipe-to-electrolyte potential of the line. The difference between the metallic surface of the pipe and electrolyte is measured at points that are easily manned, such as onshore connection points, and any fluctuations in the charge can point towards a possible rupture or leak on the line. This system, however, does not allow for the precise location of any rupture to be identified.
How well do you really know your competitors?
Access the most comprehensive Company Profiles on the market, powered by GlobalData. Save hours of research. Gain competitive edge.
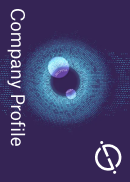
Thank you!
Your download email will arrive shortly
Not ready to buy yet? Download a free sample
We are confident about the unique quality of our Company Profiles. However, we want you to make the most beneficial decision for your business, so we offer a free sample that you can download by submitting the below form
By GlobalDataSpot the leak remotely
A further option is spot monitoring, carried out at various points across the pipeline manually. This can be carried out spontaneously or during scheduled maintenance or construction activities carried out on land or by trained divers at sea.
An increasingly popular method for sub sea installations, however, is the use of remotely operated vehicles (ROVs) that are designed for the purpose of constantly monitoring the line where necessary. Monitoring equipment attached to the ROV can allow the vehicle to conduct close-interval surveying of pipelines, and high-resolution cameras can be installed to detect minor defects before a rupture has even taken place.
The quality of this detection technology largely depends on the length and depth of the pipe, the clarity of the water and the type of existing erosion coating or protection installed along the pipeline.
The smart option
Technological advances, particularly in the fibre optics field, have allowed for advances in the detection and real-time monitoring of oil piplines. Upon installation, the technology measures flow assurances parameters and is capable of implementing corrective action, such as the shut down of pumping stations, in the event of anomalous data that may hint towards a rupture or leak.
The technology, which can be installed on both offshore and onshore environments, measures flow parameters from the source to the sales point within the pipeline and uses an online monitoring and control system to display data at a designated control room. Using the measurements, the subsea system can provide targeted intervention for a number of threats including leak detection, fatigue life prediction, Pig tracking and wax build-up prediction.
Once installed, the fibre optics can also monitor a number of exterior threats to the safety of the pipeline such as sudden drops in temperature, earthquakes or earth displacements, solid accumulations as well as displacements owing to strain and fatigue.
Ruggedised versions of the technology have previously been used on deepwater drilling operations, and the fibreoptic sensors are both lightweight and small in size, allowing for ease of installation. Highly sensitive and multifunctional, the sensors have little impact on the physical structure whilst remaining inert and corrosion resistant.
Under SCADA control
While the fibreoptic sensors take measurements, the control systems will be accomplished through Supervisory Control and Data Acquisition (SCADA) control software, which provides process control and data gathering in real-time.
The data can then be filtered and analysed by the SCADA software and installed onto a computer network, before being processed and presented for operators at the control system. For security purposes, the software automatically stores data and alerts central monitoring sites should abnormal or anomalous data be received.
This quick and accurate measurement system can highlight the size and location of the leak whilst taking preventative measures, reducing the environmental impact and allowing engineers to identify the precise location of the rupture, rather than locate it through a process of trial and error.