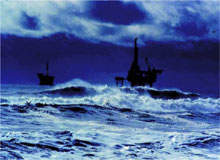
The original Ormen Lange was the massive viking longship of the ninth-century Norwegian King, Olav Tryggvason. Perhaps 42m long, with a serpent’s head at the prow and tail at the stern, this epic vessel, which was powered by 68 oarsmen, is mentioned in the Norsk Sagas.
The challenges posed by the development of the Ormen Lange gas field on the Norwegian Continental Shelf have been hardly less epic in scale. Norske Shell, which has planned and developed the wells, 125km off the west coast of Norway, has drilled the world’s deepest large-bore gas well to a depth of around 2,700m, down through 850m of some of the most environmentally difficult waters on the planet.
In early July, with three of the planned 24 wells completed, Shell, the operator during the production phase, began the first wellhead tests. The first gas is due to arrive in Norway in October, with the first supplies reaching the UK before the end of the year. Ormen Lange is expected to meet 20% of UK gas needs.
Jimmy Edgar, Shell’s completions and subsea team leader describes the conditions in which the dynamically positioned (DP) drill ship West Navigator has had to operate as “quite shocking”. “From October through to February, even sometimes into March, we have five months in which the weather is horrendous. One of the major challenges has been keeping the DP in position in 850m of water until the blowout preventers (BOPs) are in place.” Shell has been working with week-long forecasts and detailed statistical weather data that has enabled it to programme disconnections when the swell causes the vessel to heave more than 6m.
PERFECT PLANNING
“If we are expecting a particularly big storm, then obviously we are going to have to take some kind of action,” says Edgar. “But the other thing that can catch us out occasionally is that, in this part of the world, very large Atlantic swells come through – long-period waves that are the result of storms, often in the Caribbean. Because of the long period between waves, the vessel has lots of time to move up all the way to the top of a wave and then down the other side. Such conditions can cause huge heaves on the rig in what appears to be an almost flat sea.
How well do you really know your competitors?
Access the most comprehensive Company Profiles on the market, powered by GlobalData. Save hours of research. Gain competitive edge.
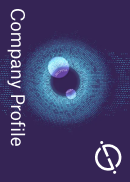
Thank you!
Your download email will arrive shortly
Not ready to buy yet? Download a free sample
We are confident about the unique quality of our Company Profiles. However, we want you to make the most beneficial decision for your business, so we offer a free sample that you can download by submitting the below form
By GlobalData“What we have done throughout drilling, and also during the completion phase, is analyse those situations, so that we have well-defined operating envelopes in terms of wave height, vessel movement, heave and the position of the vessel relative to the well centre.” Disconnecting the upper part of the BOPs and the lower marine riser package (LMRP) in an emergency can be done at the push of a button in 45–60 seconds.
Edgar explains that drilling has not been badly affected by these disconnects. Moreover, the time lost in planned disconnections in the face of inoperable seas, such as the 28m waves that hit the drilling area this February, was used to take the West Navigator into port to pick up equipment, including Christmas trees.
The first of 14 trees – the biggest ever used in an offshore project – was actually installed in November 2006. Edgar says: “The weather fluctuates between being really bad and relatively acceptable, but we could see that, statistically, we would be able to do the installation at that time. We took the chance, knowing that we might have to wait around for a few days or even several weeks to get the window.”
In Edgar’s view, one big reason why there have been no major problems in the drilling is planning. “The biggest challenges have come in the completion phase, and the level of planning that went in there was something that certainly I have never experienced,” he says. “The first well engineer arrived here just over six years ago to start planning these wells. Since then a detailed planning team has steadily been built, and we are now in the execution phase.
“So we have had six years from the conceptual stage through to execution. The results of that are evident, especially in the completion phase, where the unknowns and uncertainties were a bit greater. Planning has also enabled us to deliver those wells easily within budget and well within the time we expected.”
DRILL SHIP DILEMMA
Shell selected the West Navigator drill ship (in a contract worth some $167m) over semi-submersible options, in part because of the vessel’s greater flexibility and load carrying capacity. Edgar admits, however, that the smaller moon pool, no more than 5m from the well centre, has posed challenges that would not have occurred on a semi-submersible. Edgar says: “With the current at Ormen Lange and with the waves, one of the things we have had to watch out for is collision between the pipes or Christmas trees or whatever we are running through that hole and the side of the moon pool, something that wouldn’t have occurred with semi-submersibles.”
Despite these challenges, in June Shell announced a new contract with Norwegian owners Seadrill to keep the West Navigator on Ormen Lange for a further four years in an $810m deal.
Shell has worked via two 1,150t well templates (A and B), each with slots for eight wells. Phase two of the drilling development will involve the deployment of a third template, but at the moment, says Edgar, approval has not yet been given for the planned D template. “The deployment of this template depends on information from the first production. We have drilled a monitoring well in that part of the field to demonstrate connectivity with the reservoir. If we find that the reservoir has sufficient connectivity, the D template will not be required.”
LOW-TEMPERATURE FLOW
Another difficulty that Shell has had to address is the low temperatures revealed when thermal analysis of the well tests was done. Edgar says: “We discovered that it doesn’t really matter what flow rate we flow the gas from the reservoir up through the water column at. It arrives at the rig at approximately ambient temperature.”
Speaking to some experts on flow assurance, this is something they have never come across before. “Typically you would get maybe 50°C or 40°C at the rig, but what happens in Ormen Lange is that the riser is so long and cold that the gas arrives at about 4°C at the rig. So it is already very cold. During the well test, when we allow the gas to expand through the well test package, it cools down even further.
This is one of the biggest challenges we face now. We expect to see temperatures of -50°C through the well test package. “The way we are managing this is by heating the gas up. Of course, this is common, but the temperatures we are experiencing are unusually low.
“We have had to make major modifications to the rig to bring in stainless steels designed for cryogenic use. It has cost us significant sums to replace items like the boom on the rig and the pipelines that go to the flare boom. We are working through 850m of very cold sea, which at the seabed is -2°C. Maybe during the summer the surface temperature is 12°C, but that is only for the first 50–100m. Below that you are down to 4°C pretty much all the way down to the seabed. It is almost like a big heat exchanger, but in reverse. It doesn’t matter what you introduce at the bottom, in terms of flowing the well harder, the gas still comes out at 4°C.”
HYDRATE SOLUTION
The final battle Shell has had to fight is against hydrate formation. When water and gas mix under pressure this can occur at between 20°C and 30°C. “This unusual substance becomes stable at higher pressures and lower temperatures,” says Edgar. “We have both. On the seabed we have minus 2°C and 290bar, which is about 4500psi. Those are the perfect conditions for these ice-like substances to form, block the pipe and prevent flow.”
The solution has been to inject monoethylene glycol at the base of the riser to prevent hydrate formation. From the main glycol reservoir at the gas processing facilities onshore at Nyhamna, lines bring the anti-freeze agent to the field. It is then captured at the well head and piped back ashore to be dried, recycled and pumped out again.
Sea conditions on the Ormen Lange gas field might shock some, but they haven’t fazed Shell, which has shown that, with careful planning, ingenuity and technological expertise, even the worst conditions can be overcome.