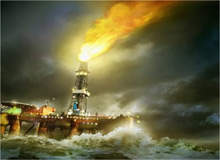
The safety culture onboard an offshore installation has to be exemplary by its very nature. However, in the interest of continuing improvement and determining the robustness of safety systems in place in potentially hazardous heavy industry, the Health and Safety Executive (HSE) has put forward the major hazard control model (MHCM).
The MHCM is a way of assessing and preparing for a range of hazardous scenarios in the offshore environment. It is also a way for senior managers to take an active part in the development of safety arrangements and promote improvement by asking questions about protocols and controls. It is certain that the operation of drilling and production platforms is governed by the bottom line – in other words, financial performance. But when money has to be spent on safety, how is the effectiveness of this expense to be monitored? Many might measure the success of safety procedures simply by the lack of major incidents. However, failure of safety procedures can be absolute, final and devastating. The Piper Alpha tragedy in 1988 is such a case.
Prevention is always the best policy when it comes to HSE. Currently, a limited measure of major hazard safety is the number of hydrocarbon releases reported. This measurement has improved, with the number now down to only 70 per year across the North Sea fields (previous years have seen between 150 and 170).
MAINTENANCE AND TESTING
According to Tony Blackmore, an operations manager in the offshore safety division of the HSE: “The industry is trying to get to grips with the intrinsic causes of major accidents and to reduce the number of major hydrocarbon releases. But it is getting more difficult as the release sources are becoming less obvious and these sources now tend to depend upon the condition of the asset (platform) and the maintenance. It is important that maintenance is carried out and control measures verified, and also that there are robust safety protocols in place to prevent major hazard releases of hydrocarbons.”
Every owner of a major hazard plant has to carry out some kind of hazard analysis as part of their safety protocol development. The major accident scenarios for an offshore installation might include structural collapse, a major hydrocarbon leak, a helicopter crash or a collision. All of these scenarios are analysed and control measures put in place to prevent or contain them. The control measures themselves then have to be tested / stressed rigorously to determine whether they are adequate and their performance documented and reviewed by senior management.
How well do you really know your competitors?
Access the most comprehensive Company Profiles on the market, powered by GlobalData. Save hours of research. Gain competitive edge.
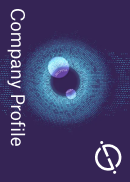
Thank you!
Your download email will arrive shortly
Not ready to buy yet? Download a free sample
We are confident about the unique quality of our Company Profiles. However, we want you to make the most beneficial decision for your business, so we offer a free sample that you can download by submitting the below form
By GlobalDataOnly by doing this can the safety systems evolve and improve to standards that satisfy the demands of a stringent safety culture. Blackmore says: “If there are problems with control measures, if for example emergency shutdown valves fail when tested (control systems here would usually be duplicated), it is important that there is an understanding of what the issues are and that action is taken immediately to remedy the situation. These measures are part of the MHCM, and senior management needs to take an overview and make sure its control model is effective.”
One major problem is that health and safety is invisible and there are few if any reliable indicators. If nothing happens, the safety systems have been successful. But they need to be tested stringently and kept up-to-date with new knowledge and technology.
According to Blackmore: “Occupational safety indicators (slips, trips and falls) are no good in this situation. Senior managers need to understand the MHCM to talk with authority about it and to use it to safeguard against major accidents offshore.”
Recent work by the HSE on offshore facilities has shown that heating ventilation and air conditioning (HVAC) controls are poor, with about one-third of tests failing on some installations. HVAC is a major hazard risk control. This is a control measure about which senior managers need to ask questions as part of the MHCM. HVAC control problems were identified as factors in the Piper Alpha tragedy.
ZERO TOLERANCE
Blackmore says: “Factors that undermine the MHCM have to be identified and challenged – for example, poor integrity of equipment and assets. Falling standards, such as relying on the manual shutdown of a piece of equipment if an automatic system has malfunctioned, cannot be tolerated. Once control measures performance drops, the MHCM is challenged and serious questions must be asked about the level of safety available.”
One key factor is having good data from reliable and stringent testing and then documenting this for use by senior management. This data can be synthesised to establish a baseline for high levels of control.
Tony Blackmore says: “Offshore companies have some of the best written protocols, but they are not so good at delivering the high level of control required for robust safety integrity. Senior managers need to become better at challenging the procedures or system controls to effect improvement.”
Overall, the safety record is quite good for the North Sea, but it is not in the upper percentile. There is an opportunity for senior management to use the major hazard control model to make the North Sea one of the safest places to work in the world. But this will rely on senior management’s leadership to promote the adoption of a new (major hazard) safety culture among all levels of staff working offshore.