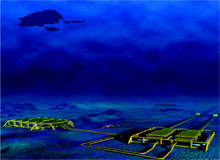
The complex bathymetry to be negotiated by long pipelines running from wells to processing systems tens of miles away, such as at Ormen Lange, are becoming increasingly common in deepwater subsea production, says Dr Siva Subramanian, staff research scientist, flow assurance team, of Chevron Energy Technology Company. Distance and water depth also limit access and mean that intervention costs are very high. But flow assurance over variable seabed topography is only part of the challenge.
“We are also seeing in parts of the world, such as the deepwater Gulf of Mexico (GOM), extremely high pressures and high temperatures (HP/HT) for the reservoir,” he explains. “There are several discoveries that have to contend with 15,000psi – 20,000psi reservoir pressures and temperatures ranging from 250°F –350°F. They bring with them some interesting phase behaviour issues. One of these is Joule-Thomson heating instead of cooling.”
Typically expanding pressurised hydrocarbon fluids – through a subsea choke, for example – causes the cooling of the fluids. But with these HP/HT systems, expanding at high pressures and choking subsea in early field life to control wells actually results in heating.
Such heating can exacerbate high-temperature concerns over material selection and qualification, thereby pushing materials to the limit in some cases. Naturally, projects attempt to focus on reducing temperatures in the system to ensure the reliability of materials and subsea system components.
Flow assurance, says Subramanian, has traditionally been concerned with low temperatures, such as those encountered at lower production rates or later in field life when solid precipitation and deposition in the subsea system become a concern.
DEEPWATER CHALLENGES
How well do you really know your competitors?
Access the most comprehensive Company Profiles on the market, powered by GlobalData. Save hours of research. Gain competitive edge.
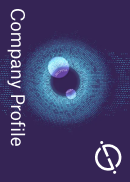
Thank you!
Your download email will arrive shortly
Not ready to buy yet? Download a free sample
We are confident about the unique quality of our Company Profiles. However, we want you to make the most beneficial decision for your business, so we offer a free sample that you can download by submitting the below form
By GlobalDataDeepwater oil developments typically tend to adopt heat retention solutions, such as insulating subsea equipment, and installing wet insulated or pipe-in-pipe flowlines to mitigate hydrate formation and wax deposition while flowing. Insulation also provides operators with valuable time during an extended unplanned shutdown to treat and secure the different subsea components in order to prevent hydrate formation.
HP/HT deepwater developments such as those in the GOM pose the unique challenge for flow assurance and subsea engineers of how to design and operate the system to provide relief from high temperatures in early life or at high rates while ensuring operability and flow via heat retention in later life or at low rates. “You are, for example, expecting materials to work over a wide range of temperatures: -20°F to +300°F, because you are trying to cover the range of possibilities over the life of the field.”
Combination solutions, such as less insulation with electric heating as needed, may be appropriate for some projects, since they can potentially provide the flexibility to adapt and address temperature issues over the life of the field. Flowline burial in later life to improve heat retention may also be an option for shorter offsets in the order of a few miles.
“However, the flexibility may mean more complicated designs,” says Subramanian, “which, when combined with the ultra-deepwater environment and long distances, could create other technical and operational challenges. A flow assurance engineer, therefore, has to adopt an integrated approached with a systems view in mind and work with other disciplines, such as subsea engineers, to generate the optimum solution for a field.”
SOLIDS SOLUTIONS
“In parts of the world like West Africa,” says Subramanian, “barium sulphate scale management in the area near the wellbore is typically a big concern for projects considering seawater injection into the reservoir for either pressure maintenance or improved recovery. Scale precipitation in this case can be triggered by incompatible chemistries as a result of mixing the seawater being injected with formation brines. Such precipitation in the near-wellbore region can jeopardise well
productivity quickly by plugging perforations and decreasing near-wellbore permeability.” Given the downhole nature of this problem, intervention cost sand the impact on projects can be high if managed improperly.”
Frequent and expensive squeeze jobs that place scale inhibitor in the near-wellbore area may become a necessity to ensure productivity, thereby adding considerably to field OPEX.
Alternatively, projects may deploy sulphate removal systems that end up having large footprints topsides and add to CAPEX, but almost completely remove all the sulphate ions from the seawater being injected, thereby removing an essential ingredient needed to form barium sulphate scale.
Subramanian says: “So you are looking at fairly expensive options to manage scale downhole. In your attempt to improve reservoir recovery, you now have created and have to manage solids in your system – another example that stresses the importance of a flow assurance engineer adopting an integrated approach and working with other disciplines, such as reservoir and completions engineers, to generate the optimum solution for a field.”
Hydrates tend to be a significant concern, typically in deepwater developments. The combination of high pressures and low temperatures can introduce hydrate risk from deep in the wellbore all the way to the export gas system. The setting depth for subsurface safety valves (SCSSVs) is typically linked to hydrate stability. The combination of water depth and hydrates being stable deep in the wellbore appears to be forcing SCSSV setting depth to more than 10,000ft TVDSS, thereby pushing its design to the limits.
DESIGN AND MODELLING
Flow assurance has become a big driver in the early design phases of a subsea deepwater development. “You cannot only look at a piece of the system and focus on just the reservoir, wellbore or pipeline,” says Subramanian. “You have to look at all the different parts of the system all the way from the sand face to the beach.”
“An integrated life-of-field approach to design and operability is crucial in devising and deploying effective strategies to manage the various flow assurance issues.” In the operational phase of the project, it is becoming common to find ways to integrate the real-time information from field instrumentation to monitor and manage flow assurance issues.
Real-time monitoring systems that couple field data with hydraulics simulations can provide operators and engineers with information to maximise production, monitor solids formation, verify if gauges are working properly, optimise procedures and adopt appropriate flow assurance strategies that reflect actual conditions in the field.
Subramanian points to industry-wide initiatives, such as DeepStar, which are seeking to advance the science on flow assurance issues such as hydrates and the complexities of multiphase flows. “There is still a lack of understanding of how these phenomena play out in a flowing system – what parameters control blockage formation and deposition of solids such as hydrates in a multiphase pipeline under flowing conditions, why certain systems flow even inside the hydrate region while others block.
“The hope is that continued research can progress understanding far enough that we can actually live with hydrates and solids in our system because we understand the risks that they pose and can accurately predict how they will behave in our system. Technology is enabling a lot of things in terms of addressing flow assurance issues and operability on current projects, but work needs to continue on improving the fundamental science and understanding.” Meanwhile, Subramanian is certain that
flow assurance has to adopt a totally integrated life-of-field approach that addresses flow challenges right through from the sand face to the beach.