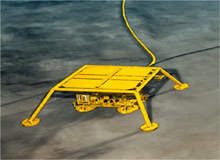
For over 20 years subsea processing has been poised as one of the most potentially promising technology developments in the offshore industry – and now, shifting factors within the sector over this period have finally begun to tip the balance in its favour.
In the early days, with deep water posing the biggest challenge, technological necessity and financial incentives formed the principal drivers.
Today, to meet the demands of deeper and more remote reservoirs, the emphasis is firmly on increased production and enhanced recovery.
For an industry often under the microscope for its treatment of fields in sensitive areas, the benefits of subsea production are clear – though there has been more than one ‘false-dawn’ along the way. As Halvorsen, senior vice president for FMC Technologies Global Subsea Production Systems is quick to point out: “a true subsea development is very environmentally friendly.”
TROLL PILOT
The success of the Troll pilot – a Norsk Hydro prototype separation and water injection project which came online in 2001 – was widely expected to give subsea processing a major fillip. Although the scene appeared to be set for the technology to turn long-standing promise into significant uptake within the offshore industry, while the project did raise awareness and drive a small trickle of subsea schemes, the anticipated surge of wider interest failed to materialise.
How well do you really know your competitors?
Access the most comprehensive Company Profiles on the market, powered by GlobalData. Save hours of research. Gain competitive edge.
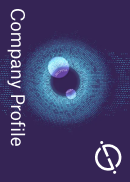
Thank you!
Your download email will arrive shortly
Not ready to buy yet? Download a free sample
We are confident about the unique quality of our Company Profiles. However, we want you to make the most beneficial decision for your business, so we offer a free sample that you can download by submitting the below form
By GlobalDataWith the benefit of hindsight, it is perhaps easier to understand why. In 2000, the UK technology specialists OTM Consultants and Douglas Westwood surveyed a number of operators to establish if they would be considering any form of subsea processing – separation, boosting, raw water injection or gas boosting – as a potential development tool in future.
Even though the Troll plant’s 30-month installation phase had already been successfully completed by the time of the study, less than 10% of the participants indicated an interest in using seabed systems.
THE GAME-CHANGER REPORT
Three years later, however, when the question was next asked, perceptions had significantly changed. In what quickly became known as the ‘Game-Changer Report’, OTM / Douglas Westwood discovered that 90% of operators expected to use some form of subsea within ten years – with more than 75% expecting to do so in less than five.
Despite this apparent level of increased interest, the actual activity in the sector has remained slow – at least until the latest reports which now seem to indicate a real shift in the way operators view this technology.
Spending on these systems has been predicted to reach $3.4bn between now and 2015. Most of this is expected to be spent in Western Europe, followed by Africa, Latin America and North America, with 131 seabed boosting applications likely to account for more than half of the expenditure. Twenty-eight separation systems, over 1,000 multiphase meters and 15 wet gas compressors will also be included.
With the July 2007 announcement of Cameron’s $100m contract to provide wellhead and subsea tree systems, manifold structures, connections and associated equipment for Apache Energy’s Van Gogh project offshore Western Australia, the early signs are good.
If the full predictions do eventually come true, it will mark a watershed moment as subsea systems definitively emerge from their largely ‘niche’ perception once and for all, to claim their place in the industry mainstream.
SUBSEA SOLUTIONS
In addition to FMC Technologies and Cameron, other big names in the game include the likes of ABB Vetco Gray and Aker Kvaener Subsea (formerly Kvaerner Oilfield Products), offering a range of technologies to meet the operating requirements of modern developments.
The general ‘subsea’ umbrella encompasses a series of key elements for seabed processing – power distribution, separation, boosting, raw water injection and gas compression – which are in use to varying degrees around the world. However, with companies such as Statoil and Hydro topping the list of operators ready to use this approach, inevitably much of the work has remained firmly in Norwegian waters.
One of these projects – the installation of the world’s first commercial subsea separation unit – is currently underway at Statoil’s Tordis field, which lies in 200m (656ft) of water in the Norwegian section of the North Sea. Sited between the existing Tordis Subsea Field (originally delivered by ABB Vetco) and the Gullfaks C platform, it provides a clear illustration of some of the benefits to be had.
Once the full-scale subsea separation facility comes onstream, Statoil expects to improve the recovery factor of the field from 49% to 55%. A carefully designed package of upgrades to the field will allow an expected additional 35 million barrels to be extracted, with the new subsea system being anticipated to yield around 19 million barrels of this improved recovery.
The scheme involves removing water and sand from the well stream subsea and then subsequently re-injecting the water via a separate subsea well.
By effectively reducing the back pressure toward the Tordis field, it permits Gullfaks C to process more hydrocarbons – reserves which would otherwise be destined to remain unrecovered.
While Norway hosts many of the current subsea projects, Total’s Pazflor deepwater project off the coast of Angola has probably better showcased the promise of the technology.
PAZFLOR DEEPWATER PROJECT
40km east of the centre of the Dalia field, Pazflor is more accurately viewed as two projects in one – a conventional Oligocene deepwater reservoir and Miocene heavy reserves located in three distinct fields. After considering the options, Total opted to develop the low-energy reservoirs using subsea separation – eliminating gas-lift and separating the associated gases from the hydrocarbon liquids, to allow the stream to come away well without the need for slug-catching.
There are other aspects of the project which also contribute to its overall attractiveness, including the cost-saving configuration of the field, which simplifies the subsea elements, optimised well location, reduced drill trajectory and a lowered gas compression demand.
In the final analysis, Pazflor stands as the long-awaited project to make the definitive case for subsea processing – heavy on firm indications of the bottom line savings and light on technology over sell.
Although operators remain naturally risk-averse and the psychological barriers to uptake still persist, the hard numbers approach taken by Total must surely begin to foster a growing confidence in the future potential of subsea production.
FUTURE DEVELOPMENTS
As oil prices have risen, the drivers on subsea processing have changed – a trend widely expected to continue in future, making enhanced recovery and increased commercial viability key objectives for the ongoing use of the technology. Reliable and cost-effective subsea approaches to accelerate production and boost reserves seem certain to form the lynch-pin in the development of offshore deepwater fields and reserves in remote or harsh environments.
There is widespread consensus that improved production systems hold the key to allow not only the exploitation of new oil and gas fields but also the extended development of mature offshore fields too, with increased recovery rates providing a major source of production. It is clear that the reliability of subsea processing equipment will be crucial in ensuring the success of such projects – and unsurprisingly this is an area which the technology providers are working hard to
perfect.
THE ARCTIC QUESTION
Subsea systems may also hold the answer to the tricky environmental and geo-political questions posed by the resources hidden beneath the Arctic.
With estimates suggesting that up to 25% of the world’s undiscovered oil and gas reserves are in Arctic areas, recovering them will become increasingly attractive. Robust and entirely subsea processing systems could offer the ideal solution.
With no above-water elements, oil and gas could be recovered from under the ice or in key fishing grounds and produced direct to shore, neatly side-stepping many of the environmental issues often associated with production in such sensitive areas.
Studies by Aker Kvaerner found that it can take up to 30 years to develop and prototype new products in the offshore industry – three times longer that for many other sectors. While the market for seabed processing does now seem to be gearing up for growth, perhaps it should come as little surprise that this technology has only just begun to come of age.