‘Passion’ is not a word generally associated with offshore technology, but I want to share with you my passion about cranes and lifting and particularly heavy lifting as it applies to the offshore industry.
The offshore world has developed rapidly in a way that could never be done on land because of the sheer size of the structures involved – and that’s where heavy lifting comes in.
Much of my career has been involved with lifting and I feel really passionate about what has been achieved by the industry in a relatively short time.
LAND CRANES
Think of the normal mobile crane you see moving down the street – perhaps a wheeled vehicle with a hydraulic jib, or a crawler crane being transported to a site on a low-loader. Or look at a construction site or the city skylines everywhere at the moment and consider the crop of tower cranes. They can all lift a few tens of tonnes, maybe even a few hundred. They provide vital assistance to all forms of land-based construction.
To help build a mental picture of the sort of weights I’m going to be talking about, think of the iconic Routemaster red double-decker London bus. That weighs about 8t unladen or 12t laden. A typical 40ft container has a capacity of 22t and lorries are generally limited to about 40t on roads, whilst a cube of water measuring 10m x 10m x 10m weighs in at 1,000t.
How well do you really know your competitors?
Access the most comprehensive Company Profiles on the market, powered by GlobalData. Save hours of research. Gain competitive edge.
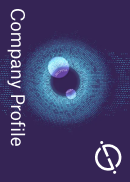
Thank you!
Your download email will arrive shortly
Not ready to buy yet? Download a free sample
We are confident about the unique quality of our Company Profiles. However, we want you to make the most beneficial decision for your business, so we offer a free sample that you can download by submitting the below form
By GlobalDataThe very biggest mobile land-based cranes used in offshore platform fabrication yards in Scotland a few years ago could lift up to 1,500t each. I think there were three of them and two sometimes worked together to lift even larger loads. Some fixed (non-mobile) derricks used in offshore fabrication yards in the US can certainly lift larger loads, but nothing matches what can be done offshore.
OFFSHORE CRANES
Back in the 1950s all that was available for offshore use were cranes mounted on flat-bottom barges capable of lifting about 200t; by the 1960-1970s ship-shaped monohull crane vessels had been developed and were hard at work with up to 3,000t capacity; then in the summer of 1979 there was an enormous leap in capacity thanks to the introduction of the Balder and Hermod semi-submersible crane vessels (SSCV), each fitted with two enormous cranes.
In the mid 1980s, two even larger SSCVs came onto the market. DB102 and M7000, like Balder and Hermod before them had capacities larger than anyone was designing liftable structures. But that did not last. Both vessels, Heerema’s Thialf and Saipem‘s S7000, (by then renamed) were upgraded such that the combined lifting capacity of the two cranes on each vessel is 14,200t and 14,000t respectively.
Indeed, S7000 holds the world record for an actual lift of 12,150t; and in 2007 lifted the 9,500t jacket for Pemex in dynamic positioning mode. Thialf has a staggering lifting capacity of 14,200t. That’s the weight of more than 1,180 fully laden London buses; or a sizeable ship, such as one of the 650 top-of-the-range supply vessels currently being built; or a cube of water measuring nearly 25m x 25m x 25m.
This truly giant leap came about because of the requirement to build huge integrated decks weighing up to 12,000t and install them in one lift, rather than the earlier technique of using small pieces to build up the topsides ‘jigsaw’. These integrated decks can perhaps be 100m x 30m x 30m high and only the ‘heavy brigade’ can deal with them.
They avoid the expensive and time consuming requirements of ‘hooking up’ smaller modules, and the vessels can also be used efficiently to lift and install huge steel jackets like the Pemex example mentioned above.
Nothing like these cranes exists on land and probably cannot exist on land – they need the forgiving support of buoyancy forces on a ship’s hull. This supports the vessel on which to mount such huge cranes. Additionally, the vessels can travel safely around the world and work in the most hostile environments.
These are the workhorses that continue to serve our industry. They set, and continue to set, new lifting capacity records and offer year-round workability.
For over 20 years, no new SSCVs have been added to the worldwide fleet of five. But the industry is so busy now that a new generation of massive heavy lift vessels, able to move at higher speeds than their predecessors, is planned / under construction. The new generation includes a massive SSCV, with a lift capacity of 15,000t, and two monohull crane ships each with a lift capacity of 5,000t that are under construction and due in service in 2010.
Several multi-purpose construction vessels with slightly smaller cranes are also being built.
SCALE IS EVERYTHING
There was a reception at the Tour Montparnasse for delegates at the IMCA Annual Seminar held in Paris in the autumn. As we stood some 210m above the streets of Paris, it was fascinating to think that this is roughly the height above sea level of the tip of the crane jibs on Thialf and S7000; equally it is the sort of depth at which saturation divers work.
Objects also go extraordinarily deep below sea level as exploration and production moves into the deeper waters of the earth’s continental shelves. Seismic survey, exploration and production drilling and installation of structures and pipelines have all exceeded 2,000m and sometimes 3,000m.
This means that not only are the offshore crane vessels equipped to lift and install jackets and decks, but they can place heavy objects and drive piles safely and accurately on the seabed some 2km below sea level.
For some deep-water operations it may not be the giant vessels that are required. Smaller but more specialised vessels may be better placed to do the work.
Just think of the length of wire that is needed for this sort of operation – the crane wires which hold up the jib and raise or lower the blocks kilometres below sea level are all reeved many times, so several kilometres of large diameter special wires are required.
Dare I say that wire ropes are another of my passions? Heavy structures are being designed to be installed at such depths that wire may no longer be the best choice to suspend them as the wire itself weighs a lot and eats up the crane capacity. So the future may involve more exotic materials such as glass- and carbon fibre as an alternative to traditional wire ropes because these fibres are much lighter than steel.
GETTING DOWN TO DETAIL
I like to think of more than just the vessel and what it can do. What about the people involved with lifting?
First there are the different streams of people who operate these highly sophisticated and computerised vessels and their cranes and other equipment; then there are the engineers who design, build and maintain the vessels and their cranes – they cover an amazing range of disciplines. Then there are the people who design and plan heavy lifts.
The heavy lift design engineer is the conductor of an orchestra ensuring that a structure that is designed to sit on its feet survives the trauma of effectively being lifted from its head. Large scale structural engineering, detailed design analysis, attention to detail on all the lift points (pad eyes, pad ears or trunnions) come to bear. There is a long chain of components in any lift.
The structure must hold itself together in the lift condition (the opposite loading to that seen during construction, transportation and the final installed condition). The structure needs to support the lift points. The lift chain continues upwards perhaps through shackles to slings and perhaps spreader frames, and then into the crane hook. From there into the crane wires which I have already talked about and the crane’s jib and structure itself.
Lastly the loads come back down to the crane foundations, which are tied into the vessel itself and the whole is neatly balanced on the vessel’s buoyancy. All parts of this chain have to work in perfect unison – hence the conductor analogy.
There is such a wide variety of tasks in offshore lifting that finding the right crane for the job is essential too – there’s something to suit every operational activity be it offshore construction (heavy lift to or from the seabed or platform) or in support of pipelay, drilling, diving, ROV operations, trenching, wreck removal, well stimulation, mobilisation, offshore loading, personnel transfer and more.
Mast cranes, pedestal cranes, crawler cranes and A-frames all play their roles with various sorts of booms, heave compensation and power / control to be taken into consideration.
Finding the people to work with these true monsters of the deep is vital. The need for more people entering the industry is of constant concern. Working on and supporting these vessels you will find engineers and technicians trained in structural, civil, mechanical, electrical, electronic, hydraulic and systems engineering, in naval architecture and computing, right through to materials scientists and lubrication specialists. The industry needs you all.