
The mono-diameter well will offer high production flows from deep oil and will be an economic method of using redundant rig slots on fields (with declining main reservoir production) to tap into small satellite fields. These would otherwise be too expensive to exploit by moving a rig to them.
Shell’s research into the mono diameter began with slotted tubes. As Wim de Vries, the programme manager of the company’s research and development programme explains, it was thought that these would expand more easily than solid tube. But, it soon emerged that an expansion ratio of between 12% and 19% could be achieved in solid tube using what he describes as the ‘small window’ in the material properties between permanent deformation, with a slight reduction in strength and actually damage to the metal.
The Netherlands lab is currently doing expansion tests of up to 25% with normal steel but to achieve the maximum 30% it is working with the steel industry on new metal formulations.
A number of onshore field tests of the expanded casings are currently under way. “We have done between 600m and 700m wells with 9.625in casings that we expanded by between 12% and 19%,” says de Vries.
“We are battling a dilemma here where we need thin and not so strong metal to get maximum expansion but we need thick and strong metals to withstand the pressures the metal is exposed to by the reservoirs that sit behind it. So, we are trying to fine tune in our research and development to achieve that balance between maximum expandability while retaining sufficient collapse rating of the pipe, so we can safely keep our reservoirs under control.”
ORMEN LANGE
How well do you really know your competitors?
Access the most comprehensive Company Profiles on the market, powered by GlobalData. Save hours of research. Gain competitive edge.
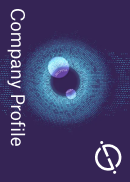
Thank you!
Your download email will arrive shortly
Not ready to buy yet? Download a free sample
We are confident about the unique quality of our Company Profiles. However, we want you to make the most beneficial decision for your business, so we offer a free sample that you can download by submitting the below form
By GlobalDataDe Vries expects that the first mono diameter production well will be on land, with the first offshore effort being a half mono diameter well in the Gulf of Mexico. The target for Shell is to have the application ready by 2012 when it embarks upon the next phase of Ormen Lange. Here, says de Vries, the mono diameter well with its high production rates as against the loss of flow from a conventionally tapered hole will be ‘a big enabler’.
Mono diameter wells, he explains, describe the method of drilling from an existing platform to a remote location while still having sufficient well bore diameter to reach the production rates that make the project economic. “This is not only in Ormen Lange. This is in Sakhalin and anywhere where we have big fields with one central platform. Same in the Gulf of Mexico where there are a lot of satellite fields that cannot be reached with existing drilling technology from the existing
platform.
“You can avoid having to put a subsurface template in the sea but actually drill from the existing platform. You can do it now but you end up with a small hole size which greatly reduces the production rate of the well and you don’t want that of course,” says de Vries.
He explains that his lab is working with Shell’s energy and petroleum teams in Ormen Lange. “We know exactly what their needs are so in our testing programme we are working up to them. We have it on our minds all the time. Therefore by the time they want to start drilling, we will be ready to actually drill a mono diameter well offshore in deep water.”
The advantages of mono diameter wells are that, unlike the standard well where unique equipment is required for hole size, tapering down to the well bottom, the equipment on the rig floor can be standardised.
“You don’t need to use rigs with a big lifting capacity to handle these big pipes at the surface, so you can use smaller and simpler equipment which can be standardised along with your procedures. There are also a lot fewer solids to be handled because you drill less earth. There are many things that make it cheaper.”
However, de Vries emphasises that much work remains to be done. “It is relatively easy to demonstrate the concept on a land well with two joints of pipe but to do a full-blown well safely and neatly is still so cumbersome that in terms of the rig time you use, it becomes uneconomical.”
CHALLENGING TIMES
The challenge now is to get beyond the intermediate trips with the separate expansion of each joint, then go out the hole with the cone and test that no leaks were pulled or casing burst, to be able to do the expansion in a single trip. To undertake the operation, quickly, securely and safely requires the development of procedures and tools.
e-zip applications.”
This is being done, de Vries says, in cooperation with service companies such as Enventure and Weatherford who will then build and test the real tools. Partial mono diameter wells are already well established he adds, with Enventure alone having already done a cumulative total of some 600km around the world. The expansion process for the full mono diameter well, he explains, is from the bottom up rather than top down.
“You can do both. We could push it through the pipe and if you do it in the lab with one join, it hardly makes a difference. But, if you want to do 1,000m it is a much, much more controlled process to be in tension and pull on the cone rather than try and push it. You can put hydraulics on it from below. You could, of course, do that from above and pump the cone down, both systems exist actually. The better system however seems to be the down up because then you can make it more of a single trip.
“If you do it the other way around, you would then have to go down with the cone and then, after expansion, pull it out. So, if you let the cone go down with the casing right from the start, then all you have to do is the expansion while pulling up. And when the expansion is done, the tool is out of the hole as well – it saves you a trip.
“So, it is more economical to do it bottom up because that extra trip in a very deep well could be a day’s rig time which nowadays offshore is $600,000.” Once the single trip mono diameter technology is operational de Vries reports that Shell will be focusing on a ‘breathing cone’, still in the early design stage.
“It can go in and out and follow the shape of the bore-hole wall. That is much nicer because you can then do away with cementing. So, rather than forcing a fixed cone through a pipe which gives you one and the same expansion all the way, once you have a breathing cone you can let it go out until it feels resistance, all within the expansion that the metal allows of course.
“If the hole you drill has a diameter tolerance within, say, a couple of inches, with a compliant or breathing cone, you can make sure that you always expand against the bore-hole wall within these tolerances and according to the type of metal that you are using. With a fixed cone you cannot. You may in one place be touching the bore-hole wall and in another place, you may be one or two inches off.
And then, of course, you have to make sure that you get zonal isolation across the places where it is off. That is why we still pump cement or put e-zips around it. But, once you have a compliant cone that will follow the shape of the bore-hole, you can actually force your metal close to the rock and get isolation that way. You could potentially in the future do away with cementing altogether which would save an awful lot of rig time and make wells a lot cheaper. It will, however, take a couple of years before you will see this in the market.’
MONO DIAMETER AND MORE
Mono-diameter well technology is far from the only innovation coming out of Shell’s Netherlands laboratory. “One of the challenges with the e-zip collars is that you cannot retrieve by just pulling on them. They are so strong that if you try to pull them free, you part the pipe. So, if you want get rid of them, you have to work the well over and mill them out.
“We have now developed an e-zip that is retrievable and you can run it in the hole, let it swell and set. It is a kind of retrievable packer. It also swells a lot faster than the normal e-zips, which can take several days. This one can do it in a couple of hours, depending on how you design it and how you dope it.
“Rather than have solid rubber on the pipe, we have shredded the rubber to pieces and vulcanised the pieces on the pipe. This still gives several 100bar pressure to the reservoir to give zonal isolation. But, if you want to retrieve it later on you put mechanical pull on it and, because it is all fragments of rubber, it actually falls apart and you can retrieve it without too much hassle.
“We are also creating e-zips where you no longer have to send your pipe to the factory to have the rubber baked on and the pipe sent back to you. We now get preconditioned rubber in which we have created a helical slot that you can wrap around the pipe on the rig floor. So, if you decide all of a sudden that you need a packer, you can take a slit e-zip out of the bag, wrap it around the pipe, put a bottom and a top cap on it and run it in the hole.”
This technology has been tested in a German quarry and is likely to come to market this year.
Swellfix is also about to market another development to overcome the problem of less than 100% fill with normal gravel packing. According to de Vries, mixing a small percentage of swellable particles with the gravel will ensure a 100% fill.
His laboratory is also working on swellable elastomers which work in saturated salts. “We have new developments in using them in saturated salts which was impossible until now because it is an osmotic process. We doped the rubber with salt so the fluid on the outside that makes it swell has to have a lesser salinity than on the inside. But, by playing with combinations of salts, we are getting close to being able to use it in saturated situations.”