The volume of water produced globally by oil and gas operations is staggering. The last major global study of produced water, dating from the late 1990s, estimated that the industry was bringing up 210m barrels of produced water each day. What’s more, that average is likely to have risen in the last decade.
WATER WASTAGE
High levels of impurities make this water an unusable by-product unless companies choose costly treatment processes to clean it up. Cost pressures, along with higher industry standards, are focusing the minds of many on finding new ways of addressing this issue.
“Produced water is the biggest waste stream from oil and gas production,” notes J Mike Stice, president of ConocoPhillips, Qatar. “Three barrels of water are produced for every one barrel of oil. Also, the water-to-oil-ratio worsens as well reserves are used up. It is very much an ongoing challenge for the industry from the perspective of cost and environmental performance.”
For some operations, particularly those working on coal-bed methane, the water to oil ratio is even worse at 3:1. Looking ahead, the industry’s environmental obligations are likely to grow larger, so there is growing impetus behind projects offering the prospect of a cost-effective, sustainable solution. This can be clearly seen in ConocoPhillips’ recently-announced investment in a Water Sustainability Centre (WSC) in Qatar.
The company hopes to provide a forum for experimentation, discussion, research and technology development that will drive efficiency in all approaches to the problem of produced water.
How well do you really know your competitors?
Access the most comprehensive Company Profiles on the market, powered by GlobalData. Save hours of research. Gain competitive edge.
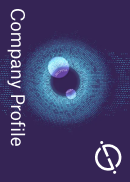
Thank you!
Your download email will arrive shortly
Not ready to buy yet? Download a free sample
We are confident about the unique quality of our Company Profiles. However, we want you to make the most beneficial decision for your business, so we offer a free sample that you can download by submitting the below form
By GlobalDataCHOOSING TACTICS
Essentially there are three possible approaches that projects at the WSC will strive to enable. The first and most obvious method is to limit the amount of produced water that is brought to the surface from a particular well.
The second option is to recycle and reuse the water by cleansing it of all contaminants. Theoretically, it should be possible to find a cost-effective method of purifying the water to a standard where it could be used for crop irrigation and as drinking water for animals or even humans. This may well prove to be the most expensive approach, but for some facilities it may be an appropriate choice.
The third option is to cleanse the water to a sufficient standard allowing its safe disposal into the ocean – though not to the same standard as water that is recycled and reused.
“All of these need technology to enhance water quality and in the case of individual production facilities it is important that the solution chosen is fit for purpose,” notes Stice.
The most likely outcome for any individual facility will be a blend of these solutions, which will be determined by certain parameters, such as its geographical location. On one hand, an offshore facility would seem to benefit from a strategy that limits the amount of produced water it has to manage. This would most likely be coupled with the discharge of cleaned, benign water into the ocean.
On the other hand, an onshore facility may be located in a dry, arid environment where water is a precious resource. In this scenario, a production company is more likely to target the highest level of cleansing, sufficient to make the water fit for agriculture or human consumption.
“Companies will use all of these approaches. It is not the case that one technique will emerge that will solve all the water management problems in the industry,” comments Stice. “Our industry – and ConocoPhillips itself – is at the beginning of understanding the produced water footprint of oil and gas production. The challenge is to develop and apply existing technologies to our problem statement. We’re making strides, but there is a lot to do.”
THE WATER SUSTAINABILITY CENTRE
ConocoPhillips is a major participant in Qatar’s oil and gas industry. It is the key foreign partner in the Qatargas 3 project, which is expected to produce 7.8 million tons of liquefied natural gas each year from 2009. The WSC, which is scheduled to open in the summer of 2008, is part of ConocoPhillips’s ongoing commitment to Qatar.
The home of the WSC will be the Qatar Science and Technology Park, which provides facilities, services and support for many technology companies from around the world that are based in Doha.
“The QSTP is state-of-the-art and it is great to be part of such a development,” states Stice. “It is a world-scale facility and we have 10,000m² of laboratory and office space there. It is a big commitment just to be here.”
Another benefit of being part of the QSTP is the collaborative environment that it engenders. This is important for the future of the WSC, which is very much a collaborative venture. ConocoPhillips is inviting stakeholders from the oil and industry to participate, but is also looking to involve other organisations in order to highlight and develop technologies that can treat produced water in a sustainable way.
“The WSC is a worldwide project for us and we will pursue companies that want to join us, in this industry collaboration, to achieve our primary goals,” comments Stice. “Our secondary focus, however, is on Qatari projects, mainly with municipalities and agricultural projects. This will include advice on water usage. We also want to collaborate with academia on pure research.”
Reaching out beyond the oil and gas sector could be crucial, as many existing technologies for filtration, for instance, have been developed for many non-energy projects. The WSC will look at other industries to find the most advanced technologies available and evaluate them in light of oil and gas producers’ specific needs.
“The WSC is about testing existing technological knowledge around filtration and the removal of metals from water,” explains Stice. “Our priority is to develop ways of removing contaminants from upstream-produced water and downstream refinery effluent. We must deal with residual oil, salts and heavy metals, all of which are addressed by technology from other industries that we can test and refine.” Desalination, for instance, has been an area of much investment over recent years, with huge projects under construction in the Middle East.
So far ConocoPhillips has backed the WSC – with funding of $25m over five to seven years – and the project will seek more funding from other sources during its lifetime. The company expects to see some notable impact from the WSC within the first two years, when research plans will be more focused and technology testing will be well under way.
The WSC will be designated as ConocoPhillips’s worldwide centre for water technologies, disseminating its findings to the company’s global operations as well as to local government and industry partners.
WAVES OF ENTHUSIASM
Judging by the reaction to the proposal for the WSC, it seems that ConocoPhillips has hit on an issue that is not only relevant to the industry, but is welcomed by a much wider community. Already the project has generated excitement among industry stakeholders and the general public around the world.
“There has been some really positive feedback from the industry, municipalities, ministries and the public,” says Stice. “The response has been overwhelming – far more than we anticipated. It shows that this is something the industry and the public are committed to.”
In Qatar specifically, community projects focusing on water management and sustainability are welcomed. ConocoPhillips feels these are important elements in its commitment to the region and as important as the efforts to improve efficiency and environmental performance standards in the oil and gas industry.
In backing the WSC, the company has recognised that it must balance the goals of the industry with the needs of the environment and the potential social benefits of improved water management. Its goal is to create solutions that will enable win-win scenarios around the world.
“We must consider the business aspect to ensure that solutions are cost effective, but at the same time we must look for the solution that best meets our needs, but is environmentally sustainable,” believes Stice. “We’re committed, we’ll stay the course and we know the project will make a difference beyond changing what the company does day-to-day.”
ConocoPhillips’ investment in the WSC promises many exciting prospects for the future, though the project has yet to launch. Work will begin in earnest once the WSC management team arrive in Qatar early in 2008 and starts focusing on the many areas of research with top-level expertise.
Certainly the oil and gas industry stands to benefit greatly from the collaborative effort the company is putting together, but so do other industries, communities and, of course, the environment.