Soon after I joined the offshore industry with my modest structural engineering skills I was asked to analyse and approve a drawing using large pieces of wood. I had done some work with reinforced concrete and steel but wood was a new one.
I quickly learnt the offshore environment is a tough one and even harder on the materials used, offering employees in the industry a wide range of challenges.
EXTREME ENGINEERING
Structural engineers in the offshore arena must deal with anything from the extreme and hard-to-predict loading, to the wet, corrosive, and often very cold, environment. On any given day there may be special demands and the repairs and replacements are usually expensive so there is a significant reward in getting it right.
Steel, man-made fibres, wood and syntactic foam are all material options and the material scientists, design engineers and those building structures for, and operating equipment in, the marine environment face a myriad of options. These of course all have to be balanced with the knowledge that weight is at a premium because many of the structures they are building are floating.
Taking account of where their work is situated can have a significant impact on the materials used and throw up a few surprises.
How well do you really know your competitors?
Access the most comprehensive Company Profiles on the market, powered by GlobalData. Save hours of research. Gain competitive edge.
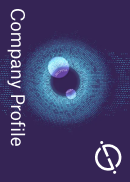
Thank you!
Your download email will arrive shortly
Not ready to buy yet? Download a free sample
We are confident about the unique quality of our Company Profiles. However, we want you to make the most beneficial decision for your business, so we offer a free sample that you can download by submitting the below form
By GlobalDataLow temperatures in projects near the poles impact on the choice of steel, while steels used in the production of oil and gas must withstand very high working temperatures and pressures, as well as resist the aggressive chemicals coming out of the reservoir.
Exotic steel materials are often used in pipes, either throughout the whole pipe cross section or as a liner. These materials come with their own set of welding challenges. Welding underwater (wet), or dry in underwater pressurised habitats is only successfully achievable after considerable experimental research.
Many offshore components are effectively monofilaments meaning a failure in one place could be catastrophic as there is no second structure to take the load, so their designers and inspectors have to take extra care to see that the material, and any joint, is of the right standard along the length.
WEIGHING IT UP
The weight of any vessel, including construction vessels is important and it is necessary to look at strength, capacity to float and transit, before even looking at a vessels ability to support the equipment it has on board. This applies to offshore platforms, subsea oil field equipment and subsea vehicles too.
Designers need to look to light but strong materials like aluminium and glass-reinforced plastic (GRP). While it is used in some offshore components aluminium provides a whole new set of challenges as it corrodes in the marine environment or in combination with other materials and it has fire risks.
Weight is also the reason for using syntactic foam. A number of components which are submerged, some up to 3km below sea level, require buoyancy. Building strong steel buoyancy boxes does not create enough uplift benefit because steel is so heavy. Such design specifications are tough to meet, especially over a long period of time.
Light and easy-to-mould syntactic foam should be robust and not easily damaged. It should also withstand multiple immersions or very long periods under water, often at significant pressure without breaking down.
Fibre ropes are also used with weight in mind. Steel rope is heavy and a very long rope hanging vertically down into the sea uses much of its tensile capacity supporting its own weight. This would not be satisfactory if an engineer wanted to lower a 300t structure 3km onto the seabed. Fibre ropes are neutrally buoyant so they do not pay this weight penalty but when you consider they need to be manufactured, stored and handled carefully to avoid damage or deterioration and deliver the designer’s desire, it gets interesting.
And then there is wood – a material used widely in temporary structures offshore. While temporary loads can be hard to establish engineers can design successfully if they have an adequate knowledge of timber quality and its characteristics.
While the offshore environment is a tough one throwing up any number of challenges on a daily basis, it also offers lots of surprises and the often exotic materials used are full of the unexpected.
Not only are the materials of great interest to those people producing them, but designing with them and using them also provides its own set of challenges.