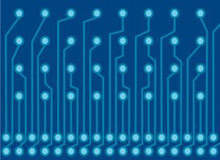
Oil and gas production from a cluster of wells is traditionally difficult to manage, due to the multiphase nature of the well fluids, skilled manpower shortages, field conditions and subsurface uncertainty. This can lead to late diagnosis of production problems, and manpower-intensive, slow and conservative handling of production constraints and restricted understanding of subsurface potential.
In operation since 2004, Shell’s software application FieldWare Production Universe (FW PU) allows data-driven well models to be easily constructed and updated from real-time production data, and thereafter applied to track well-by-well production for real-time well surveillance/optimisation. FW PU is cost effective in that it is a real-time software application that works mainly with existing infrastructure.
The simplicity and ease of application of data-driven techniques has also allowed extensions of the approach to a wide spectrum of applications, including the tracking of well production from subsea, smart wells and, for artificially lifted and EOR wells, for example, beam pumped gas lift, ESP, PCP and injection wells.
Advanced surveillance
The data-driven approach of FW PU takes full advantage of the well-test and production metering available in conventional production operations, eliminating sustainability issues associated with using physical models for well surveillance, inclusive of changing fluid properties, well conditions and instrumentation uncertainty.
Although the underlying algorithms are relatively complex, the FW PU application has straightforward graphical user interfaces that allow well-test data to be loaded and displayed, and well models configured, created, validated and brought online by operational staff. Well tests can be automatically uploaded into FW PU as they are conducted, ready for model validation or updating.
How well do you really know your competitors?
Access the most comprehensive Company Profiles on the market, powered by GlobalData. Save hours of research. Gain competitive edge.
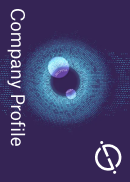
Thank you!
Your download email will arrive shortly
Not ready to buy yet? Download a free sample
We are confident about the unique quality of our Company Profiles. However, we want you to make the most beneficial decision for your business, so we offer a free sample that you can download by submitting the below form
By GlobalDataThe use of data-driven models for well production surveillance provides a number of advantages, one of which is that no numerical assumptions need to be made about the underlying physics or flow mechanics of the well or the composition of well fluids. Further, FW PU requires only repeatable well measurements; within limits, absolute measurement accuracy at the well is not critical.
Wide-scale roll out
The successful embedding of a real-time technology like FW PU allows for a step change in the level of production surveillance and the realisation of maximum value from its use is a non-trivial exercise. The software application needs to match the dynamic physical production elements (reservoir inflow, well performance, production processing and testing facilities) and the capabilities of the production staff, as well as their production management processes.
To date, FW PU has been installed for the surveillance of well-by-well production in more than 30 production facilities onshore and offshore worldwide, covering over 1,000 wells. FW PU surveillance covers a whole range of wells, including free-flow wells, gas-lifted wells, jet-pumped wells, ESP lifted wells, subsea wells, lean and rich gas wells and smart multizonal wells.
Operational optimisation
The FW PU data-driven models used to estimate well flow in real time can also be employed to generate predictions of well production using well control parameters, such as production choke position and lift gas injection rates. The FW PU Optimizer thus uses data-driven models to optimise estimated oil production from a single well by computing the choke or lift gas set points for maximum oil or gas production from that well alone.
FW PU can also be used to optimise the production of a cluster of wells subject to various well processing facilities or export constraints. Common optimisation problem formulations include:
- Maximising net oil production with limited liftgas, including partial gas-lift compression outages.
- Maximising net oil or condensate production while meeting gas export nominations, or sudden changes in gas demand.
- Maximising oil production subject to gross and gas-handling constraints, while maintaining a minimum level of water production for water injection, and minimising water disposal and gas flaring.
Given the above production targets and constraints, plus FW PU models of the wells and the headers, the FW PU Optimizer can then automatically compute optimal liftgas and/or production choke set points.
FW PU data-driven models are based on well testing, which is endemic to oil production, and as such are eminently sustainable and continue to be successfully operated since initial implementation over four years ago. Contrast this with physical models that have proven to be difficult to set up, calibrate, maintain and sustain in an operating environment.
Gas well modelling
Gas wells may have a wet gas meter on their flowlines, which in some cases are used in lieu of individual well testing. The well wet gas meter may be a simple orifice, venturi or a more advanced meter with dual differential pressure elements.
The meters often become oversized as the wells decline. Other issues include computing the wet-gas gas volume fraction (GVF) and estimating the densities of the individual components.
To overcome these problems, the industry typically reverts to tracer testing or the use of mobile temporary well testing skids, both of which are costly and cumbersome.
To address these issues, in the absence of dedicated test facilities, FW PU uses the aforementioned data-driven modelling techniques on the commingled well production data from the production separator to estimate gas and liquid production rates for all of the wells, all of the time.
The approach is as follows: each of the gas wells is modelled by deliberately perturbing individual wellflows and correlating the changes in the well wet gas flows and pressures with corresponding changes in the bulk gas, oil and water flows. This can also be done on an opportunity basis using data from plant startup when the well is progressively ramped up to full production.
These techniques have been successfully applied to continuously estimate gas well flows and CGR and WGR ratios for several locations.
Multizonal production estimation
The increasing number of extended reach multizonal or multilateral well completions pose production monitoring and management challenges. It is important to obtain accurate estimates of the production of oil, water and gas for each of the zones in an extended reach well to efficiently manage the production profile throughout the well and to obtain the full benefits of the well’s extended reach.
While these wells will have surface well-test facilities, the challenge remains as to how to efficiently test and characterise the individual zones, and to track their production during normal commingled production.
The latest extended reach wells are ‘smart’ in that they include tubing and annulus downhole pressure gauges and also surface-adjustable inflow control valves (ICVs) for each zone. Given the zonal tubing and annulus downhole pressures, and the associated inflow control valve openings, and using the same principles as outlined previously, FW PU data-driven models may be generated for the individual zones of a multizone well.
The FW PU models are then able to provide estimates of production from the individual zones in real time, working from the real-time downhole gauge readings.
In order to build the FW PU data-driven models for the zones, it is necessary to carry out a series of specifically designed tests whereby individual zones and combinations of zones are tested using the well-test unit.
These tests capture the characteristics of the individual zones, as well as interaction between them. In a combination of surface production choke valve (FCV) changes and downhole ICV changes, both individual zones and combinations of the zones are tested.
From the tests, a FW PU model is derived to continuously estimate individual zonal production for oil, gas and water. These models also capture the interaction between the zones and are used to compute optimal settings for the aforementioned ICVs.
Local well controllers for beam-lifted wells
Almost all beam lift pump-off control units rely on the interpretation of rod load versus displacement of the walking beam. From these measurements, pump-off can be locally detected by a number of strategies.
An investigation was initiated to apply the FW PU data-driven modelling capabilities to update beam-pump surveillance and optimisation capability. A series of tests on wells in the Far East and Europe were conducted over a number of years.
The net result was a locally mounted control and optimisation panel, the Advanced Local Well Control (ALWC), which uses data-driven models; a radically different approach to commercially available equipment. Working with this set of instruments has the advantage that all instruments are commonly available, cost effective, sustainable commodities located at ground level for easy maintenance and calibration.
In comparison, the conventional beam lift instrumentation is more specialised and vendor-specific. ALWC capability includes:
- Pump-off detection from the power and flow line
Differential pressure models - Continuous production estimation from the flow
Line differential pressure and power models.
The auto-optimisation capability of the control unit was also developed by applying techniques designed for FW PU. By having an accurate estimate of well-fluid production from the differential pressure/power models, it is possible to allow the controller to vary the ‘off time’ for the unit after pump-off detection and determine the optimum off-time setting.
Application to a 1,600m-depth gassy well gave the following results:
Change in well-cycle time – from four minutes on and 15 minutes off to 15 minutes on and 30 minutes off – resulted in a significant reduction in well cycles per year, with a consequent expected reduction in mechanical and electrical failures due to startup and shutdown stresses.
Production increased from 13m3/d to 20m3/d, along with a 15% power savings due to electrically balancing the unit.
Pump-off detection was almost impossible to set with the originally installed Rod Pump Controller; however, pump-off was consistently detected by the ALWC.
The normal functionality of a rod-pump control unit in terms of alarm limits, protection and communication are also provided in the ALWC. The optional introduction of sound sensors potentially allows the sound fingerprint of the unit to be logged while the unit is operating optimally.
This fingerprint can then be used to detect faults, such as belt slip or sheared foundation bolts.
Improving intermittent gas-lift operation
A trial project applied Plunger Assisted Intermittent Lift together with a smart local controller. The local control unit uses some of the FW PU data-driven modelling and optimisation techniques.
The net result is a control unit that delivers increased production and a reduction in gas lift.
The controller is fully automated in terms of well production optimisation and gas-lift management. It incorporates auto-restart features and relieves the operators of most of the tedious aspects of operating intermittent lift wells.
The control unit also synchronises lift from different wells, so that the slugs from the wells do not coincide, as this can possibly flood the production separation facilities.
Conclusion
Data-driven modelling techniques have the potential to significantly improve surveillance and optimisation in oil and gas production operations. To date, the FW PU application has been installed for the surveillance of well-by-well production in more than 70 production facilities onshore and offshore worldwide, covering over 1,000 wells.
The wide-scale roll out of FW PU is systematically conducted and builds on the long Shell experience with real-time production-operation applications. FW PU surveillance covers a whole range of wells, including free-flowing wells, gas-lifted wells, jet-pumped wells, ESP-lifted wells, subsea wells, lean and rich gas wells and smart multizonal wells.
While the roll out of FW PU continues, there are also many possibilities for the extension of the data-driven modelling framework to address other significant gaps in the daily management of oil and gas production operations.