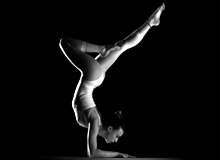
There are several different methods Shell undertakes to ensure safety and efficiency for all its operations. But as with most balancing acts, one side outweighs the other.
“Safety is our top priority, it’s entirely supported by our senior management and CEO, we are safe guarded from budget cuts – we do have pressure to make sure we’re being as efficient as possible, but safety is always a top priority,” says global discipline head of logistics and production supply chain for Shell E&P, Dirk Kramers.
Harsh environments
In today’s climate, exploration and production companies are forced to operate in less hospitable and harsher environments across the world. As with all other operations, transport and logistics has its own issues in making sure all materials and staff arrive safely and its operations is run as safely and smoothly as possible.
There are two key ways that Shell looks at tackling this issue. There are the planning initiatives and then the more hands-on systems it deploys.
The Zero Goal Must Win initiative was introduced two years ago when they discovered 70-80% of exploration and production fatalities came from road transport. “That was our biggest area of concern, we have seen a reduction in fatalities, but we still have too many incidents and accidents but fortunately the severity is less that it has been in the past,” explains Kramers.
How well do you really know your competitors?
Access the most comprehensive Company Profiles on the market, powered by GlobalData. Save hours of research. Gain competitive edge.
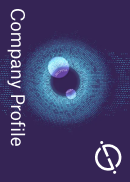
Thank you!
Your download email will arrive shortly
Not ready to buy yet? Download a free sample
We are confident about the unique quality of our Company Profiles. However, we want you to make the most beneficial decision for your business, so we offer a free sample that you can download by submitting the below form
By GlobalDataTransport safety hotspots for Shell include areas that not only have infrastructure challenges to contend with, but also a large variety in the social and political climates. For example its operations in Nigeria and Algeria pose several issues for the company on a security level.
“If I look at Nigeria – there the challenge is around security and road infrastructure. Unfortunately there is still hostility in Nigeria where people are aiming for our cars and, combined with a poor road infrastructure, this requires a differentiated approach. A good example are the trucks on the road that we don’t think meet the required safety standards from an equipment as well as a driver capability perspective, so when these trucks get into difficulty, the chance that they’ll seriously injure someone is quite high there, and the past proves this, hence our driver training needs to address this.”
By working with local governments and key institutions relevant to culture, Shell is making clear progress. “We had a campaign jointly with the government in Brunei called ‘tell a friend’. We said to every individual in our company, tell your friend that they should wear a seatbelt and you want him to come home safe then ask your friend to tell someone else, you’ll be amazed how quickly the word spreads.”
Understanding cultures
It seems Shell is able to infiltrate all areas of culture in the name of safety, and it’s working. “A good example is in Oman, where we do more than 220 million kilometres a year. Many Omanis still don’t see wearing a seatbelt as a necessity. So in the event of road traffic accidents we still see too many serious and fatal injuries. Standard campaigns unfortunately had a limited effect and as such we started to engage the religious community in conveying the message during prayer times in the mosques,’If you purposely expose yourself to these kinds of dangers and you are killed that’s not in line with the preaching of Allah,’ and it worked.
“We try to understand the local culture, to understand where we have the influence and then have discussions with people in that country to find the best ways to start discussing that. There’s no one solution that fits all.
“In Russia our plans have worked quite drastically, we’ve seen an enormous tail off in fatalities there, where one of the main causes of accidents was an alcohol problem. In the areas where we operate in Siberia and Sakhalin there was quite a habit of consuming alcohol shortly after (and occasionally during) working hours. Drinking vodka after work was a social event and a lot of people didn’t realise that the next morning they could still be intoxicated, the alcohol was still in their system. As such, drivers can’t react properly and with icy conditions that they often have in those regions it’s a recipe for disaster. By the introduction of mandatory alcohol tests, awareness campaigns and rigorous consequence management it has now been reduced dramatically and we haven’t had a fatality for six months,” says Kramers.
At the height of the project Shell increased alcohol testing to around 16,000 pre-drive checks, 9,000 semi-random checks and 100 totally random checks every week resulting in resounding success.
It is clear that once there is an understanding of what’s best for the company and the local people, that it is then important to create an infrastructure to keep this good will and change in attitude working. This is where IT development comes into play.
In order to monitor its drivers, Shell works hard to create an economical and effective monitoring system. In-vehicle monitoring systems are already on the market in several forms, including GPS tracking, behavioural pattern monitoring, and systems looking out for hazards and danger points on the road, but Shell is working to create a system that has all these capabilities in one device.
This is in order to monitor whether a driver is wearing a seatbelt, how many hours they are driving for, how fast they are going, how fast they are accelerating and decelerating. “It’s like a black box on a plane, we can download all those parameters to see, for example, how fast they have been driving and then go back to the driver and explain where they’re going wrong, as such changing their behaviour” says Kramers.
Hot spots
Shell wants to extend this technology to a single device so that in each of its countries it can connect any known safety hotspot to a planned journey and provide the driver with a direct insight into those hotspots.
“If there’s a dangerous bend in that road or a crossing – or if the driver is about to go into an area with a dense population, then the system will sound a warning. It will say, ‘dangerous bend ahead’ as it has built-in GPS tracking,” says Kramers.
“We know exactly where he is. The system could give a verbal warning saying: ‘Be careful, slow down, you’re entering a residential area’.
“We noticed that some of our fatalities involved extremely experienced drivers who had been driving in the area for five or ten years and as such you would expect great performance. This is however not the case and the reason behind this is they go into automatic pilot on a route they are used to driving every day. We are trying to get this device at a very low cost, and we are working with some technical providers to see whether or not we can use current technology and make it very cheaply available to us as we want to deploy it to thousands of vehicles. Our hope is to aid the driver in improving his driving behaviour.”
Shell is close to achieving its goal – the individual components are ready, but it’s waiting for a unit that integrates all components. The systems are currently between $2,000 and $3,000, which Shell aims to bring down to around $500 a year for the unit and its supporting management system.
There is due to be a prototype up and running at the end of March and then an approved concept will be trialled in Oman with a few hundred cars at the end of Q2.
Shell’s more holistic approach is also demonstrated by its investment in a Global Logistic Management System (GLMS).
It is working closely with software provider IBS to get the product covering the full spectrum of logistics in an oil and gas business environment and into a commercial product so it can be sold to other oil and gas companies.
“There is at present no integrated fit-for-purpose system available that connects people and materials’ movement by aviation, marine and land in one piece of software,” explains Kramers.
“We have to make sure that people and their materials can travel from one location to another with ease, for example when staff have to go to an area such as Sakhalin, in Russia, that’s not an easy task.
“There are several factors to take into account. Staff need to have work permits before being allowed entry into the country. When the engineer comes into the country he needs a hotel room as he often can’t fly offshore on the same day – and before we book the individual to go offshore, we need to check whether he has the appropriate training certificates. Everyone that goes offshore needs to have survival and helicopter escape training. Once we have all the confirmations we are then able to book him on one of the scheduled flights going to offshore locations.
“Once we’ve booked him we then need to make sure that he has his materials to work with, we don’t want him to be sitting offshore for $1,000 a day doing nothing. Hence we have to make sure that the materials are there when the engineer arrives. We are not 100% there yet, but getting close. The products are developed with IBS, for which we pay them a licence fee and they committed to commercialising the product on the market place as we try to make this an application adopted industry-wide.”
Way to go
Kramers makes it clear that there is still some way to go, and that there will always be a human element to ensure logistics function as they should. “We still need to apply common sense,” he explains.
“The system isn’t attached to the World Meteorological Organisation for example, or configured to pick up regional weather warnings; we still rely on our staff to gauge the weather warnings and to make the call whether the operation scheduled in GLMS can go ahead.
“An excellent example of how we’re using it in this respect is a recent helicopter accident in the Gulf of Mexico. We decided to stand-down all the same type of helicopter as we didn’t know why the helicopter went down. We then used the same system to book and transport people by boat as if they were being booked and flown in, demonstrating the great flexibility we have build into GLMS.”
The GLMS ties in directly with another process called cognitive risk assessment where the company can compare various modes of transport. Kramers gives the example of a 600km journey, where the decision concerns if staff should travel by bus or plane.
In Europe, 600km isn’t a great deal of exposure but in Algeria for example, there’s a lot of hostility in the interior and one would rather opt for the plane to reduce security issues to as low a level as possible. These everyday decisions that are based on all factors are needed to make sure the safest and most efficient transport methods are used.
Kramers has made it clear that in any of Shell’s operations, safety of staff and local residents is the main priority. Unfortunately there are several ways that their safety can be compromised.
Whether this is self-inflicted by cultural differences, unsuitable equipment, or external factors such as political or social unrest, Shell is doing everything in its power to not only ensure the safety of its employees, but also the residents of these countries. As any one fatality is one too many, other companies should heed his words.
Five charters of the Must Win Goal Zero initiative
- Reduce land transport exposure
- Enhance driver behaviour
- Enhance competency and capability of contract holders
- Improve vehicle safety
- Implement recognition and consequence management
Programme elements and scope
- Reduce land transportation exposure, e.g:
– Reduce kilometres driven
– Safe Journey Management - Enhance driver behaviour, e.g:
-Defensive Driving Training
– In-Vehicle Monitoring System
– Road Safety Monitoring Teams - Improve Contract Holder competency and capacity
– Link with Contractor HSE Management Must Win - Implement recognition & consequence management
– minimum offences: seatbelts, alcohol/drugs, speeding
– Applies to driver (staff and contractor), supervisor, manager,
contract holder / owner
– Balance rewards with consequences - Increase vehicle safety
– Along EP2005-0261 Standard
The programme has a global reach and has 5 focus areas in scope
- SPDC (Nigeria)
- PDO (Oman)
- SEIC (Sakhalin)
- SPD (Salym)
- EPX (Exploration)