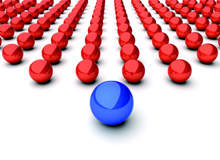
"Excellent testing facilities combined with analysis tools and world-class knowledge." These, says Stein Olav Drange, research and development (R&D) manager at StatoilHydro, form the basis for all technological advances.
"For us this is the only way to develop technology. It's very challenging with subsea compression but we have specific programmes and we progress from step to step in a very consistent manner. It's checking and its learning, and if we need to do tests for a little longer, then we will."
K-lab laboratory
The maximum operating pressure in the multiphase loop at K-lab is 150bar, with flow rates up to 6,000Am³/h gas and 150Am³/h liquid. K-lab, StatoilHydro's measurement and technology laboratory at its Kårstø facility north of Stavanger in Norway has one of the world's most sophisticated test facilities for this type of wet gas equipment.
As the closest neighbour to the gas processing plant there, K-lab has unlimited access to gas for testing, direct from various fields on the Norwegian continental shelf (NCS). It is now possible to conduct full-scale onshore tests under conditions almost corresponding to normal seabed operation.
"K-lab is a world-class facility that can analyse, test and qualify various types of gas processing equipment – including subsea compressors and pumps, high-pressure separation units, multi-phase meters, valves and pipeline pigs – all in full scale," explains Trond Austrheim, K-lab manager with StatoilHydro.
How well do you really know your competitors?
Access the most comprehensive Company Profiles on the market, powered by GlobalData. Save hours of research. Gain competitive edge.
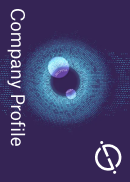
Thank you!
Your download email will arrive shortly
Not ready to buy yet? Download a free sample
We are confident about the unique quality of our Company Profiles. However, we want you to make the most beneficial decision for your business, so we offer a free sample that you can download by submitting the below form
By GlobalDataStatoilHydro has developed a new technological strategy for its business. "We have a lot of exciting projects going on," Drange tells us, "but we have to stay focused on four specific areas." They are:
- resource replacement; finding new resources to be able
to keep up with and preferably increase production - field development in harsh environments
- heavy oil on and offshore
- climate challenge.
Drange explains that the company is always conscious of the commercial focus for any project. "As is the case with any production company, we have to ask how we can increase our production and the amount of oil and gas we are extracting from the ground. We have a production level of 1.9m barrels of oil equivalents a day (bpd) and the ambition is to have an equity production of 2.2m boe per day in 2012.
"There are two aspects: to find new resources with exploration to be able to keep up with current levels, and to increase production from producing fields – IOR. Subsea processing, compressors, multi or single phase pumps, raw seawater injection are important technologies to manage this."
Cooperation
But this is only the beginning of the story in terms of the subsea work StatoilHydro is doing. "We launched a project in April last year with the aim of demonstrating compact inline multi-component integrated gas leak with separation systems" Drange explains.
"We are now working with Petrobras and Chevron building specific test facilities, so we can test different components and change various elements to see what we can achieve and make sure the products and technologies are reaching their targets.
"We also have the possibility of testing the equipment offshore topside in a working environment on real well streams. I can't stress enough the importance of cooperation between R&D and the field units; we need each other in order to progress."
The main subsea processing realisation project for StatoilHydro at the moment is the Tyrihans raw seawater injection project.
"We are installing two subsea pumps in the field for raw seawater injection. It's the first time in the NCS that's going to happen. The water will be injected into the reservoir to improve recovery in the field. The water will be injected into the reservoir to improve recovery in the field. The pumps will be installed this summer and then put into production in March 2010. The pumps are 2.5MW each, and the tie back length is 31km. This is the most cost-effective and efficient way to increase production."
The organic process of research and development at StatoilHydro is a success as it plays on the company's strengths.
Great potential
All new technologies in this field are difficult to manufacture and use throughout the industry, although there is great potential. "They are all field specific, but have the potential to be used in other applications. The compact separation technology that we develop is mainly for subsea use, but it may also be a good alternative for topside facilities. We have proved this technology is compact, it's low weight, the separator doesn't know if it's in 3,000m of water or anywhere else for that matter, the potential is there."
Other applications include revisiting sites that have otherwise been left dormant. "All fields are specific, so it's hard to put a number on the exact amount that they may increase recovery using subsea processing," says Drange.
"For subsea tie-backs it's also about adjusting your well head pressure to a level that fits the inlet pressure at your host platform."
R&D financing
Any research and development is going to cost a great deal of money. Testing facilities, expert engineers and time on offshore facilities are a huge expenditure.
The risk is making sure the finished technology or product will pay for itself, but there is a fear in all industries at the moment that innovation and long-term strategies are at the bottom of the list of priorities.
Drange isn't worried. "It's obvious that we have to be more cost-efficient in our thinking but regarding our R&D budget, nothing has been cut so far. Of course we have to be prepared for rapid changes in this volatile market and there's obviously a huge difference in mentality when the oil price is $140 compared to $40, but what is important to us is that our strategy is set at long-term goals. In the worst case it may be necessary to reduce the speed of development but we're going in the same direction and we have the same goals, and that's not going to change. So far we've not been restricted. We have the same budget and plan as we did before the financial crisis came about. The main thing is that we have to be more cost efficient in our thinking."
StatoilHydro has proved that when it comes to technological advances, planning and testing facilities are invaluable. These facilities are without doubt the basis of successful R&D results within subsea processing.
The organic process and allowing creative and constructive thinking are the keys to tangible results, while keeping well-structured and progressive scheduling. There is a great deal of whispering in the industry that these processes can change the face of extraction.
StatoilHydro has shown that, in order to stay on top of the game, investment and cooperation are paramount. We should all be making the most of an industry that still has so much to give.
At a glance: K-lab
K-lab Metering and Technology Laboratory was founded in 1988 at the Kårstø Gas Process Plant as an accredited laboratory for the testing and calibration of dry gas meters. Unlimited access to high-pressure natural gas and condensate has since made the laboratory a unique test facility worldwide.
By utilising natural gas, condensate and water at high pressure and at large scale, the test equipment can be tested in the same operating conditions it will face at a later stage, when installed at its final destination.
K-Lab has throughout a number of years carried out R&D and qualification of process equipment such as multiphase-meters, high-pressure separation equipment, pipeline pigs and various types of valve. A recent major upgrade of the test facility has made K-lab the first facility in the world for testing and qualification of subsea compressors.
In addition, K-lab has executed several tests on an array of issues, including CO2 removal, hydrate formation, membrane technology for dew-point control and the effects of drag reducing agents (DRA).