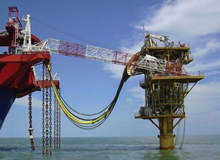
The Girassol field was discovered in April 1996 by Elf Exploration Angola. Just over two years later, on 8 July 1998, the company obtained the official go-ahead from Angola’s national oil company, Sonangol, and the Girassol partners to launch a development project.
The Girassol project, which is the first field on Block 17 to go into production, is an outstanding technological achievement in terms of the size of the deposit, the water depth and the degree of innovation required to exploit the reserves. Girassol is located in 1400m of water 150km off the coast of Angola, between Soyo and Luanda. The very extensive field (14km by 10km) is made up of extremely permeable Tertiary sand reservoirs containing very high-quality 32° API crude, resulting in good well productivity.
Following the major discoveries on Block 3, where exploration began in 1981, it occurred to geologists that the outer zones of the Congo river delta might contain hydrocarbon deposits. However, since the discoveries in the Pinda zone during 1990–91, exploration results in Angola had been disappointing.
The year 1992 saw the awarding of a number of new blocks further off the Angolan coast. Bidding was lively, with the earlier discoveries in the area arousing the interest of UK and US oil companies, such as BP, Shell and Amoco. However, Elf was awarded the right to operate Block 17 and it became a 10% partner on Block 16 (operated by Shell). This allowed the company to enhance its skills by cooperating with experts working for other international oil companies as well as the national company Sonangol.
After an encouraging discovery on the Bengo field and positive indications from the Margarida well, in April 1996, Elf positioned itself as an authority on the local Tertiary thematic and achieved a positive result on the first well drilled on Girassol.
RAPID PROGRESS
How well do you really know your competitors?
Access the most comprehensive Company Profiles on the market, powered by GlobalData. Save hours of research. Gain competitive edge.
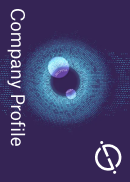
Thank you!
Your download email will arrive shortly
Not ready to buy yet? Download a free sample
We are confident about the unique quality of our Company Profiles. However, we want you to make the most beneficial decision for your business, so we offer a free sample that you can download by submitting the below form
By GlobalDataWith the discovery of the Girassol deposit, things began to gather speed. A 3D seismic appraisal covering 1100km² and involving onboard data processing was soon carried out, and immediately afterwards a multi-discipline project group was set up, bringing together 3G specialists, geologists, geophysicists and reservoir engineers, as well as a petroleum architect and a number of drilling, production and construction experts.
The first task was to interpret the seismic data to determine the optimum position for the first and subsequent appraisal wells, and then to evaluate the accumulation as a whole and estimate the recovery factor. At the same time, conceptual studies were undertaken to devise a production scheme that would overcome the specific problems related to the water depth.
In an unprecedented move for the group of companies developing Girassol, an upstream project team was set up well before the project entered its development phase – only three months after striking oil and even before appraisal was fully completed – thus allowing more rapid progress to be made during the conceptual phase. Girassol was to be the first in a long series of discoveries, which would include Dalia, Rosa, Lirio, Jasmin and Perpetua.
FAST-TRACK APPROACH
One of the distinguishing features of the Girassol project is the fast-track approach that was used in development. Fast-track development allows better time management, which can have a major impact on project economics. With a fast-track scheme, instead of proceeding in sequence, several phases – appraisal, 3G studies, petroleum architecture studies – are carried out concurrently, meaning that the development scheme can be decided much earlier.
With a fast-track approach, all the relevant experts are brought together in an integrated organisational structure together with the petroleum architect, who carries out his studies in this rather unusual context while ensuring that all technical decisions take into account all the uncertainties and risks.
Such an approach requires rapid and efficient information flow between the various players involved, so that each is informed about any areas of uncertainty or hypothesis regarding the parameters he is using. Each individual must realise the potential impact on the other players of any changes in the data they provide.
When faced with a technological challenge or a major innovation deemed to be essential to the project – as was the case with Girassol – the fast-track timetable must provide for equipment qualification before the construction phase begins. It is also preferable to allow for a consolidation phase to take stock of reservoir studies, petroleum architecture studies and progress in the development and construction process.
To reduce the number of interfaces involved, the Girassol development project was divided into four large packages covered by separate contracts: drilling; the subsea production system (SPS); the umbilicals and flow lines (UFLs); and the floating production, storage and offloading (FPSO) unit. Following a call for tenders and a design competition, contracts for the FPSO and the UFL were awarded to two major consortia.
DEVELOPMENT PHASE
The development of Girassol involves two phases. Phase one, covering development up to first oil, involved bringing into operation 11 out of a total of 39 wells. When all 39 are operational, Girassol will comprise 23 producer wells (some of which will produce more than 35,000 barrels per day each), 14 wells for water injection and two for gas injection. Phase two covers all the remaining wells as well as the installation of the relevant flow-lines and umbilicals.
The overall project budget is $2.8bn, of which three-quarters is required for phase one. When official approval for the project was obtained in July 1998, the Girassol partners and Sonangol set Girassol in motion by confirming the award of three major contracts, totalling more than $1.5m.
Between 5% and 10% of the world’s reserves of oil, amounting to some 100 billion barrels, are thought to lie offshore in more than 500m of water. But gaining access to the Girassol’s treasure hidden beneath the waves involves overcoming a number of obstacles. Hydrocarbon production is still limited to water depths up to 1800m.
Girassol is an extremely complex project which was launched before all the required techniques had been developed. To produce the Girassol reservoir, the project team had to install a wellhead and gathering system in 1400m of water, connect up hundred of pieces of equipment without help from divers, and set up risers to bring effluent up to the FPSO.
Drilling on the Girassol field was carried out by drilling vessels with a dynamic positioning capability. These ships, equipped with variable-speed thrusters for greater stability, were specially built for the exploration and development of Block 17.
The subsea production systems (SPS) comprise well manifolds, wellheads, ‘Christmas trees’ and the well jumpers connecting the well to its manifold. The Girassol development scheme involves a network of 39 subsea wells all tied in to the FPSO: 23 producer wells, 14 water injectors and two wells for injecting the associated gas produced during processing of the crude.
No less than 13 subsea manifolds and their associated control systems were installed on the seabed. All in all, 500 separate valves are needed to control the circulation of the various fluids between the subsea wellheads and the surface facilities.
To maximise productivity and reduce the number of wells necessary, Girassol drillers used horizontal drilling techniques, and some of the 39 wells will be capable of producing up to 35,000 barrels per day.
The Norwegian-made Christmas trees, which can withstand very high pressure, are designed to control the flow of effluent coming out of the reservoir and to shut down the well if necessary. The first wellheads were subjected to rigorous testing, both at the factory and in the deep waters off the Norwegian port of Bergen.
Each element was very carefully inspected because at depths greater than 1000m the only way of operating valves is by remote control or by using a submersible robot. Any equipment malfunction would require the whole wellhead to be raised to the surface, which would involve considerable cost.
The wellheads are linked to the FPSO by a network of subsea flow-lines, designed to take account of the low temperatures encountered at great depth.
LOW-TEMPERATURE SOLUTION
Solving the problem of low temperature was crucial to success at Girassol. The seabed temperature is only 4°C, and it is absolutely imperative that the crude be maintained at more than 40°C until it reaches the FPSO, mainly to avoid the build up of paraffin and hydrate deposits that can cause flow-line blockages.
The temperature of the crude when it leaves the wellhead – about 65°C – is not particularly high. If standard, non-insulated steel tubing was used for the flow-lines, the temperature would fall quite rapidly, losing 18°C for every kilometre of flow-line. Given that some of the flow-line bundles are up to 7km long and that the risers are 1.3km high, this was unacceptable.
In addition, thermodynamics during transit up the riser means an unavoidable loss of 10°C, leaving only an 8°C loss margin during transport from wellhead to riser. That means the oil must not lose more than 1°C per kilometre travelled.
The solution was to use heat insulation in the all subsea system components, especially the flow-lines. The insulation material had to have three properties:
- The thermal insulation and inertia capacity to maintain temperature for a production shutdown of at least 16 hours
- The ability to resist pressure of 140 bar
- Weight reduction buoyancy
The solution selected was high-density syntactic foam, which has an insulation capacity 500 times greater than steel.
UMBILICALS AND FLOW-LINES
The subsea production network which links the well heads to the FPSO, comprises both umbilicals and production lines, usually referred to as flow-lines. The umbilicals and flow-lines (UFLs) comprises 45km of production lines, 33km of injection lines, three risers towers and 77km of umbilicals. In addition, flexibles are used to link the risers to the FPSO and to transport the crude across to the loading buoy for export by tanker.
The production lines were designed in loops to facilitate pigging and to allow the lines to be filled with inert storage oil in case of a production stoppage. The UFL network has six separate production loops, with one being reserved for subsequent development. Each well is connected via a manifold to one of the loops, which are all tied in to one of the three riser towers.
The subsea lines were assembled at the project’s Soyo yard on Angola’s northern coast. The network was assembled in eight bundle sections between 800m and 2.9km in length before being towed along the seabed to the Girassol site.
One of the most critical phases of the project was the positioning of the various lines on the seabed and their connection to production equipment. They had to be positioned very precisely using acoustic transponders placed on the seabed. The connections were controlled from the surface using two remotely operated systems: a modular advanced tie-in system (MATIS) for the flange connections between lines, and a connector activating tool (CAT) for connections involving subsea manifolds and wellheads.
THE RISER TOWERS
Riser towers are vertical structures some 1250m high and bring the effluent up from the seabed to the FPSO. The design of the risers was the result of detailed study and testing to verify the thermal insulation of the syntactic foam. The towers were assembled in Angola, at a specially equipped coastal construction yard at Lobito.
The riser towers are one of the major innovations of the Girassol project. Each riser comprises four production lines and two water or gas injection lines. The production lines are tied in to the subsea production loops so that pigs can be sent down regularly from the surface to ensure free flow by dislodging any paraffin deposits that may have formed on the inside walls of the lines.
Each production loop also includes a line that can, when necessary, be used to inject methanol into the network to ensure that the natural gas contained in the crude does not solidify as hydrate ‘ice’ at low temperature, thus blocking the flow. Furthermore, to maintain pressure in the reservoir, seawater is injected to replace the crude oil that is extracted, and the gas separated from the crude aboard the FPSO is re-injected instead of being flared, thus reducing the generation of greenhouse gas emissions.
The 1250m riser towers were towed semi-submerged from the coast to the Girassol site. A special 600km itinerary was chosen to minimise the stress from waves and currents during the sea crossing. Towing each riser to the site took only five days, and despite being a world first, the installation operation required only a few hours.
Once at the production site, each riser was tilted to vertical using a counterweight. The operation was constantly monitored using sensors on the riser itself, and the lower section of the tower was controlled with cables attached to surface vessels with a dynamic positioning capability. Once the riser was attached to its suction anchor,
it was kept vertical by the upper float and the syntactic foam.
The wellheads are installed on the seabed and connected to the surface facilities by flexible tubing systems. The risers that bring the effluent up to the surface are designed to handle extreme ocean states and weather conditions.
LARGE-SCALE FPSO
The FPSO comprises a seawater desulphating unit; an oil treatment and stabilisation plant; pumps; generators; and oil storage tanks. The combined plant can process up to 200,000 barrels per day of crude oil, desulphate and re-inject 400,000 barrels per day of seawater and store two million barrels of processed crude. The oil is then piped to the offloading buoy moored 2km from the FPSO.
The FPSO takes the crude oil aboard, processes it to remove the gas and water, and then pipes it aboard tankers moored nearby for export. There are currently some ten production schemes worldwide using the FPSO principle, but none of them are on such a large scale. The process deck was originally intended to be built at the French port of Marseilles, but in July 1999 construction was transferred to Hyundai’s Ulsan shipyard in Korea where the FPSO’s hull was already taking shape.
The key feature of original plan was to build the process deck, with a design weight of 20,000t, as a single integrated unit 180m long and then skid it onto the storage part of the completed hull.
That plan was later modified, with the process deck, now with a design weight of 25,000t, being assembled on the hull in sections weighing no more than 350t each. The whole deck was built and assembled at Ulsan in only 21 months. The hull itself, weighing 42,000t, was floated out of its construction drydock in July 1999, and fitting-out was completed by October in the same year.
On 30 March 2001, the world’s largest floating production facility began its long journey to Angola towed by three tugs. On 11 July 2001, after a voyage lasting over three months, the FPSO arrived at the production site and, over the following weeks, the vessel was moored to 16 separate suction anchors. Each anchor is 17m high and attached to the vessel by a 120mm sheathed cable 1.8km long, with a length of chain at each end (650m at the seabed and 200m at the surface).
OIL EXPORT SYSTEM
Once the loading buoy, which measures 19m across, had been towed into position at the site, it was anchored via its own mooring system 1.4km from the FPSO. Rigid polyester lines completed by lengths of chain were used to moor the buoy to its suction anchors, with each separate mooring made up of 1.5km of 145mm polyester cable plus 300m of chain linking it to the anchor and 150m of chain to the buoy. Cable was used to save weight – it weighs 15kg per metre out of the water but less than 4kg once submerged, compared to 140kg (out of the water) for 80mm mooring chain.
Once the buoy was in place, the offloading pipeline was rigged from the FPSO to the buoy. The standard technique for offloading buoys is to run the pipeline from the FPSO down to the seabed, across the intervening gap and then up to the buoy.
Girassol planners chose the simpler solution of using semi-submerged lines. Two flexible 16in pipelines, one 2400m long above another 2750m long, were slung across semi-submerged in a twin-loop ‘W’ configuration, supported in the centre by 29 flotation modules. In normal operation, the highest part of the ‘W’ lies at a depth of 340m and the deepest part of the lower line reaches 690m.