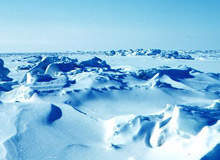
World Expro: To what extent has a growing shift towards high pressure / high temperature (HPHT) environments changed your role?
Giovanni Botto: Eni has quite a history of HTHP exploitation. In the 1990s we started the production of a field in the Po Valley in north-western Italy. The temperature there exceeded 180°C and the pressure was above 12,000psi. More recently, it is worth mentioning Kashagan, a high-pressure field in the north Caspian Sea with a lot of hydrogen sulphide, as well as some assets in the Gulf of Mexico and offshore Egypt.
We know that we are moving towards more extreme environments: hotter reservoirs and lower temperatures outside – I’m thinking of the Arctic operations especially and unconventional (for example, extra heavy oil, tar sands) reservoirs. The overall role of R&D is not changing, but our responsibility is shifting increasingly towards these more difficult conditions.
Where has that seen most of your attention focused lately?
The most comprehensive effort ENI has developed in recent years for facing challenging environments is the development of a proprietary near-balanced drilling system. It is a closed-loop system, able to analyse real-time drilling data to detect kicks or losses, and keeps continuous circulation in the well.
The project is virtually complete following testing in several places and, for us, it holds the key in extreme environments. It was assembled in-house so as to get some competitive advantage out of this technology, but we have not gone through a full commercialisation phase yet – it was developed using some sub-systems from external providers.
How well do you really know your competitors?
Access the most comprehensive Company Profiles on the market, powered by GlobalData. Save hours of research. Gain competitive edge.
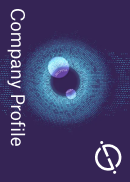
Thank you!
Your download email will arrive shortly
Not ready to buy yet? Download a free sample
We are confident about the unique quality of our Company Profiles. However, we want you to make the most beneficial decision for your business, so we offer a free sample that you can download by submitting the below form
By GlobalDataWe are also interested in developing an alternative means of transmitting data from bottom hole to surface without cables, for example, using the pipes or the formation itself as a conductive medium.
Today, the limitation of conventional MWD tools is the quantity of data that can be transmitted to surface.
If we are able to develop a technology for transmitting a lot of data in real time that would be a massive advantage to us, but the work is still at a very early stage.
Have we also seen focus turn to casing design?
We have developed a proprietary casing design that allows for the reduction of borehole size or casing clearance without damaging the diameter of production casing and tubing. This system enables us to access deeper targets and new reserves while maintaining the same hole size and reach shallower targets with reduced casing sizes. This technology, like managed pressure drilling, has been developed in-house with the support of external partners for specific sub-systems.
Can you expand on how those external providers are chosen?
There is no clear rule. We’ve been working with oil companies, both major and niche technology providers, within and outside the industry. In recent times we have seen a concerted effort in terms of quantifying the return from R&D, including intellectual property.
ENI is a big company, but not a super major. Depending on the application, we have to rely on service providers because those are the guys who will bring us the technology.
We’ll try and drive the evolution of technologies – for example, ENI were the people who supported Baker in the development of the Autotrack rotary closed-loop system back in the late-1990s – and we also try and identify smaller niche service providers.
When you’re talking overall drilling requirements, however, big things need to be built in big factories. Industrialisation is always an important consideration.
Describe the amount of internal collaboration required to make the R&D function work.
We run need-search exercises on a yearly basis and will conduct interviews with all business units, collect aggregate needs and start working our R&D programmes based on that.
The R&D central authority grants funds for the different technology areas, including drilling and completion. R&D functions in Milan drive the technology applications towards ENI business units worldwide. Usually budgets, risks and rewards of new technology applications are shared among central R&D functions and business units.
Is intelligent completion still a major area of R&D investment?
ENI pioneered intelligent completions in the late 1990s, including the world’s first subsea application. We’ve been through some ups and downs, but the practise is well established nowadays within the company’s DNA and a technology of choice for a number of operating scenarios – one recent example would be the Abo field off the coast of Nigeria.
The technology is certainly mature enough for conventional environments, say below 150°C. The problem of high temperature remains and we’re still not there yet.
I cannot confidently run an intelligent completion in an environment that is 200°C and, equally, can’t see a time on the immediate horizon when that will be possible.
What are the major operational drivers for your department?
ENI is actively seeking for solutions to minimise deepwater risks and costs, from blue sky solutions to readily available ones – for example, a technology that is becoming common practise is the dual-casing run. Given the size of the pie, real efforts are being undertaken to identify further areas of improvement, including the potential of dual-activity rigs.
Safety, environmental impact and sustainability are among the key elements driving ENI’s technology selection process. The projects mentioned earlier are an example in this regard: the managed pressure drilling system certainly increases safety while the smaller diameter casing profile benefits the environment by reducing the amount of drilling cuttings. These returns are duly captured from R&D.