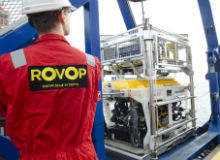
Moray Melhuish is commercial director at ROVOP, a niche company that provides rapid-response remotely operated vehicles to the subsea oil and gas and offshore wind farm industries. ROVOP was singled out for a business growth award at the 2012 Scottish Green Energy Awards. Previously, Melhuish was sales manager, i-Tech, at Subsea 7, which specialises in seabed-to-surface engineering, construction and services.
Julian Turner: Please describe the evolution of ROVOP and the remotely operated vehicle (ROV) systems it provides to offshore oil and gas and wind farm operators.
Moray Melhuish: ROVOP has carved out a niche for itself by focusing solely on the provision of ROV services, being independent of all vessel owners and charterers (and therefore not competing with our customers), hand-picking and employing the most experienced ROV professionals and offering customers the latest and best ROV technology available to the market.
The company has evolved from Seaeye Cougar XT systems, selected for its high thrust / small deck footprint combination, to providing larger Panther XT Plus electric light work-class vehicles that provide exceptional high current performance and work-class manipulators – and now Schilling HD work-class vehicles.
The 150HP Schilling HD systems are, in our opinion, the most capable and advanced ROV systems available to the market today, which is why we have invested so significantly in them.
How well do you really know your competitors?
Access the most comprehensive Company Profiles on the market, powered by GlobalData. Save hours of research. Gain competitive edge.
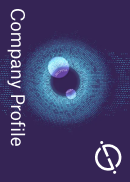
Thank you!
Your download email will arrive shortly
Not ready to buy yet? Download a free sample
We are confident about the unique quality of our Company Profiles. However, we want you to make the most beneficial decision for your business, so we offer a free sample that you can download by submitting the below form
By GlobalDataJT: Is ROVOP investing in new ROV technology to complement its existing product range?
MM: Ongoing investment in our ROV fleet is important to ensure that our vehicles continue to be the most capable in the market. In November 2012, we announced a planned investment of £15m in Schilling HD work-class ROVs, in addition to significant investment in Seaeye Cougar and Panther XT Plus electric light-work class vehicles. Each vehicle type is chosen for its distinct performance in the conditions we typically work in; for example, a low vehicle profile combined with high thrust is important for operation in high currents.
Maintainability is also crucial. The Schilling HD vehicle is unique in that it is designed around a 60-minute repair philosophy; while repairs to other work-class vehicles may take 12 hours or more to complete, the repair to the HD should take just one hour. With high rig and vessel day rates at stake, this design feature can end up saving days of vessel time over the course of a project, resulting in considerable cost savings for our customers.
Financial investment alone is not a guarantee of success, however. At ROVOP, investment is combined with a ruthless selection policy targeted at employing the most experienced ROV personnel in the industry. To date, the company has created more than 40 highly-specialised, export-focused jobs; before the current investment programme is complete, we estimate that we will have created a further 40.
ROVOP is also investing in the next generation of ROV personnel. To enable us to train pilot technicians onshore, we have invested more than £250,000 in a Schilling HD simulator – which we will receive later in 2013 – while the first HD system to join the fleet has been mobilised to an offshore wind project in Germany.
JT: What are the main benefits that ROV technology offers offshore operators compared with more traditional subsea techniques?
MM: The main benefit of any ROV is that they avoid having people in the water during subsea operations. While we are careful to avoid any damage, the ROV system is a machine which can be repaired, and its use instead of divers reduces the risk to human life.
In addition, ROVs are capable of operating in depths and at currents beyond the capability of divers. Our work-class systems are typically rated to 3,000m, more than ten times the depth suitable for diving, while our Panther XT Plus systems are capable of travelling at four knots.
In terms of cost savings, a ROV system can be mobilised for far less than a dive spread and operated from a greater range of vessels.
JT: Offshore oil and gas operators are exploring increasingly inhospitable environments. What challenges do these environments pose to ROV specialists like ROVOP and how is the company responding?
MM: The main challenge to ROV contractors is to ensure that their veteran systems continue to be reliable, and are capable of deploying the latest generation of hydraulic tooling and advanced survey equipment.
ROV systems, like any technology product, are evolving at a fast pace. In this regard, ROVOP has a considerable advantage over larger subsea contractors, in that its fleet of vehicles consists of only modern vehicles with the latest system diagnostics built in.
The oldest system we own was built in 2012, so every product we have is designed to accommodate the increasingly inhospitable environments faced by offshore operators.
JT: What are the differences between offshore wind farm and oil and gas projects and does ROVOP have to adapt its technology to deal with the differing demands of each industry?
MM: ROVOP selects its technology to ensure that it can operate equally well in the shallow waters of an offshore wind farm, and in the deepest oil and gas projects. Arguably, the high currents, poor visibility and wave impact encountered in the first few metres of water in offshore wind projects are more difficult to operate in than the deep, clear waters that characterise our oil and gas work.
JT: How is the offshore ROV industry regulated and what are the major legislative changes affecting ROVOP in terms of safety and technical standardisation?
MM: ROVOP is a member of the International Marine Contractors Association (IMCA), which provides good practice guidelines around which we work.
For example this includes the number of pilot technicians and supervisors deployed with each system per shift, as well as the experience and competence each team member must have before they can progress to the next level in their careers.
The IMCA is due to issue new guidance documents on inspection, installation, rigging and lifting, among others, and as always ROVOP will engage with the organisation to ensure that best practice is adopted when these new guidelines are introduced.
JT: Can you pick out a recent offshore project that was a particularly successful showcase for ROVOP and its technology?
MM: In one instance, a customer awarded a contract to another ROV contractor that provided less capable equipment and less experienced personnel. The impact of this cost-focused approach was high levels of down time, project delays and cost overruns.
ROVOP was consulted, and mobilised new equipment operated by highly experienced personnel. Since then, the project has been a success and this is reflected in the high level of repeat business that the customer brings to us.
JT: How do you see ROV technology evolving and does ROVOP have any innovations in the pipeline?
MM: As we grow, we see increasing demand for our services and we will continue to invest in the latest generation of ROV systems.
The £250,000 simulator investment will enable us to develop the skills of our offshore personnel at all levels and also enable us to provide customers with simulations of their offshore projects before they take place. This will not only identify risks and opportunities for improvement with proposed methodologies; it will also result in cost savings by identifying issues before any equipment is taken offshore.
Related content
Subsea repair: refining the process
Often taking place at great depths and presenting serious risks, subsea repair work on offshore pipelines can be a challenging business.
Ormen Lange: the beginning of entirely subsea oil and gas production?
As Shell continues to develop its subsea compressor technology for its Ormen Lange deepwater project in the Norwegian Sea, the vision of an entirely rig-less project could soon become reality.