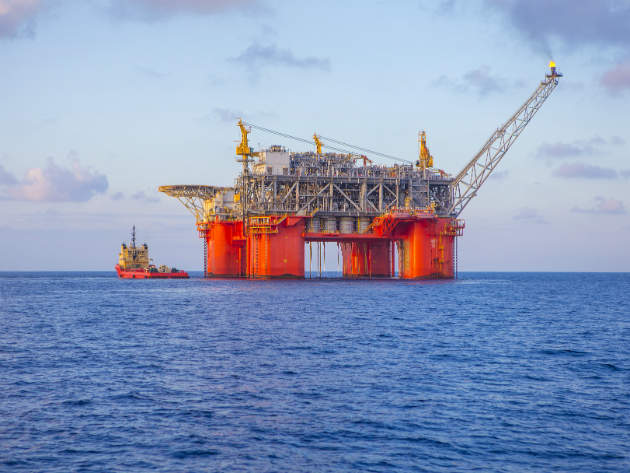
In November GE and BP announced work had begun on a new pilot project to trial GE’s Plant Operations Advisor (POA) technology on BP’s Atlantis rig in deep water offshore the Gulf of Mexico. It is the first time GE’s asset management technology has been deployed in the oil and gas sector.
The pilot project, which was first announced last year, is firmly underway, with data being collected and managed for use by BP’s operations personnel to reduce rig downtime and provide analytical insights.
This phase of the project will end in mid-2017, after which the technology will be deployed throughout BP’s other deepwater assets, resulting in the biggest roll-out of GE’s Predix technology, a cloud platform for the Industrial Internet, on which the POA technology is based.
Here, we find out more about the technology and the pilot project from
Binu Mathew, global head of development and product management at GE Oil & Gas Digital.
How well do you really know your competitors?
Access the most comprehensive Company Profiles on the market, powered by GlobalData. Save hours of research. Gain competitive edge.
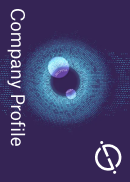
Thank you!
Your download email will arrive shortly
Not ready to buy yet? Download a free sample
We are confident about the unique quality of our Company Profiles. However, we want you to make the most beneficial decision for your business, so we offer a free sample that you can download by submitting the below form
By GlobalDataHeidi Vella: Can you tell me a bit more about GE’s pilot project with BP?
Binu Mathew: The project is being built on top of GE’s Predix platform and ties into our asset performance management solution.
The POA technology connects up the machine data around the rigs, pulls it all into a central location and provides visibility and analytics to BP, giving them much more visibility into what is going on compared to before. This helps them tremendously in terms of dealing with non-productive time.
That sounds simple but it is extraordinarily difficult to do if you have servers in individual locations or in individual plants.
This technology brings all of it together. Then we start dealing with a lot of difficult technology issues which we have solved with Predix – such as the amount of data coming in. When you are dealing with lots of machines and a large number of data variables across those machines, being able to deal with that scale is something we have solved with Predix.
HV: How long does it take to deploy the technology?
BM: One of the big benefits is that Predix is a cloud platform – so that means it is running on GE’s cloud infrastructure in data centres around the world. So, there is a lot of this stuff up-and-running that does not need to be deployed, which cuts down deployment time considerably.
The bulk of the work in terms of deployment is connecting up the assets. One of the things that is interesting about the oil and gas industry is that, actually, there is a lot of data that is being collected, there are control systems on the plants, there are historians, there is actually a lot of sensor equipment.
Going forward we will make it easier to collect additional machines as well. Even today there is a lot of data that is simply not being accessed. One of the estimates I have seen is that around 5% of the data being collected is not actually being used.
So, in summary, we connect all this data up, send it across and run it in the cloud. For each rig this takes about a month.
HV: How do you manage safety in regards to the cloud?
BM: One of the things I think is a common misconception is data might be more unsafe on the cloud. However, you need to remember a lot of these machines are connected up anyway, and when you have a certified cloud provider like GE putting in all the infrastructure around security, certifications and analysis, the security teams are constantly monitoring the system, we believe a cloud system is actually far more secure than a traditional system.
For a traditional system you are often dealing with different individual silos and the individuals who are in each plant or location are not necessarily security experts, they are typically doing this as a side job.
This isn’t just theoretical. This is what we have seen in many cases when we are working with plants; they are simply open and if people know how to access them it is very easy to disrupt.
HV: Has the project faced any challenges yet?
BM: We work in an agile format, where teams go in in a two-week cycle and we go through the features that are relevant to BP. We get very quick feedback and are therefore able to put them back into the project very, very quickly, so that helps us tremendously.
From a GE perspective, we are building this up as a central project for the industry as a whole so the feedback we get as part of the exercise is extremely valuable.
HV: The industry is generally considered to be a slow adopter of new technology – do you see this changing?
BM: We do. We have done surveys of the customer base and if you look at the reactions you get today, it is changing even when you talk to people quarter on quarter. I think it is rapidly flipping towards acceptance of the importance of digital solutions. I think the downturn in the overall industry is also driving that focus of down production time and optimisation of production. These are all very relevant things in an era where the oil price is in the $50 a barrel range.
I think you are going to see this in two sets of spending. As new assets are put in place then I think customers want to have this kind of technology now as part of building up new plants and new capabilities. But for existing assets as well customers are looking to get much more than they did before. So even if you don’t have capital spending in that sense, there is a drive now to spend more on these sets of solutions so that they can get more leverage out of existing capital assets.
HV: How much money can the technology save a company?
BM: If you have a plant that is operating, say, at 91% uptime, our goal would be to up that by a couple of percentage points. If you can make reliable overall uptime improvements of two percentage points that is a considerable benefit to the customer.
HV: Is there a minimum of digitisation required on a rig to deploy the technology?
BM: It all depends on what the assets are that impact uptime. That would depend on a case-by-case basis. If you found that most of your issues are to do with critical rotating equipment or critical pumps, typically a lot of those are sensor-enabled, but that is an evaluation the customer needs do. Do you have data available for these assets? If so, then the focus moves to how we can connect all this up and use the data. If not, then GE also has technology to help sensor-enable a number of assets.
HV: Going forward, could this technology reduce the number of staff an operator needs?
BM: Maybe in the longer term that might come into play. For now I think the main benefit for customers is increased uptime and production optimisation. That is better use of the personnel they have in place. So, a person trying to figure out exactly where the problem exists can now look at one of these systems and get a far better insight into where the issue is and get it fixed much more quickly than before.