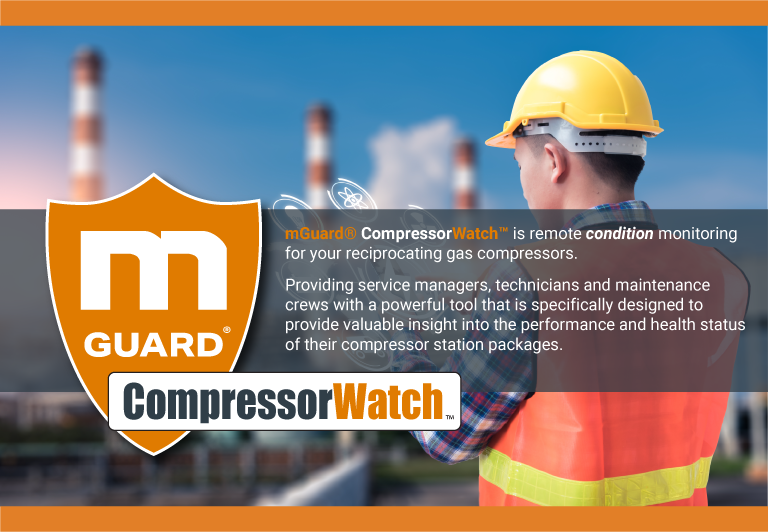
Monico Monitoring, Inc. is an industrial communications company with over 18 years of experience, providing solutions for the capture, translation, transmission, visualization and analysis of industrial data from heavy machines and equipment. Monico has a suite of industrial gateways specifically designed for the capture of data from machines and equipment used in oil and gas, mining, marine and electrical power generation. It collects this data from machines/equipment by connecting to the industrial networks and reading protocols (i.e., machine data) such as J1939, Cat Data Link, ModBus, CANopen and more.
Monico specializes in Caterpillar engines; being one of the only companies other than Caterpillar® that streams real-time engine data using the proprietary Cat® Data Link protocol. Monico also works with many other OEMs and have captured streaming data from Liebherr, John Deere, Cummins, and more.
A highly ruggedized industrial gateway
About six years ago Monico began noticing that although they could help their customers get data from their machines/equipment and store it in databases or push the data into screens (i.e., HMIs); the data wasn’t being leveraged to its full capability. So, they set off on a journey to create a highly ruggedized industrial gateway to meet the demands of harsh environments and provide the processing power to capture real-time data and process edge analytics.
Monico began working to develop and provide a solution to help their customers get the most benefit from the data that machines were generating. In oil and gas, Monico has been working globally with large companies for more than 12 years in drilling and gas compression; helping integrate industrial data into enterprise solutions. However, Monico wanted to take it a step further and employed subject matter expertise with experience in data analytics for engines and compressor station packages. Over the last four years Monico’s subject matter expert, David Krenek, has been developing automated analytics that run 24/7/365, monitoring gas compression stations and helping to predict potential failure modes that may result in catastrophic shutdown events or reduced performance.
Monico is proud to announce the culmination of it all and offer our latest solution for the oil and gas industry; specifically for Gas Compressor Station Package Monitoring; referred to as mGuard® CompressorWatch™.
About the mGuard® CompressorWatch™
mGuard® CompressorWatch™ is remote condition monitoring for your reciprocating gas compressors (i.e., drivers and ancillary equipment). Here are its benefits:
- mGuard® CompressorWatch™ provides a tool for reliability managers, service managers and technicians to have improved insight into how the station; the engine and the compressor are performing and what the health status is. It helps to improve optimization, uptime and reliability
- CompressorWatch™ is built on the trusted MonicoLive™ platform hosted in the Microsoft® Azure cloud. Our automated analysis and notification are completely set-up and managed by Monico’s Subject Matter Experts and specifically designed to save you money through improved asset reliability, reduced unscheduled shutdowns and improved preventative maintenance planning.
- mGuard® CompressorWatch™ collects real-time streaming data from the compression station assets; including the engine ECM, Package Controller and other external sensors.
- No expensive sensors add-on packages are required, this solution works with existing sensors/networks
Monico has developed real-time analytics that run unattended 24/7/365 as data streams in from the asset(s)
- There is no need to download data records, CAN logs or other information to run analytics manually in spreadsheets or other tools
- No need for a human to be actively involved in analyzing data (it works while you sleep)
Automated notifications and analysis include, but are not limited to:
- Emissions
- Engine & Compressor Components
- Engine & Compressor Sensors
- Engine Performance
- Compressor Valve Failures
- Equipment KPIs (e.g., Reliability)
- Jacket Water Cooling Systems
- Auxiliary Cooling Systems
- Air Intake Systems
- Ignition Systems
- Lubrication Systems
- Exhaust Systems
- Air/Fuel Ratio Systems
How does it work?
As data stream in from a compressor station package, mGuard CompressorWatch runs analytics on the data in real-time and if conditions are met that are indicative a potential failure mode they are captured, logged, and can be reviewed with time stamps in a powerful user dashboard environment.
The Data Visualization or Dashboard environment provides full detailed charts, graphs, tables and more with data from the asset and can be reviewed in manner similar to a DVR; moving forward and backwards through time. This provides a powerful tool to service/maintenance professionals in diagnosing what may be happening with the station and how to remedy it.
However, the real power comes from the Advanced Notifications feature of CompressorWatch; which alerts maintenance, service personal of an event via email with a link embedded to the actual occurrence in MonicoLive with recommended and suggested actions to be taken.
Now, you don’t have to wait for your station to have problems you can know ahead of time that problems are developing and proactively address it.
Further details:
For more information on mGuard® CompressorWatch™ we invite you to read our highly detailed FAQ – Informational Brochure.