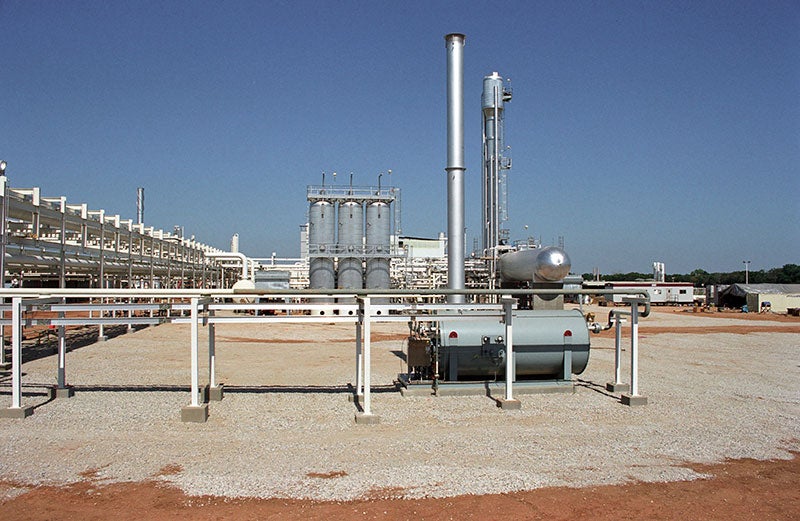
Water bath heaters (WBH) provide a well-established method for heating oil and gas and are known within the industry for their successful application across a range of operations.
Typically used on offshore platforms, refineries and gas suppliers, they mitigate the need for a high pressure vessel and form a critical component on oil and gas networks.
WBHs work by submersing a process coil into a heated bath solution, such as water-glycol mix, molten salt, or oil. This indirectly heats the oils or gas inside to 130 to 150 degrees Fahrenheit (though higher temperatures can be achieved with an oil or molten salt bath solution) as it flows through the heater’s tube bundles and creates energy.
It is important that the tube bundles are not directly heated to reduce the risk of unwanted condensates. Should they come into contact with high temperature gases, moisture in the gas could cause the tube bundles to condense and subsequently produce a corrosive liquid.
Additionally, heating gas before pressure is reduced helps to avoid ice crystals and hydrates – which can cause major damage to equipment – from forming in lines when the pressure is reduced. If preheating is not applied within the process, equipment may also experience embrittlement of piping and fittings, and blockage of filters and regulator/valve seats.
There are benefits for crude oil, too, helping to reduce its viscosity to form an easily-pumped liquid.
Uses of water bath heaters
WBHs utilise a safe, simple process. In the event of coil failure, this indirect heating method helps to reduce the risk of explosion. They are typically used for: heating transfer fluids; regeneration gas heating, vaporising and superheating LPG and LNG; and heating sensitive gases and fluids, such as crude oil.
Typically, a WBH will consist of a control system, insulated shell, removable fire tube and process coil, stack burner and gas train. Aquatec, a series of water bath heaters from leading manufacturer of heaters and tanks Heatec, feature an externally insulated heater shell, burner, furnace tube, serpentine tube bundles, an expansion chamber, and an aluminium skin.
They are skid-mounted, factory-wired and piped and the furnace tube may be either a single U-tube or multiple U-tubes, depending on the Btu required.
The Aquatec burner fires directly into a U-tube inside the heater shell and is filled with water that surrounds both the serpentine and U-tubes. The water transfers heat from the U-tube to the serpentine tubes, heating them indirectly without exposure to high temperature gases.
Normally gas-fired, outputs of standard Aquatec models range from 0.65 million to 9 million Btu/hour but they can be customised to suit site needs. Heatec’s WBH series can also be configured for use in hazardous zones or isolated areas where electrical power is not available.
Heatec design, manufacture and service heating and storage systems around the world. The company’s products are used throughout the hot mix asphalt industry as well as chemical plants, oil-and-gas refineries, on off shore platforms, barges, and many others.