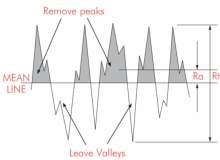
To extend the fatigue life of components by reducing friction and lubricant temperature, the process of C.A.S.E.™ isotropic superfinishing is recommended for all components where both sliding and rolling of metal occurs between two load-bearing flat surfaces. Suitable applications include transmission gears and shafts of virtually any size.
This technique is normally preceded by controlled shot peening followed by superfinishing. The process involves removing the surface peaks but retaining the surface valleys for lubrication retention and heat transfer. Oxalic acid softens the surface peaks, making them more susceptible to micro-honing. Non-abrasive finishing stones progressively smooth the surface, which produces a bright mirror-like surface finish. The chemical process does not harm the beneficial residual compressive layer induced by shot peening or attack the grain structure of the material. It can be used to round off sharp edges for ease of handling and assembly.
Pitting fatigue is common in gears and the C.A.S.E.™ superfinishing process has been effective in improving resistance to macro-pitting, as well as micro-pitting. The smooth surface finish allows contact loading to be distributed over a greater surface area, which results in reduced contract stress and extended pitting fatigue life. Experience has shown that using gears that have been superfinished results in up to five times increase in fatigue life.
Typical applications include:
- Transmission parts
- Bearings
- Cams and followers
- Journals
- Seal faces
- Any situation involving metal to metal contact