Listed below are the key oil and gas trends impacting the predictive maintenance theme, as identified by GlobalData.
Unplanned shutdowns due to equipment failure can incur immense cost penalties for oil and gas operators. Older oil and gas facilities have been more at risk of unplanned downtime. These also may contribute towards excess greenhouse emissions. Using predictive maintenance techniques, the performance of older equipment can be improved.
How well do you really know your competitors?
Access the most comprehensive Company Profiles on the market, powered by GlobalData. Save hours of research. Gain competitive edge.
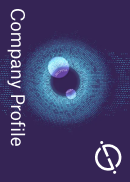
Thank you!
Your download email will arrive shortly
Not ready to buy yet? Download a free sample
We are confident about the unique quality of our Company Profiles. However, we want you to make the most beneficial decision for your business, so we offer a free sample that you can download by submitting the below form
By GlobalDataCost pressure
The oil and gas industry are susceptible to economic downturns, which can cause huge operating losses for stakeholders, indefinite delays in planned projects, and job losses. In such situations, it is key to efficiently manage operating expenses to have a higher chance of survival.
Periodic maintenance conducted in the oil and gas industry is aimed at increasing asset productivity and profitability. The exercise can prove costly and cannot always ensure the prevention of unanticipated equipment malfunctions. In contrast, predictive maintenance can assist in the early discovery of equipment failures, thereby reducing unnecessary downtime. It can also reduce the requirement for scheduled maintenance tasks to be performed regularly, cutting the associated operational costs.
Recent volatility in oil prices has motivated the industry to reconsider its maintenance strategies and opt for implementing innovative predictive maintenance technology across a variety of assets, to boost operational efficiency and reduce downtime.
See Also:
Streamlining maintenance activities
Predictive maintenance technologies assist in taking a proactive approach at asset inspection by recognising the equipment that requires maintenance or service, precisely diagnosing the nature of the problem, and recommending a potential remedy. It allows maintenance professionals to plan and execute repairs selectively, reducing the overall effort required to complete maintenance procedures. Predictive maintenance also aids in the efficient management of machinery necessities, like lubricants, components, and other add-ons.
Ageing infrastructure
Much of the infrastructure in the oil and gas industry was built several decades ago, using designs, materials, and technology that were available at the time. In several cases, the planned life expectancy envisioned during the design process has also been exceeded by these aging assets. The infrastructure is bound to malfunction at some point in the future. Therefore, it must be inspected and monitored regularly.
Sensors installed on ageing equipment would also help to prevent accidents and reduce risks to the employees and the environment. However, implementing predictive maintenance in older equipment can be a difficult task to accomplish. Most new equipment, on the other hand, comes preinstalled with sensors for monitoring telemetry and other key parameters that might be easily fed into a predictive analytics system to identify the condition of the equipment.
Shortage of skilled workforce
Predictive maintenance technologies have been around for a long time, and oil and gas businesses have used them in a variety of situations. However, in recent years, the industry has seen a surge in the adoption of predictive maintenance to ensure that all field equipment is operating at peak efficiency.
However, with the growing demand for these technologies around the world, the availability of qualified personnel required for interpreting sensor data may prove insufficient. Evaluating data from vibration sensors, thermographic equipment, and other devices necessitates extensive domain knowledge and skill, as well as years of training and field experience.
Covid-19
After the Covid-19 pandemic, ensuring the health and safety of workforces in the oil and gas industry has gained renewed rigor. Predictive maintenance technologies help in averting major mishaps as well as operational hiccups, which leads to a safer environment for the workforce.
Predictive maintenance employs the internet of things (IoT) and other technologies to monitor assets, especially those that are remotely located. It can also navigate the negative impacts of Covid-19 supply chain disruptions by optimising the maintenance works with the help of artificial intelligence (AI).
The Covid-19 shock, and its economic fallout are likely to accelerate the digitalisation activities in oil and gas operations, increasing industry-wide adoption of predictive maintenance technologies.
This is an edited extract from the Predictive Maintenance in Oil and Gas Industry – Thematic Research report produced by GlobalData Thematic Research.