Listed below are the key technology trends impacting the predictive maintenance theme, as identified by GlobalData.
The emergence and rapid growth across innovative technologies such as the Internet of Things (IoT), artificial intelligence (AI), augmented and virtual reality (AR/VR), big data, cloud computing, and others have shaped the maintenance strategies in the oil and gas industry. Remote and centralised observation platforms have improved decision making. The base measurement technologies for predictive maintenance have also improved, as a vast amount of data and analytical capabilities are available, owing to the boom in digital transformation projects across the industry.
How well do you really know your competitors?
Access the most comprehensive Company Profiles on the market, powered by GlobalData. Save hours of research. Gain competitive edge.
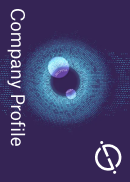
Thank you!
Your download email will arrive shortly
Not ready to buy yet? Download a free sample
We are confident about the unique quality of our Company Profiles. However, we want you to make the most beneficial decision for your business, so we offer a free sample that you can download by submitting the below form
By GlobalDataDigitisation
The oil and gas industry has experienced significant advancements in digital technologies during the previous decade. AI and machine learning (ML) are becoming increasingly important in all aspects of a business. The oil and gas business is increasingly being transformed by digitalisation, which is allowing for remote monitoring and control of operations, as well as data-driven decision making.
The deployment of predictive maintenance is aided by the growing reliance on remote asset monitoring from centralised sites. It enables businesses to check equipment status in real-time, analyse equipment servicing or repair requirements, and dispatch maintenance people as needed to complete maintenance tasks.
Big oil companies have long pursued the digitisation trend and are therefore ahead of the curve in implementing predictive maintenance strategies. Prominent NOCs are also actively increasing their digital footprint to capitalise on their existing resources.
See Also:
Digital twin
Digital twin involves virtual simulation of a physical operation involving various equipment. It is used for monitoring the physical operation it is replicating in the virtual form. Companies can gauge the results of real-world deployments and make informed decisions based on these findings.
The adoption of the digital twin is best suited for performing predictive maintenance on oilfield equipment, as the system would be able to accurately assess the equipment’s health and performance, and provide feedback for corrective actions, whenever necessary.
IoT
IoT has been a great way to collect accurate and readily accessible data from daily oil and gas operations. Several companies are using IoT technology to enhance their monitoring capabilities as the uninterrupted operation of their critical equipment is essential for profitability. Declining sensor costs have also boosted the oil and gas industry’s adoption of IoT solutions.
Asset management remains the key aspect for IoT deployment, and the major concern for companies is the high cost of maintenance of ageing critical infrastructure. IoT is providing the bulk of the necessary data for companies to carry out maintenance, repair, and overhaul of critical infrastructure. This leads to increased reliability and improves an asset’s lifespan.
Combining multiple technologies
Predictive maintenance technologies, such as vibration monitoring, thermography, lubricant oil analysis, ultrasonic and acoustic emission testing, and visual inspection are all adept at predicting equipment failure and even identifying the probable source of deterioration. Using a combination of two or three of these technologies can considerably improve the accuracy of predictive failures.
Moreover, when multiple technologies are used in combination, they can be used to correctly pinpoint the exact cause of the impending failure and guide companies in taking further action to avoid a breakdown.
Data analytics
Data analytics entails the ability to analyse large volumes of sensor data, compare it with historical records, and correlate patterns for determining the current health of equipment. The development of newer data analytics models has enhanced the accuracy of flaw detection. Real-time analysis has improved the speed at which faults are being identified, resulting in early warnings for the maintenance crew.
AR and VR
The wearable technology consists of a sensor-equipped device, such as a watch, helmet, or glasses, which can be worn by a person while performing tasks. Combined with AR/VR technologies, it can help field technicians to undertake maintenance tasks. Schlumberger uses AR-enabled smart glasses to enable employees to operate and maintain mobile fracking equipment.
Companies are customising portable devices, such as smartphones, tablets, smart glasses, and HMDs, with AR technology to support field activities. BP, Chevron, and Baker Hughes have started to use AR for remote technical assistance. VR has been used to train technicians in inspection and training activities in the oil and gas industry. Effective use of wearables and AR/VR can significantly improve predictive maintenance tasks.
This is an edited extract from the Predictive Maintenance in Oil and Gas Industry – Thematic Research report produced by GlobalData Thematic Research.
Related Company Profiles
Iot Holdings Plc
BP Plc
Schlumberger Ltd
Baker Hughes Co
Chevron Corp