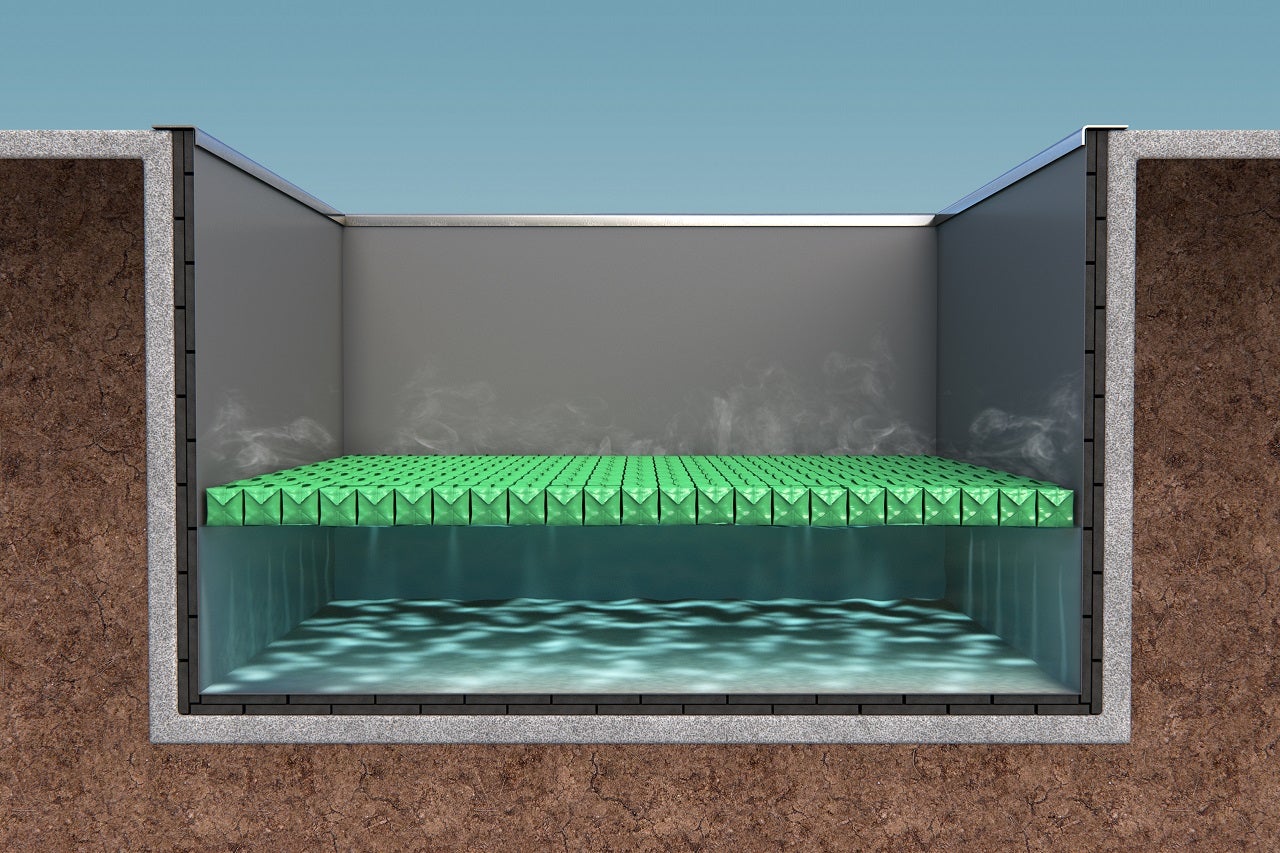
New LNG facilities are being built to support the increasing global demand for energy, prompting a focus on the safety of these facilities. As companies look to shrink facility footprints, maintain safety, and operate in new ways – or in more populated areas – now may be the time to consider a multi-pronged approach to LNG pool fire suppression and cryogenic spill protection.
Although every site must have a spill containment area, taking a systematic approach to managing the risks generated by LNG may provide a cost-effective way to reduce thermal radiation and flame height while shrinking exclusion zones and maintaining facility and employee safety. Looking holistically at steps to manage fire risks includes examining ways to cap or cover spilt LNG, reducing and extinguishing flames, and planning to limit the amount of vaporised LNG available to burn by using a combination of tools such as the FOAMGLAS® PFS™ pool fire suppression system and FOAMGLAS® Cryo Spill™ Protection System. Using both technologies together to cover and line the LNG containment pit can deliver improved and cost-effective passive fire suppression.
The FOAMGLAS® PFS™ pool fire suppression system
The PFS™ system is designed to provide a cost-effective, reliable, long-lasting, and low-maintenance passive option to limit thermal radiation, flame height, fire size, and view in contained LNG fires. The second-generation fire suppressant also supplies immediate mitigation of thermal flux. Unlike firefighting foams, which require frequent replacement, it was designed to remain in place indefinitely, providing an automatic response and reducing the potential for deployment delays. The system also potentially allows new facilities to reduce exclusion zones, shrink distances between operational zones, or trim the protective material used on piping.
The FOAMGLAS® Cryo Spill system
The FOAMGLAS® Cryo Spill™ system is straightforward to install and can be used as additional passive security and cost-effective measure to reduce the amount of flammable LNG vapour in the event of a spill. Lining containment pits with the insulation in conjunction with using the FOAMGLAS® PFS™ system provides additional hurdles for pool fires.
In addition to reducing the production of flammable vapour during a spill, there can be a financial advantage to insulating containment areas with the FOAMGLAS® Cryo Spill™ system. Both steel and concrete can be sensitive to rapid changes in temperature, such as exposure to cryogenic liquids at or below -160˚C (-256˚F). A sudden cold shock may induce structural changes that reduce the load-bearing capacity of either material.
Suddenly exposing concrete to subfreezing temperatures can damage the material, as it may contract or expand when water inside the concrete freezes – both types of movement can generate microfractures. Similarly, rapidly exposing carbon steel to temperatures below -29˚C (-20˚F) can induce the metal to become brittle and fracture, although some types of low-temperature stainless steel can tolerate temperatures down to -48˚C (-54˚F).
If concrete pit walls are not insulated, cryogenic steel may need to be used as reinforcing rebar in LNG containment pits. However, rebar made from cryogenic steel is far more expensive than traditional rebar. By insulating concrete walls – keeping them from sinking to cryogenic temperatures – containment areas may be able to save money and use traditional rebar.
Benefits from a systematic approach to fire suppression
Using the FOAMGLAS® PFS™ system as a passive prevention can improve facility and employee safety, reduce the vaporisation of LNG, and limit thermal radiation and flame height if the LNG pool ignites.
Combining the use of the FOAMGLAS® PFS™ system with a spill pit lined with the FOAMGLAS® Cryo Spill™ system can further reduce the amount of LNG able to boil-off during a spill and limit the flammable vapour produced.
Additionally, lining spill pits with FOAMGLAS® cellular glass insulation may provide cost savings, as the insulating effect of the material can help protect concrete walls and allow for the use of traditional rebar in place of more expensive alternatives like cryogenic steel reinforcing rebar.