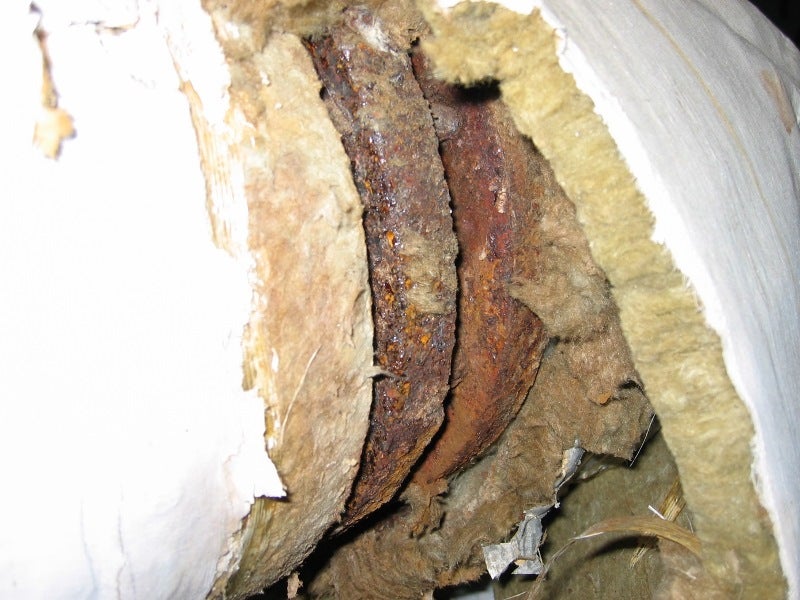
The general consensus within the offshore sector is that corrosion resistance is an important safety consideration.
Corrosion-related failures at processing facilities are a major source of risk to offshore oil and gas installations, and that’s why it’s so important to do whatever is possible to prevent any possibilities of corrosion formation.
Moisture ingress into conventional insulation materials usually results in accelerated corrosion of the underlying steel surface, which can lead to the structural failure of insulated items such as pipes and vessels.
If such equipment is operating under high pressure, then the potential of a catastrophic failure poses a real threat to the safety of facility, workers not to mention the environment.
Formation of Corrosion Under Insulation (CUI)
The main issues that promote corrosion under insulation are the deterioration of joints, joint sealants, inadequate maintenance of metallic cladding and the use of fibrous insulation materials.
With fibrous insulation materials, the insulation can often contain significant moisture before it is even applied, even with ‘water repellent’ fibres.
The insulation will have absorbed humidity from the atmosphere and could even have been exposed to marine rain or spray containing salt.
Simply applying these materials and sealing them in will introduce moisture around the pipe.
External corrosion is caused by the ingress of chloride containing water from the environment, as a result of sea water deluge and practices such as washing decks with seawater, which is absorbed and retained by the fibrous insulation materials.
Inadequate coating systems applied to pipe work and vessels has been a major contributing factor to CUI.
Preventing Corrosion Under Insulation
The simple conclusion is that you need to keep water out of insulation systems in order to prevent CUI.
One of the most effective ways of doing so is through the introduction of closed cell insulation materials together with an applied flexible coating to provide a seamless weather proof membrane, which will prevent any possible water ingress and retention.
Cellular glass is a 100% closed cell insulation material that is used from -268 degrees C to +430 degrees C, and so is widely used for both cryogenic and hot systems.
Its uniquely 100% closed cell nature is the reason why, over a decade ago, Statoil and the Norsok standards started promoting cellular glass insulation as a key part of their CUI prevention strategy.
Another critical point is the ability to fully seal the insulation system; cellular glass can be joint-sealed through the entire thickness of the insulation, so giving a full-thickness barrier against water ingress rather than relying on a thin surface cladding joint.
FOAMGLAS® Terostat PC® FRi
The FOAMGLAS Terostat system is a combined system of FOAMGLAS closed cell cellular glass insulation with Terostat PC FRi, a one component silicone-based sealant, coating and adhesive, which cures by reaction with moisture to a soft elastic monolithic product.
The product is free of solvents, isocyanates and PVC, and combined with its excellent flame retardant properties (Class O as per BS476) this makes it the preeminent anti-CUI insulation system for offshore applications.
Many offshore and onshore installations have adopted this way of working and started to see the benefits in CUI prevention and increased long-term thermal efficiency.
Pre-coating cellular glass in flexible coatings such as the FOAMGLAS Terostat system have simplified this process by giving quick installation with easier and more-effective sealing to maximize CUI protection.
A 100% closed-cell insulation, plus a pre-applied flexible coating with fully sealed joints, will provide an exceptional insulation system for CUI prevention and longevity.