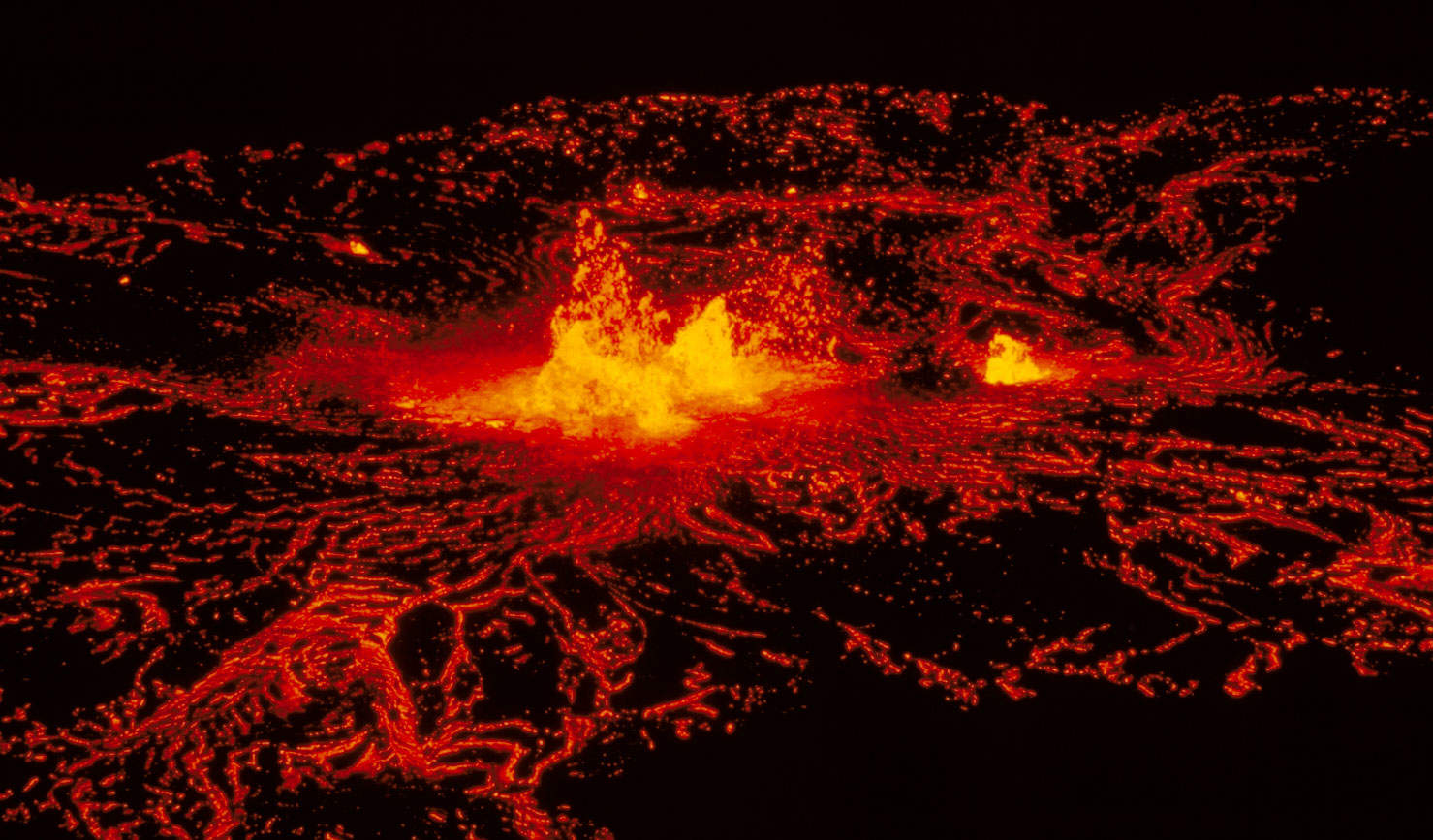
Even long after an oil well has given up the ghost of productivity, it needs to remain sealed to prevent the leakage of hydrocarbons.
As part of the plug and abandonment (P&A) phase, most wells are dealt with by inserting a plug comprised of cast iron and rubber inside the steel casing, before being sealed on top with a dollop of cement.
In the event of a leak, the traditional remedy adopted by the industry is the ‘perf and squeeze’ method, in which the casing is punctured from within and cement squeezed through the holes to reinforce the seal.
Yet, it’s a not a conclusive fix, and often needs to be repeated over the course of a well’s life in abandonment. The cumulative costs in doing so are far from cheap. Operators that don’t treat wells also risk failing in their environmental obligations.
That’s why the introduction of a new well-sealing technology could be the alternative the industry has long been crying out for. Developed by Interwell Norway, the technique uses thermite – more commonly used in the welding of railway track segments – which simulates the eruption of a volcano, creating artificial magma that fuses infrastructure to the surrounding rock.
Recently, the technology has been piloted in the Canadian provinces of British Columbia and Alberta, home to a number of onshore wells shown to be leaking methane. With commercialisation almost on the horizon, the next plan is to explore its potential in an offshore setting, as Michael Skjold, innovation and business manager at Interwell – and the technology’s inventor – tells Ross Davies.
How well do you really know your competitors?
Access the most comprehensive Company Profiles on the market, powered by GlobalData. Save hours of research. Gain competitive edge.
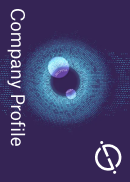
Thank you!
Your download email will arrive shortly
Not ready to buy yet? Download a free sample
We are confident about the unique quality of our Company Profiles. However, we want you to make the most beneficial decision for your business, so we offer a free sample that you can download by submitting the below form
By GlobalDataRoss Davies: How and when did you discover you were on to something with this new technology?
Michael Skjold: It was actually quite an easy discovery. About eight years ago, I was working for a large industrial service company [Baker Hughes] performing P&A operations in the traditional way with cement – which always seemed to me to be very time-consuming and expensive. Most worrying of all, the results were never 100%, and the wells always seemed to keep leaking.
It was the merger of several ideas. When I was a boy, I was always interested in volcanoes, dinosaurs, geology. Then one day, I saw this clip on YouTube about how they weld railway tracks using this chemical composition thermite. The composition includes aluminium and iron oxide – common materials to get hold of – and looks like floating magma or lava.
I started reading about igneous rock and how it affects the different formation types. That’s when the idea started to build inside me about whether I could actually create a man-made artificial magma solution.
The challenge was to apply an amount of energy at the correct depth and correct place in the well hole to be able to obtain a crystallisation process with the surrounding formation, creating 100% sealant efficiency.
RD: What are the benefits compared to traditional perf and squeeze solutions?
MS: I suppose we’ll only be able to see the benefits when the application has fully achieved proof-of-concept. It’s kind of divided into separate benefits depending on what kind of well it is – whether you are on onshore of offshore.
In Canada, where we have piloting the technology, there are lots of onshore wells with gas migration problems. This means the gas migrating from inside the casing cannot be solved easily with traditional methods.
But in our case, we do not have a defined borderline between our solution and the formation. It kind of mixes together. So this gas migration pathway is totally sealed off and locked. This means that you can create a barrier that actually lasts forever by only using E-line as an instrument.
RD: How expensive is this technology exactly?
MS: It’s very hard to say the price right now. It’s a question I’ve been asked a lot recently! We know we aren’t able to compete with traditional onshore requirements consisting of just one plug and eight metres of cement. That is so cheap, we don’t have a chance.
But in cases where there is vent flow and gas migration, in the long run we could potentially reduce the cost by at least 50%.
RD: How close are you to commercialisation?
MS: It’s in the final phase now. We have performed a total of five pilot wells with very promising results. Actually, it was during this verification period that we discovered this widespread problem of gas migration onshore in Canada. This led us into optimising the technical solution to solve these problems.
At the moment we are working together with super-majors out there on around 8-12 wells in order to get final proof-of-concept. We are also running a technology qualification process.
RD: What’s the potential for this technology to be deployed in an offshore environment?
MS: That’s actually the main goal. In my career, I’ve never actually been on an onshore well – my experience is only offshore. So my dream was to be able to perform this technology on subsea wells by only using a ship – using the rig only to drill holes.
Through this, you can also use a lighter vessel, reducing the technical challenges found today, as well as the very heavy and expensive operations that come with using a rig. You need circulation, too. It’s very demanding.
So our main target and goal for the project is to be able to perform offshore P&A through the use of an E-line only. That will reduce costs enormously.