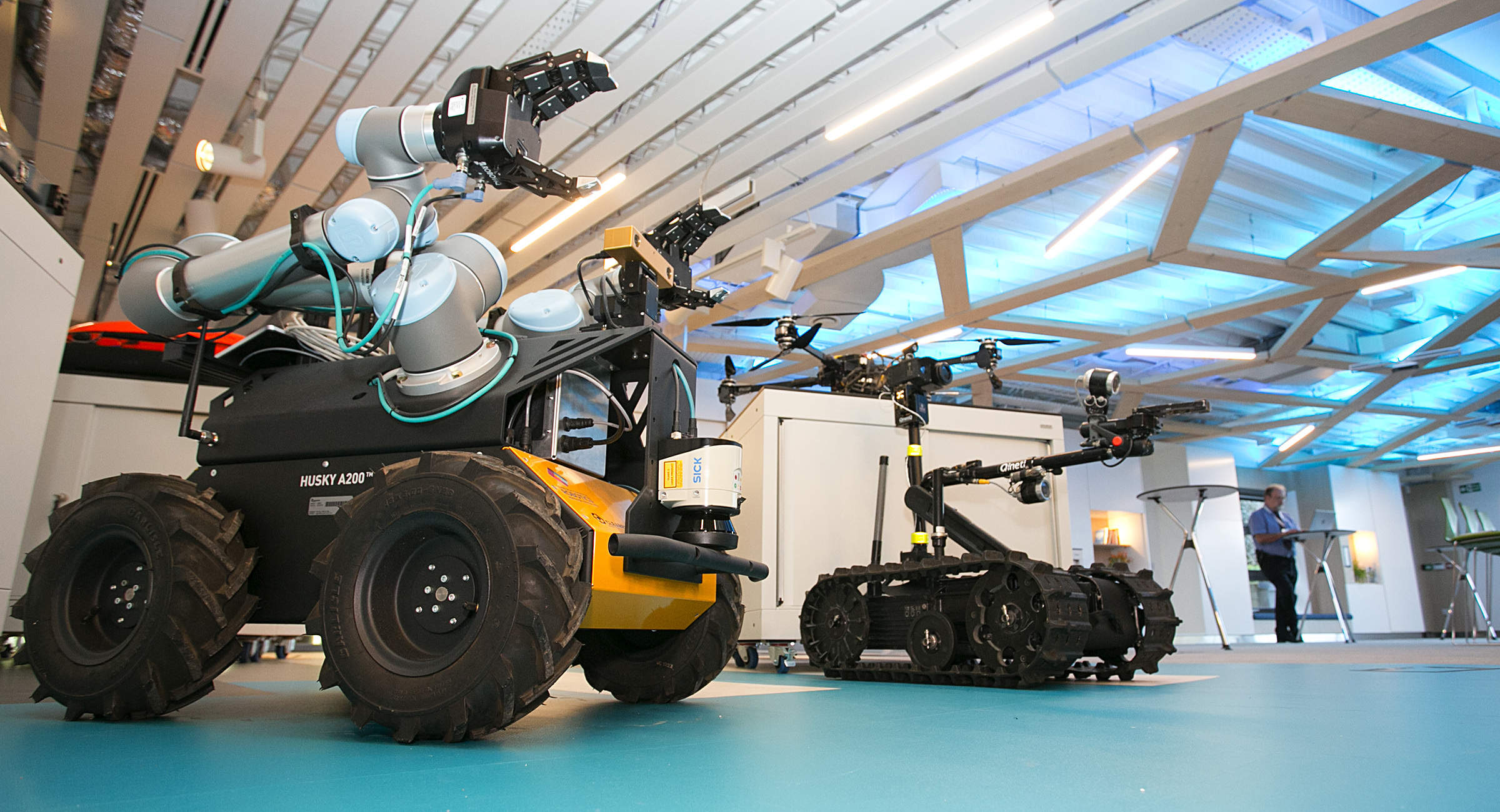
When it comes to assessing the condition of their process vessels and tanks, most North Sea operators traditionally use intrusive inspection techniques.
This commonly necessitates shutting down the platform and sending an engineer into the vessel to carry out a manual inspection. The method is far from ideal; resulting in lost production, platform shutdowns are costly – not to mention hazardous.
It is high time operators working on the UK Continental Shelf (UKCS) looked at newer, more innovative ways of vessel inspection, claims the Oil & Gas Technology Centre (OGTC). According to a recent survey by the Aberdeen-based group – alongside engineering group ABB – the adoption of non-intrusive inspection (NII) technology could deliver increased production and lower maintenance costs worth up to £242m per year to the UKCS.
Up to 80% of vessels currently operating in the North Sea could be examined using NII – without requiring a shutdown – claimed the study. Adoption of the available technology, however, remains low.
New ideas: The OGTC joins forces with Sonomatic and University of Strathclyde
The OGTC is looking to remedy the disappointing status quo concerning NII awareness. In April 2017, the group launched its first Asset Integrity ‘Call for Ideas’ initiative, which identified pressure vessel inspection as a “crucial challenge to maximising economic recovery from the UK Continental Shelf”.
In March, the centre announced it had invested in three robotics projects with inspection specialists Sonomatic and University of Strathclyde, aimed at transforming the inspection process.
How well do you really know your competitors?
Access the most comprehensive Company Profiles on the market, powered by GlobalData. Save hours of research. Gain competitive edge.
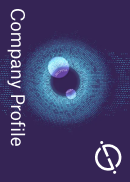
Thank you!
Your download email will arrive shortly
Not ready to buy yet? Download a free sample
We are confident about the unique quality of our Company Profiles. However, we want you to make the most beneficial decision for your business, so we offer a free sample that you can download by submitting the below form
By GlobalDataThe OGTC is working on two projects with the University of Strathclyde. The first is concerned with developing a new robot crawler, equipped with 3D laser scanning and non-destructive testing technology. The solution will construct a virtual, dynamic 3D representation of the inspection site, allowing for remote operation.
The second project with the university is focused on the use of drone swarms – as commonly used by the military, as well as for logistics activities – as a safer, more flexible and cost-effective alternative to human inspection.
The aim for Sonomatic is to develop “the next generation of robotic NII technology, with improved speed, agility and autonomy compared with existing systems”.
The benefits: Less disruption, lower costs and improved safety
“The application of robotics in offshore oil and gas is almost limitless, but as an industry we’ve only scratched the surface of what’s possible,” explains Rebecca Allison, asset integrity solution centre manager at the OGTC.
“Companies could reimagine their business processes and transform productivity. But this will only be possible if we understand the challenges and collaborate on the potential solutions.”
The OGTC and Sonomatic have worked together before. Last year the latter was one of the technology providers – along with Eddyfi and MISTRAS – involved in three NII trials jointly organised by the centre and Total E&P.
The trials, which took place on two process pressure vessels on Total’s Elgin Franklin platform – while the vessels were online and operating – revealed NII to deliver the same outcome as traditional intrusive methods (also tested as a benchmark), but without the costly shutdown and man entry into the vessels.
“NII allows vessels to be inspected in service,” says Mark Stone, Sonomatic’s integrity services manager.
“This means production is not disrupted. The cost of the inspection is also typically lower than cost of preparation and internal inspection. It also avoids man entry into vessels, meaning the major hazards of inspection are removed.”
So, what are the dangers facing engineers when it comes to traditional intrusive inspection techniques?
“There are significant risks associated with confined spaces and managing the hazardous substances encountered,” says Allison.
“That’s exposure to everything from naturally-occurring radioactive materials, to mercury and pyrophoric scale.”
“Confined space entry is one of the biggest risks in operation of pressure equipment, so operators want to avoid this,” adds Stone.
Limitless potential: What happens next?
The potential of robotics cannot be underestimated, believes Allison. It is an area of technology that carries the potential to not only make a traditionally burdensome task infinitely easier, but to better the general performance of an entire industry.
“Robotics has the potential to transform the offshore oil and gas industry,” she claims. “We have countless repetitive, dirty and potentially dangerous tasks carried out every day. Integrating robots for these tasks will help upskill our workforce and improve the quality of the jobs.
“Projects like this will help inspire and attract the next generation oil and gas workforce.
NII of process pressure vessels has a direct impact on maximising economic recovery. Every vessel is intrusively inspected, it has to be shutdown resulting in lost production. NII means the condition can be assessed while the vessel is online and operating.”
For Stone, the new project represents a vital opportunity for the offshore sector to capitalise on the “significant advances” in robotics technology over the last decade.
“The aim is to develop a scanning system for NII that will provide improvements in inspection speed – reduced time of inspection – and reduce manpower requirements to complete NII,” he says.
“The system developed represents the next generation of inspection technology, taking advantage of recent developments in automation, robotics, navigation and inspection capabilities.”
And it doesn’t just stop at pressure inspection.
This March also saw the launch of the OGTC’s second Asset Integrity ‘Call for Ideas’. The focus this time around will be on corrosion under insulation (CUI) – a problem that can be ascribed to over 20% of the major oil and gas incidents reported within the EU since 1984, says the OGTC. By the centre’s estimates, CUI costs the UK economy £28bn every year.