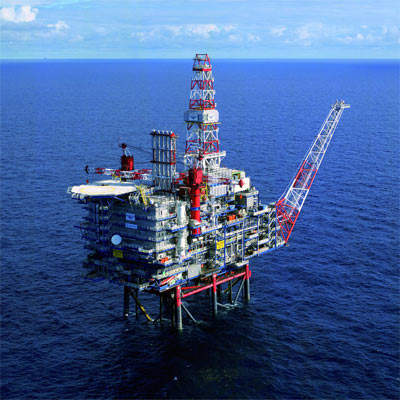
Sophisticated systems for the exploration and production (E&P) industry have led major operators to deploy many new real-time monitoring, surveillance and control systems, often at significant cost. Though these solutions are deployed at many stages of oil and gas field development, less attention has gone to asset operations where the greatest rewards may be found.
Shell E&P identified that properly-implemented ‘smart’ technologies, integrated with facilities’ daily operations, could greatly benefit this stage. The group developed its Fieldware Production Universe (PU) application for processing real-time signals from individual wells, through numerical, data-driven models, to devise three-phase flow estimates that are reconciled with total platform production.
These estimates change the traditional process of periodically routing well production to a test separator. With PU, individual well flow information is always available, so tests to validate or update PU models are performed only when necessary. A more advanced version – PU-RTO – uses models to support real-time production optimisation.
PU has become a fully-implemented and sustainable product, though only after lengthy and sometimes arduous development.
“Across the industry most operators can think of at least one system that has been rolled out, but not been fully adopted and has died before it delivered its full value,” says Carl Gerrard, production engineer of Shell’s real-time operations. “Reasons for failure are many, but often centre around support and delivery of true benefit to end users.”
Nevertheless, the success of Shell’s efforts is typified by PU’s application at the Nelson platform. Though challenging, this implementation helped Shell to refine PU and use it as a consistent element in its European operations.
CLOSING THE GAPS
Shell Global Solutions BV (SGS) developed the Fieldware Production Universe to address fundamental gaps in the management and surveillance of conventional oil and gas production. Measuring three-phase well flow, by routing to a test separator, normally takes many hours and may be performed weekly, monthly or even less frequently. Therefore, well production is extrapolated between tests, meaning issues causing deferment are not detected until the next test.
“Within our organisation several approaches have been used to predict three-phase flow,” comments Gerrard. “All were found to be difficult to sustain in an operating environment. PU was designed to overcome these sustainability issues.”
While well and test separator are connected, PU develops numerical, data-driven models linking individual well three-phase flow with signals from wellhead instrumentation, including tubing head pressures and temperature and lift gas data. PU uses complex algorithms, but has a simple graphical user interface for loading well test data, creating models and validating results.
A user with two or three days training can develop and maintain most models.
When the well is in production, wellhead data supports individual flow estimates. These are compared with total facility production, which crosschecks PU estimates. Algorithms can reconcile estimates with total measured production.
With continuous real-time, wellhead and production data, constant and real-time production estimates are available. PU essentially provides a virtual three-phase meter for each well and can indicate when models require updating.
Data-driven models – crucial to the sustainable use of PU – have many advantages. The numerical relationship between wellhead and flow includes calibration errors in wellhead instruments. Repeatable well measurements are required and accuracy is not critical within certain limits.
To provide redundancy against instrument failures, independent models are created for each well using different inputs, which provide fallback models if individual instruments fail. The potential for data-driven models to optimise gas-lifted wells seems to be substantial.
PU IN PRACTICE
Throughout Shell, PU has been implemented on over 70 offshore and onshore assets. Often, it has accelerated production and reduced deferment. The overall programme is a success, with further implementations planned.
PU data-driven models, estimating real-time wellflow, can help generate estimates of well production for given values of commonly-manipulated well production variables, such as production choke position, lift gas injection rates and header pressure. These models can help choke or lift gas set points for maximum production, recognising possible constraints to optimise individual wells.
Often, surface production system constraints, including: gross liquid-handling capacity of the production separator, produced water system and gas lift compression capabilities, restrict an integrated production facility’s capacity. Optimisation opportunities, including maximising net oil production with limited lift gas, exist within these constraints.
PU uses production system constraints, alongside data-driven models, to compute optimum well choke or lift gas settings. Where the same header links multiple wells, header pressure interactions between wells can influence individual well production. These are included in the standard non-linear, steepest ascent optimisation algorithms to compute optimal settings, along with various heuristic methods to validate the solution.
As with many optimisation systems, set points can be entered manually into the control system, or delivered through a middleware layer like the process historian. Optimisation models can be automatically updated by inserting perturbations into set points.
The business case for implementing new technology is often stronger on greenfield projects, though Shell E&P has many brownfield assets, such as the Nelson Platform, built in 1994, which became a Shell asset in 2002. It lies 200km north of Aberdeen, Scotland and produces approximately 6,000m³ of oil and 450kSm³ of gas each day from 33 platform wells, which produce from the same reservoir through two subsea tiebacks. All platform wells use gas-lifting to assist production. Some 60% of gas produced is used to power the platform.
The platform operates a distributed control system (DCS) and over 6,000 key process variables are stored onshore in a process historian, which receives data at one value a minute – commonly called ‘real-time’. Onshore staff use the process historian extensively for well and platform surveillance, but the system is rarely used by offshore staff.
PU was installed by SGS at Nelson in 2005, following use by onshore teams for surveillance and optimisation. The PU interfaces with the process historian, reading historical data and delivering current wellflow and other diagnostic data.
The process historian – familiar and widely used throughout Shell’s business – also receives daily well and production data automatically through emails from key onshore and offshore recipients.
Combining an established crew with familiar working patterns, an ‘adequately-functioning’ spreadsheet system and a new product, unproven in an operating environment, naturally generated some concern. From the outset it was clear that implementation would only succeed if it met all the platform’s needs, benefited end-users onshore and offshore and boosted production.
Gas lift optimisation on Nelson had evolved gradually, involving many users and data flows, though users were only aware of their individual parts in the overall process. A lack of formal control documentation also meant different shifts approached optimisation differently.
To fully understand the process, key staff – including control room operators from both shifts – were brought together to map existing process workflows and the functionality of the new optimiser, resulting in a new workflow for PU-RTO. This new workflow revealed that offshore operators initiate short-term optimisations. If necessary they can manually control wells by using DCS to tackle issues such as slugging.
“PU detects manually-controlled wells and the gas they use is subtracted from that available for optimised wells,” notes Gerrard. “Onshore petroleum engineers determine the models and rules for optimisation from the relevant data – all held centrally on the PU server. All optimisation data is obtained from the process historian, which also sends optimal set points to the DCS. There is no manual DCS data entry.”
GAS LIFT OPTIMISATION
Formation gas from Nelson’s wells is compressed on the platform and supplied to a common distribution manifold. Each well has a gas lift flow transmitter and control valve, while a DCS control loop regulates flows to a set point.
Many factors affect the relationship of produced net oil to injected gas lift, which differs for each well. Onshore or offshore staff may change limits daily, such as valve constraints.
Available gas lift depends on compressor capacity. The combined maximum limits on individual wells generally exceeds the available lift gas.
Optimal distribution of lift gas maximises net oil production. As conditions change, this optimisation needs to be frequently recalculated and the changes applied to well gas lift rates.
For many years lift gas distribution was calculated using a system of physical well models and independent optimisation programmes. Data was entered manually from the Nelson control room into a PC spreadsheet. Gas lift set points were also keyed manually. Onshore staff updated well models, operating constraints and optimisation algorithms.
One key benefit was that optimisation lay in the hands of readily-available offshore operations staff. The disadvantages were long system cycle times and the low priority of optimisation during busy periods. Onerous onshore maintenance of underlying models also caused delays and inaccuracy.
A study in 2005 concluded that optimising gas lift was a key variable affecting the time needed to return a well to full production after shutdown. The spreadsheet solution had limited version control that caused operational errors. Across the industry, initial gains from new systems decreased in implementation as they were not embedded into daily operations and Nelson’s spreadsheet has faced a similar fate.
PU-RTO IMPLEMENTATION
Implementing PU-RTO necessitated many technical changes and altered the way work was executed on the platform. Technically, the biggest change was the sending of gas lift set points to the DCS from an office computer. Historically, the remoteness of offshore platforms isolated the offshore control system from onshore IT systems. Bandwidth has improved recently, so PC users on Nelson have similar connection speeds to office users. This connectivity is key to enabling applications like PU, but brings its own security and integrity risks.
For many years, data flowed only from Nelson DCS to the process historian and office PCs. Sending gas lift set points from ‘the office’ back to the DCS was new territory. A detailed assessment examined risks in the IT connection and the underlying business processes. It also documented the consequences of incorrect set point data reaching gas lift controllers or failed set point transmission.
“With existing protection systems on the platform we concluded that the direct sending of gas lift set points to the DCS does not constitute a risk to the platform’s safety or integrity,” says Gerrard. “However, an unacceptably high risk of process disturbance, well damage and production loss does exist. To mitigate this, changes require final review and acceptance by the control room operator on the DCS.”
Feedback from onshore and offshore PU-RTO users has been positive since go-live in 2006.
Offshore crews seldom require remote support and rapidly fix occasional maintenance issues, such as gas lift transmitter failure, with minimal onshore intervention.
A key business driver for PU-RTO was how quickly a platform could be restarted after a ‘trip’. Since implementation, many trips have occurred with the fastest restart time 75% of the previous average. Ongoing operational changes mean Shell cannot yet confirm it, however, PU-RTO is believed to have changed distribution of gas to individual wells and increased total platform production.
Real-time optimisation has great potential, but demands E&P companies engage early in the implementation and embrace new ways of working.