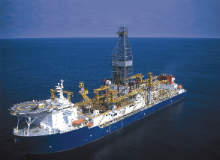
When oil prices started to rapidly decline in 2014, few in the offshore industry expressed the view – at least in public – that a ‘new normal’ was here. But as 2015 dragged on and prices refused to budge, it became increasingly apparent that a new paradigm had emerged and that a more efficient, less expensive operational model was needed to deal with it.
One area calling out for a new approach is the maintenance of offshore vessels. Unplanned downtime, generally caused by the failure of money line equipment, is more common than most would care to admit and when such failures do occur, it can be hard to get the right diagnosis and spare parts in a timely manner.
On the other side of the coin there is unnecessary maintenance, interventions that are carried out in line with a scheduled maintenance plan but have no positive effect. For example, a semi-submersible ship might have eight generators but most of them are hardly used, so applying equal effort to maintaining all of them is a waste of time and money. Scheduled maintenance can even cause unintended harm.
"Every time you maintain something, you are more likely to introduce an error than if you actually left it in its normal state," explains Andy McKeran, digital marine leader at GE Marine. "One example is a bearing. If you stick a rotating machine down and change a bearing you’ve got just as much chance of introducing a problem than if you left the bearing alone and just monitored the temperate of the oil, the temperature of the machine and its vibrations."
Therein lies the core principle behind SeaStream Insight, a technology unveiled by GE Marine at the Offshore Technology Conference in Houston in May. SeaStream collects data from various parts of a drilling vessel using a network of monitors. This data can relate to a range of factors, which affect component performance, from temperature and vibration readings to the number of times a valve has opened and closed in a specified period. The data is then processed, organised and relayed wirelessly to the drilling contractor, original equipment manufacturer (OEM) and whoever else has a stake, giving real-time visibility over the state of the asset and allowing problems to be resolved, often remotely, in a timely manner. By combining previously separate sources of data, the technology gives an overall picture of asset performance that was previously lacking.
How well do you really know your competitors?
Access the most comprehensive Company Profiles on the market, powered by GlobalData. Save hours of research. Gain competitive edge.
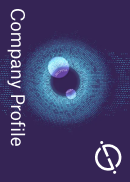
Thank you!
Your download email will arrive shortly
Not ready to buy yet? Download a free sample
We are confident about the unique quality of our Company Profiles. However, we want you to make the most beneficial decision for your business, so we offer a free sample that you can download by submitting the below form
By GlobalData"[An existing limitation] onboard these vessels was inadequate visibility of asset health," says McKeran. "You’ve got the drilling system, the power management system, the dynamic positioning and the mud logger and these systems don’t actually talk to each other. For example, you might be trying to analyse slip-to-slip connection time to [help you monitor] your drilling productivity, but you don’t have visibility into what the weather was doing at that time. It could be a significant associated affect [on the quality of data you collect]."
Fresh from the GE store
This technology was not designed specifically for the offshore drilling environment. In fact, GE has been employing it to monitor power plant, renewables installations and onshore power facilities for a few years. But in a traditionally conservative industry, such as the offshore game, the introduction of SeaStream Insight represents a notable change in the way it puts data and IT at the centre of vessel maintenance and operation.
An interesting example of this is in the way SeaStream employs predictive analytics – identifying potential problems and acting to stop them becoming real ones. Traditionally offshore operators have done this by creating physics-based models, painstakingly constructed simulations of a particular vessel that you can use to test different operational scenarios. SeaStream instead uses a tool called Smart Signal. As it’s completely based on the analysis of data points, it doesn’t require any prior modelling or even knowledge of the vessel’s physical properties. It collects data points (tens of thousands, if a high level of granularity is required) and creates a ‘digital twin’, a virtual representation of the vessel, against which data from the real-life vessel can be compared.
"The concept is to create a software driven model and then monitor the "as is" state against it over a period of time," McKeran explains. "We currently monitor over 15,000 assets globally using smart signal, of which around one third are not GE assets. The beauty of smart signal is that it becomes OEM-agnostic, whereas with a physics-based tool you often have to be the original equipment manufacturer to design that tool. If your design then changes from vessel to vessel, you have to redo you model, whereas with data-driven models you are just looking for the same type of inputs from asset to asset."
Big data fears unjustified
Mention employing big data analytics in the offshore environment and a few common fears arise. Isn’t a huge amount of processing power needed to crunch the data? And how can you derive real, relevant meaning from the masses of data you crunch?
The first fear has been made largely unfounded by technology. In McKeran’s estimation, three years of data on drill-floor application takes up 3-4tb, as much as the storage capacity of some personal computers. On the second point he believes the most important initial step will be breaking the data down into segments based on what is relevant to whom: reliability data, which goes back to OEMs, operational data, for use by drilling contractors and contract data, which oil companies can use to demonstrate that they are meeting their contractual obligations.
With finance departments looking for ways to reduce operating expenditure, it’s little surprise that many in the industry are quickly coming around to McKeran’s way of thinking.
"We are noticing that conventional asset vice-presidents are being joined at the decision-making table by CIOs and CTO’s," he says. "Our industry has been relatively risk averse and that CIO’s are getting involved shows that the benefits are exceptionally clear. You are not looking at massive re-instrumenting of vessels, so it lends itself to a retrofit-type market where you have to look at your associated opex budgets. But it’s also for new builds – it will help people change the way we design vessels."