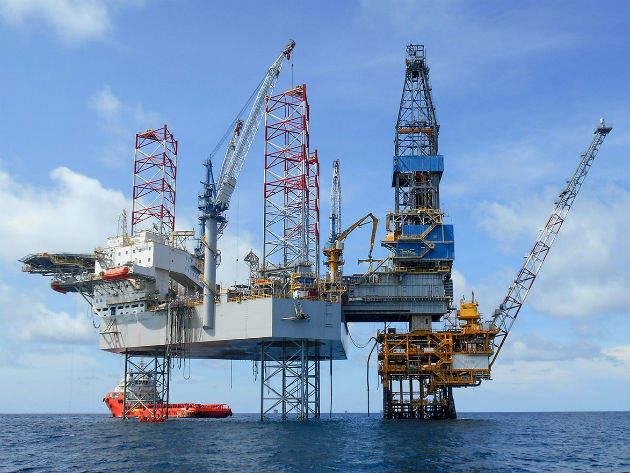
In today’s challenging business environment, cutting expenditure is crucial for the offshore sector. According to a recent report by Oil & Gas UK total expenditure on the UK Continental Shelf fell from a peak of over £26bn in 2014 to £17.2bn in 2016.
How well do you really know your competitors?
Access the most comprehensive Company Profiles on the market, powered by GlobalData. Save hours of research. Gain competitive edge.
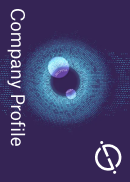
Thank you!
Your download email will arrive shortly
Not ready to buy yet? Download a free sample
We are confident about the unique quality of our Company Profiles. However, we want you to make the most beneficial decision for your business, so we offer a free sample that you can download by submitting the below form
By GlobalData“We are living in a relatively uncertain environment at the moment in the offshore oil and gas industry,” says Andrew McKeran, marine executive at General Electric’s Marine Solutions. “There is oil price volatility and there is an expertise imbalance which has resulted in performance variability and variance.
“There are also other, longer running problems. Companies often face difficulties when it comes to troubleshooting because of the very nature of the offshore industry. And then we are seeing a lot of unplanned downtime and maintenance costs. This is no longer acceptable to the industry because of oil price instability and the drop in day rates that some of our partners and clients are now experiencing.”
Improving the operational productivity of drilling rigs is one way the industry can help tackle these problems. In March, GE and Noble Corporation announced plans to work on an advanced data analytics system for offshore drilling rigs called the Digital Rig.
Utilising the industrial cloud
For the project GE will draw upon its experience in both software and industry. “Before starting we took a step back to look at what we already have within the GE store that might be useful,” McKeran says. “We looked at the power business, the onshore oil and gas business, aviation and so forth.
“We also decided to look at our industrial cloud-based platform Predix, which offers us the ability to run analytics at scale. Of course, there are some limitations when you are dealing with the offshore business: the asset is not connected to a cloud in any way, shape or form, for example. That means you have to bring in the nuance of running analytics on the edge, and then using the minimal bandwidth connections that you have from the platform back to the shore.”
Real-time data
To create enhanced drilling process efficiencies, GE is looking to build new performance indicators. “This entails producing efficiency reports,” McKeran explains. “It is effectively about asking: how well did we drill? It is about looking at your well plan and comparing it with what you have actually done over the past 24 hours.
“What we are offering here will be different from other systems that are out there. We will be doing it on board the vessel in near real time, rather than sending the information to the beach, having it processed and then sending it 24 hours later. Our philosophy here is that if you can get that information in near real time, you can avoid an operational disruption that may come 24 to 48 hours later or in a week’s time.”
GE is also looking to improve the drilling process through performance analytics which can predict deviations and forecast potential disruptions on-board the vessel.
“The idea is to reduce operational disruptions,” says McKeran. “For this what we have is zonal analytics, which is split into two elements: high-frequency signature analysis on drive systems and looking at usage intensity on some of the assets that are on-board the vessel.”
Predictive maintenance
Some information will be sent to the shore, McKeran adds. “Having created those zonal analytics on the vessel we will send information back for predictive analytics so that we can look at look-term pattern behaviours,” he says.
“We will feed the information into a cloud-type environment and will start running what we call smart signal. The idea is to offer somewhere between three weeks’ and three months’ notification for any pending issues. We will be looking for underlying patterns and deviations very early on. We can pick up things like potential vibration issues, temperature issues and so on weeks before they are picked up on an automation system.”
This part of the Digital Rig will make use of GE’s digital twin concept, where like-for-like digital representations of physical systems are created to help companies understand, predict and optimise the performance of their assets.
“Here we are looking at effectively modelling an asset,” says McKeran. “What we do is take from our standard library of assets and build a blueprint, a basic understanding of how that asset is literally, mechanically and electrically coupled together. This will be done shore-side either in the cloud or in an industrial performance and reliability centre within GE.”
For McKeran the shift to predictive maintenance will have a big impact on the industry. “We are looking to transform and redefine maintenance strategies by moving away from traditional OEM, calendar-based maintenance and towards a long-term, sustainable, adaptive philosophy of cost reduction for maintenance on board the vessel.”
While the partnership between GE and Noble was only recently announced, McKeran says work began in the first quarter of this year and progress is already being made.
“We have already delivered what we call ‘the data mile’ where we utilise a centralised historian and start looking at harmonising data across the vessel,” he says. “Progress is very fast and both companies are looking to accelerate the time to value to prove its effectiveness.”