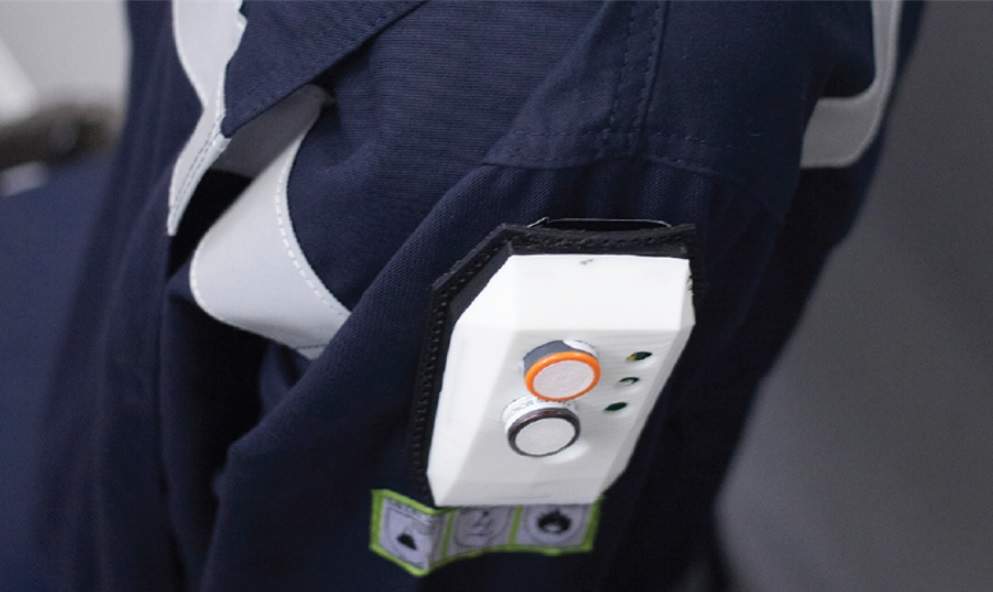
Offshore oil and gas platforms are affected by a number of hazards, from gas leaks to extreme weather, and operators have been working for decades to ensure every safety precaution is taken. Now the internet of things (IoT) is offering a new option in the form of wearable safety technologies.
“The direction many companies are following points towards a digitalisation of the workplace, in order to reduce human errors, increase safety and simplify work processes,” explains MIT Design Lab senior design lead Sara Colombo. “Definitely there is much space for the adoption of IoT and connected solutions, and companies need to fully embrace this revolution and to train workers to make them ready to adopt these solutions even further.”
IoT wearables have already begun to play an important role in the digitalisation push across a number of industries. But the unique challenges involved in working offshore mean adoption has been slow in the oil and gas sector.
MIT’s Safety++ project may be one of the contenders to change this, however, with its new range of energy industry-ready wearables. Elsewhere, proven technologies such as SmartCap are expanding from their original applications with the potential to enhance safety offshore by applying hard-won lessons learned in other industries.
Tackling fatigue with SmartCap
The SmartCap was originally designed for use in the mining industry, where shift work and long hours made fatigue a key safety concern, as it is in the offshore sector. The company was formed to build a predictive technology to counter this risk during the early days of wearables.
Now available as a band that can be clipped inside a number of headwear alternatives, the SmartCap provides an early warning system for fatigue. “The product measures brain activity, sometimes referred to as EEG,” says SmartCap Technologies CTO Daniel Bongers. “The brain activity is translated via a proprietary machine-learnt algorithm to a number. That number is representative of the risk of falling asleep unintentionally.”
How well do you really know your competitors?
Access the most comprehensive Company Profiles on the market, powered by GlobalData. Save hours of research. Gain competitive edge.
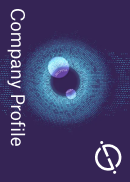
Thank you!
Your download email will arrive shortly
Not ready to buy yet? Download a free sample
We are confident about the unique quality of our Company Profiles. However, we want you to make the most beneficial decision for your business, so we offer a free sample that you can download by submitting the below form
By GlobalDataThis information can be displayed on a screen for the individual worker, and communicated with a central server. This allows the fatigue of all workers to be assessed, which is a useful tool in improving health and safety. It also becomes possible to recognise fatigue patterns, enabling broader operational solutions.
The original SmartCap was hardware-intensive, making it difficult to apply in industries other than mining because of the limitations to movement and the increased price. “Our new solution, the Life SmartCap, is a lightweight wearable which takes advantage of low-energy Bluetooth,” says Bongers. “This means it communicates much more universally with smart phones and industrial tablets, and so being less hardware-intensive, the cost has come down.”
Fatigue can affect workers in all industries, but when working on a platform in the middle of the ocean, one sleepy mistake can have serious consequences. Therefore, a technology that helps combat fatigue and allows a company to keep a sharper eye on the health of its staff certainly offers operational benefits.
MIT Safety++ products
MIT launched an IoT wearables project, Awearness, in 2015 as part of a collaboration between Italian oil major Eni and the MIT Mobile Experience Laboratory. The team has produced an outfit of wearables designed for the energy industry.
“We designed Safety++, an ecosystem of connected objects that collects data from the workers and the environment through wearable sensors and makes them readable and available in real time,” says Colombo.
An undershirt was designed as an easy and non-intrusive item for monitoring biological data using 16 points of haptic feedback. It includes lung expansion sensors, ECG sensors, galvanic skin response sensors and a flexure sensor. A central sensor on the upper back of the vest can transmit the data, and works together with the environmental data from the Jacket++.
The team designed the jacket with sensors on either arm that can monitor noise, air quality and smoke and detect multiple dangerous chemicals. Working on oil and gas platforms, or within a refinery, can expose workers to a number of potentially damaging chemicals including toxic vapours that are often invisible and odourless. By using sensors, harmful gases can be immediately identified, and proper safety steps taken.
The outfit comes with a carabiner to protect against falls, and shoes. “The shoes we designed embed a pressure sensor and a vibration motor as a feedback medium,” says Colombo. “When the worker lifts excessive loads, the shoes vibrate and alert the user that the load that he is trying to carry is above the recommended weight.”
MIT has already begun testing the products in the energy sector, with a number of successful trials in power plants. Expansion into the offshore oil and gas sector is something the lab is already planning to look into in the future.
“[The wearables] have been designed to cover a number of possible scenarios in the oil and gas industry in general,” says Colombo. “For instance, the man down situation, which is connected to the problem of lone workers, is an issue experienced in offshore plants. Being able to monitor vital signs would be beneficial for offshore workers.”
Smart glasses
BP has already begun using IoT wearables in some areas of its operations, such as onshore gas sites. The company’s smart glasses use augmented reality to overlay data and instructions over the worker’s field of vision. They are also able to present sensor information on the lens and communicate this information with a central communication hub.
In 2016, BP’s Digital Innovation Organisation technology principal Blaine Tookey spoke at the Wearables Technology Show about the potential for IoT wearables in the offshore oil and gas sector.
“This is the revolution we’re looking for: the new paradigm that wearables will bring to people working in oil and gas,” said Tookey. “This technology will drive automatic situational awareness, so our field workers will have the right knowledge at the point of work. Enabling a ‘man down’ to be automatically recognised by colleagues and the control room and location sensing will be really valuable.”
Tookey highlighted a range of products he would like to see developed further for the offshore oil and gas industry. These included smart sensors, displays and communication devices that could all be integrated into wearables.
With the current success of the smart glasses in other areas of BP, it is likely that they will make an appearance in the offshore industry where up-to-date information could be invaluable. However, the glasses would need to be modified to work in the wet and windy offshore environment.
Moving beyond wearables
All of the products have faced challenges in development, but still greater problems with adoption. “There are often challenges to do with resistance because this can be seen as some sort of big brother initiative and therefore it’s highly critical that the wearable be comfortable, effective and well understood,” says Bongers.
This is something Colombo touched on as well, saying: “The main problem with this kind of connected and monitoring systems is users’ fear of ‘being watched’ or ‘controlled’.” Despite the obvious safety benefits therefore, the technology may face hurdles gaining traction in the offshore sector.
The industry remains confident that the benefits will win out, and wearables will become the norm. According to Colombo, the technology could even go beyond wearables, to ensure complete monitoring.
“In research, we are witnessing a change in paradigm from ‘wearable’ to ‘embodied’ IoT solutions,” she says. “Augmenting our own body with sensors and actuators is what’s next. But this is just in an early stage of research, and companies, especially in the energy field, tend to have a much more conservative approach to innovation. So, we will not see any embodied technology augmenting workers’ perceptions or actions in the next decade, but we hope to see more connected protective equipment and wearable systems in the next few years in the energy plants of tomorrow.”