Reutilising existing oil and gas infrastructure can lead to a more cost-efficient energy transition. Some parts of the currently installed infrastructure perform functions that will remain critical for some time, even in a fast pace transitioning world.
As stated by the UK Waste and Resources Strategy: “A more circular economy will see us keeping resources in use if possible, so we extract maximum value from them. We should recover and regenerate products and materials whenever we can, giving them a new lease of life.”
Although repurposing infrastructure is the main target, it also requires careful planning as a premature retirement could ultimately have negative consequences for energy security.
Upstream infrastructure retrofitting – carbon dioxide injection
The main types of carbon dioxide (CO₂) storage projects associated with oil and gas formations and infrastructure are those involved in enhanced oil recovery (EOR) and geological storage. The first one is used to increase the ability of the oil to flow to a well which, in the case of CO₂ injection, occurs by reducing its viscosity. Moreover, EOR projects can be later easily converted for permanent CO₂ storage. The second case involves injecting the CO₂ into the formation for its permanent storage without the expectancy of recovering any additional crude oil.
When adapting the upstream infrastructure for CO₂ injection, the GlobalData webinar report identified key technical factors to consider for being successful.
Midstream infrastructure retrofitting – hydrogen transport
Compared to natural gas, transporting hydrogen at the same pressure requires three times the volume needed to keep the energy flow constant. Considering the flow requirements, approximately 10% of the existing compressors can generally continue to operate without any changes. For 40% of the compressors, some accessories as the impellers, feedback stages, and gears might need adjustments, with the remaining 40%-50% of compressors requiring replacement.
How well do you really know your competitors?
Access the most comprehensive Company Profiles on the market, powered by GlobalData. Save hours of research. Gain competitive edge.
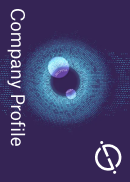
Thank you!
Your download email will arrive shortly
Not ready to buy yet? Download a free sample
We are confident about the unique quality of our Company Profiles. However, we want you to make the most beneficial decision for your business, so we offer a free sample that you can download by submitting the below form
By GlobalDataAnother factor that influences the eligibility of a pipeline for its reuse is the hydrogen production method. Steam methane reformate (SMR) or auto thermal reformate (ATR) production methods, compared to the electrolysis scenario, fit better due to their linking to the current gas infrastructure. Considering this, it is estimated that 25%-40% of the onshore pipelines can be reused, while in the case of offshore, the length reuse range is reduced to 2%-25% due to the inexistence of an offshore pipeline code covering hydrogen transport.
A GlobalData webinar report has shown that, over three selected case studies, huge savings can be achieved by retrofitting a pipeline for hydrogen transport.
Midstream infrastructure retrofitting – carbon dioxide transport
Pipeline retrofitting can facilitate carbon capture and storage (CCS) initiatives. The most suitable options for long-term storage of CO₂ in depleted reservoirs are EOR or geological storage projects. These projects involve the transportation and injection of CO₂ in its dense phase, for which a minimum of 70% of the offshore pipeline length is eligible for reuse due to its high maximum allowable operating pressure (MAOP) in Europe. However, for onshore pipelines, a minimum of 20% of the length is applicable for CO₂ transport in its dense phase.
As the GlobalData webinar report detailed, over three case studies, the savings associated with repurposing a pipeline for CO₂ transport would significantly vary between onshore and offshore pipelines.
Downstream infrastructure retrofitting: crude refineries conversion/co-processing of renewable fuels and biofuels
The use of renewable fuels is crucial in decreasing greenhouse gas emissions as these leave a lower carbon footprint compared to petroleum-based fuels. Producing these reduces the countries’ reliance on imported fuels, thus diversifying their energy supply. Adapting an existing crude refinery to produce renewable fuels can also enhance its economic performance by increasing its product variety, making it more reliant on economic shocks such as rising oil prices.
The production of renewable fuels such as renewable diesel and sustainable aviation fuel involves the hydro treatment of feedstocks, which requires the modification of traditional crude refinery operations and equipment. However, repurposing a refinery to process these biogenic feedstocks is a novel process involving a steep learning curve. Also, operational experience has shown that unlikely crude oil pipeline transport, biogenic feedstocks are delivered via rail, truck, or barge. Consequently, if the feedstocks are of different grades, their supply size, frequency, and storage must be considered.
Repurposing a refinery to produce biofuels generally requires a low investment with few adaptations and infrastructure requirements, as processing vegetable oil or animal fats processing it’s a known process. However, if biofuel production involves bio-oil pyrolysis of biomass, a substantial investment is usually involved. According to the GlobalData webinar report, by 2030, standalone renewable refineries capacity worldwide will exceed co-processing and converted crude refineries capacity, mainly due to the technical difficulties involved in repurposing these to produce renewable fuels and biofuels.